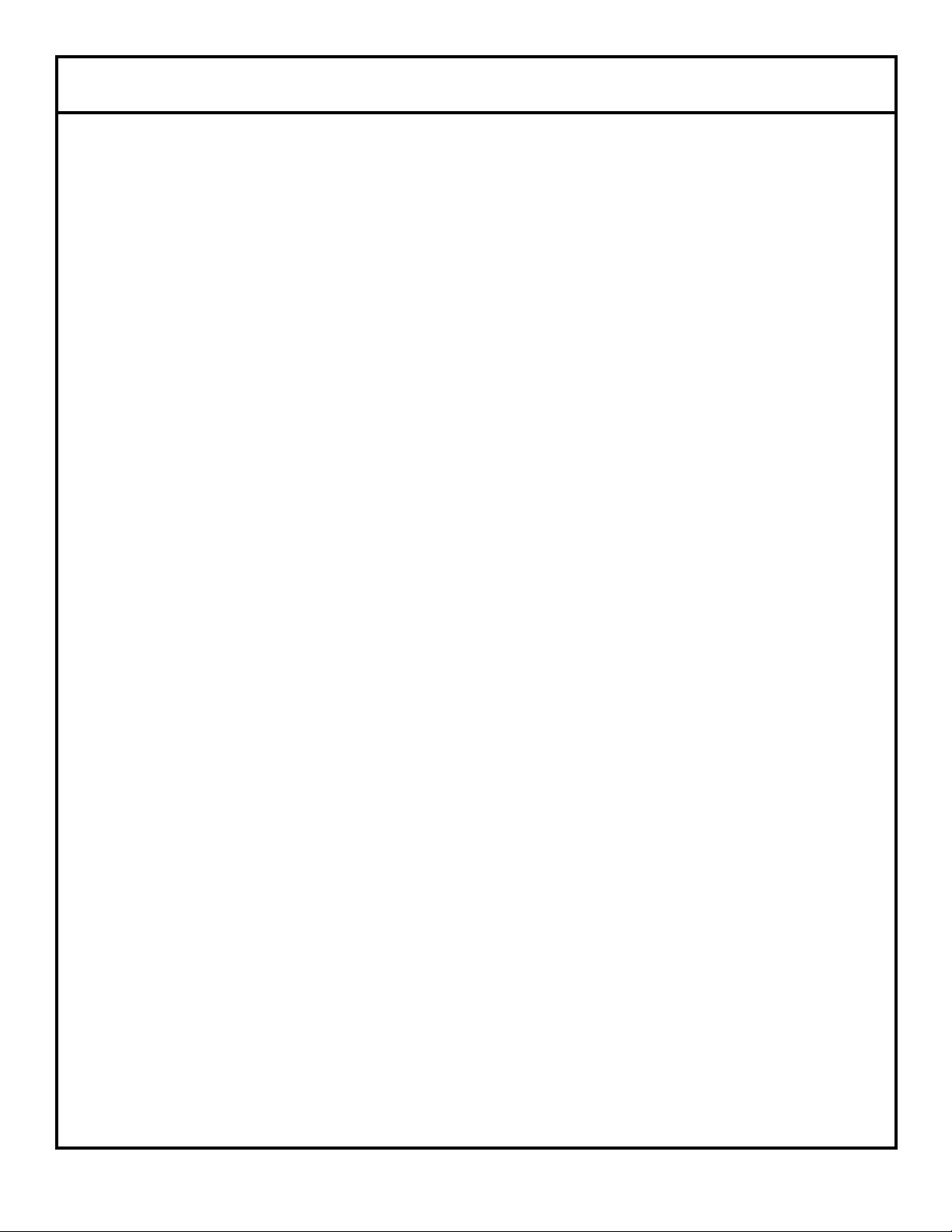
SAE J1979 Revised APR2002
-3-
5.4 Service $04 - Clear/Reset Emission-Related Diagnostic Information ..................................................... 37
5.4.1 Functional Description ............................................................................................................................37
5.4.2 Message Data Bytes ...............................................................................................................................37
5.4.3 Parameter Definition ...............................................................................................................................37
5.4.4 Message Example ..................................................................................................................................37
5.5 Service $05 - Request Oxygen Sensor Monitoring Test Results............................................................ 39
5.5.1 Functional Description ............................................................................................................................39
5.5.2 Message Data Bytes ...............................................................................................................................39
5.5.3 Parameter Definition ...............................................................................................................................40
5.5.4 Message Example ..................................................................................................................................41
5.6 Service $06 - Request On-Board Monitoring Test Results for Specific Monitored Systems .................. 43
5.6.1 Functional Description ............................................................................................................................43
5.6.2 Message Data Bytes ...............................................................................................................................43
5.6.3 Parameter Definition ...............................................................................................................................44
5.6.4 Message Example ..................................................................................................................................45
5.7 Service $07 - Request Emission-Related Diagnostic Trouble Codes Detected
During Current or Last Completed Driving Cycle .................................................................................... 47
5.7.1 Functional Description ............................................................................................................................47
5.7.2 Message Data Bytes ...............................................................................................................................47
5.7.3 Parameter Definition ...............................................................................................................................48
5.7.4 Message Example ..................................................................................................................................48
5.8 Service $08 - Request Control of On-Board System, Test or Component ............................................. 48
5.8.1 Functional Description ............................................................................................................................48
5.8.2 Message Data Bytes ...............................................................................................................................48
5.8.3 Parameter Definition ...............................................................................................................................50
5.8.4 Message Example ..................................................................................................................................50
5.9 Service $09 - Request Vehicle Information ............................................................................................ 51
5.9.1 Functional Description ............................................................................................................................51
5.9.2 Message Data Bytes ...............................................................................................................................51
5.9.3 Parameter Definition ...............................................................................................................................52
5.9.4 Message Example ..................................................................................................................................53
6. Diagnostic Service Definition for ISO 15765-4 ....................................................................................... 63
6.1 Service $01 - Request Current Powertrain Diagnostic Data ................................................................... 63
6.1.1 Functional Description ............................................................................................................................63
6.1.2 Message Data Bytes ...............................................................................................................................63
6.1.3 Parameter Definition ...............................................................................................................................65
6.1.4 Message Example ..................................................................................................................................65
6.2 Service $02 - Request Powertrain Freeze Frame Data.......................................................................... 69
6.2.1 Functional Description ............................................................................................................................69
6.2.2 Message Data Bytes ...............................................................................................................................69
6.2.3 Parameter Definition ...............................................................................................................................71
6.2.4 Message Example ..................................................................................................................................71
6.3 Service $03 - Request Emission-Related Diagnostic Trouble Codes ..................................................... 74
6.3.1 Functional Description ............................................................................................................................74
6.3.2 Message Data Bytes ...............................................................................................................................74
6.3.3 Parameter Definition ...............................................................................................................................75
6.3.4 Message Example ..................................................................................................................................75
6.4 Service $04 - Clear/Reset Emission-Related Diagnostic Information ..................................................... 76
6.4.1 Functional Description ............................................................................................................................76
6.4.2 Message Data Bytes ...............................................................................................................................76
6.4.3 Parameter Definition ...............................................................................................................................77
6.4.4 Message Example ..................................................................................................................................77
6.5 Service $05 - Request Oxygen Sensor Monitoring Test Results............................................................ 78