ESD-TR3.0-01 ESD-TR3-v2.0-01-02测量电离器偏移电压和放电时间的替代技术.docx
2.虚拟产品一经售出概不退款(资源遇到问题,请及时私信上传者)
### ESD-TR3.0-01 ESD-TR3-v2.0-01-02 测量电离器偏移电压和放电时间的替代技术 #### 标题解读 “ESD-TR3.0-01 ESD-TR3-v2.0-01-02 测量电离器偏移电压和放电时间的替代技术”这一标题主要介绍了关于静电释放(Electrostatic Discharge,简称ESD)领域的一项技术报告,该报告详细讨论了用于测量电离器偏移电压和放电时间的新方法。 #### 描述解读 文档的描述部分简要重申了标题中的内容,进一步强调了这份技术文档的主要研究方向是关于电离器偏移电压与放电时间的测量技术。 #### 知识点详解 ##### 1. 静电释放(ESD)与电离器 - **静电释放(ESD)**:在半导体制造、硬盘驱动器、平板显示等高精密电子产品生产过程中,静电控制至关重要。静电是一种常见的现象,但在某些敏感设备中,即使是微小的静电释放也可能会导致产品损坏或性能下降。 - **电离器**:一种用来中和静电荷的设备,通过产生正负离子来平衡环境中的电荷分布,从而降低静电释放的风险。 ##### 2. 偏移电压与放电时间的概念 - **偏移电压**:指的是电离器产生的电压与其期望值之间的差异。理想情况下,电离器应提供一个中性化的电场环境,但实际应用中往往存在一定的偏差。 - **放电时间**:指从电离器启动到静电荷完全被中和所需的时间。这个参数对于评估电离器的有效性和响应速度至关重要。 ##### 3. 替代测量技术的重要性 传统的测量方法可能存在一些局限性,如准确性不高、操作复杂等。因此,开发新的测量技术对于提高静电控制效率具有重要意义。 ##### 4. 技术报告内容概览 - **作者**:由静电释放协会的工作组3(Ionization)撰写。 - **目的**:提供一种测量电离器偏移电压和放电时间的新方法,旨在帮助制造商和用户更准确地评估电离器的性能。 - **警告**:该技术报告不构成强制性的标准,仅作为参考信息供业界使用。 - **前言**:阐述了静电控制在现代电子制造业中的重要性,并强调了技术报告的价值在于为用户提供有关材料、产品、系统或过程的信息。 ##### 5. 关键技术点 - **偏移电压测量**:介绍了几种新颖的方法和技术,以更精确地测量电离器产生的偏移电压,包括但不限于改进的测试设备、传感器技术和数据处理算法。 - **放电时间测量**:探讨了如何通过创新的技术手段缩短测量放电时间的过程,提高测量的精度和可靠性。 - **案例分析**:报告中可能包含了一些具体的案例分析,展示了新技术的实际应用效果及其相对于传统方法的优势。 #### 结论 ESD-TR3.0-01 ESD-TR3-v2.0-01-02 技术报告对于提高电离器偏移电压和放电时间的测量精度有着重要的意义。通过采用新的测量技术和方法,可以有效地提升静电控制系统的性能,减少因静电引起的设备故障率,进而提高整个电子产品的制造质量和效率。对于静电控制领域的研究人员和工程师来说,这份报告提供了宝贵的参考资源和实践指导。
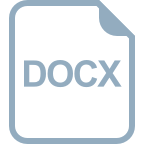
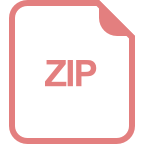
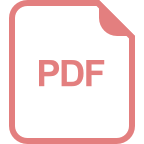
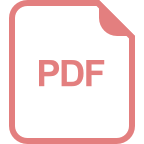
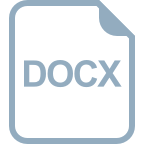
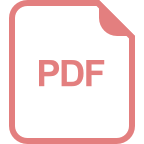
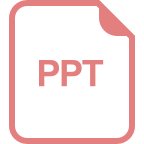
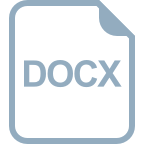
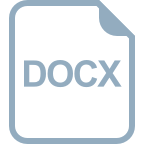
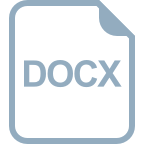
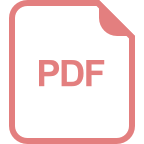
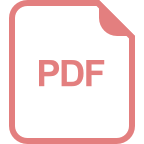
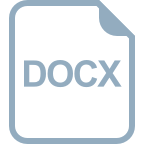
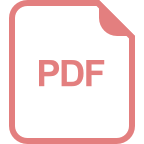
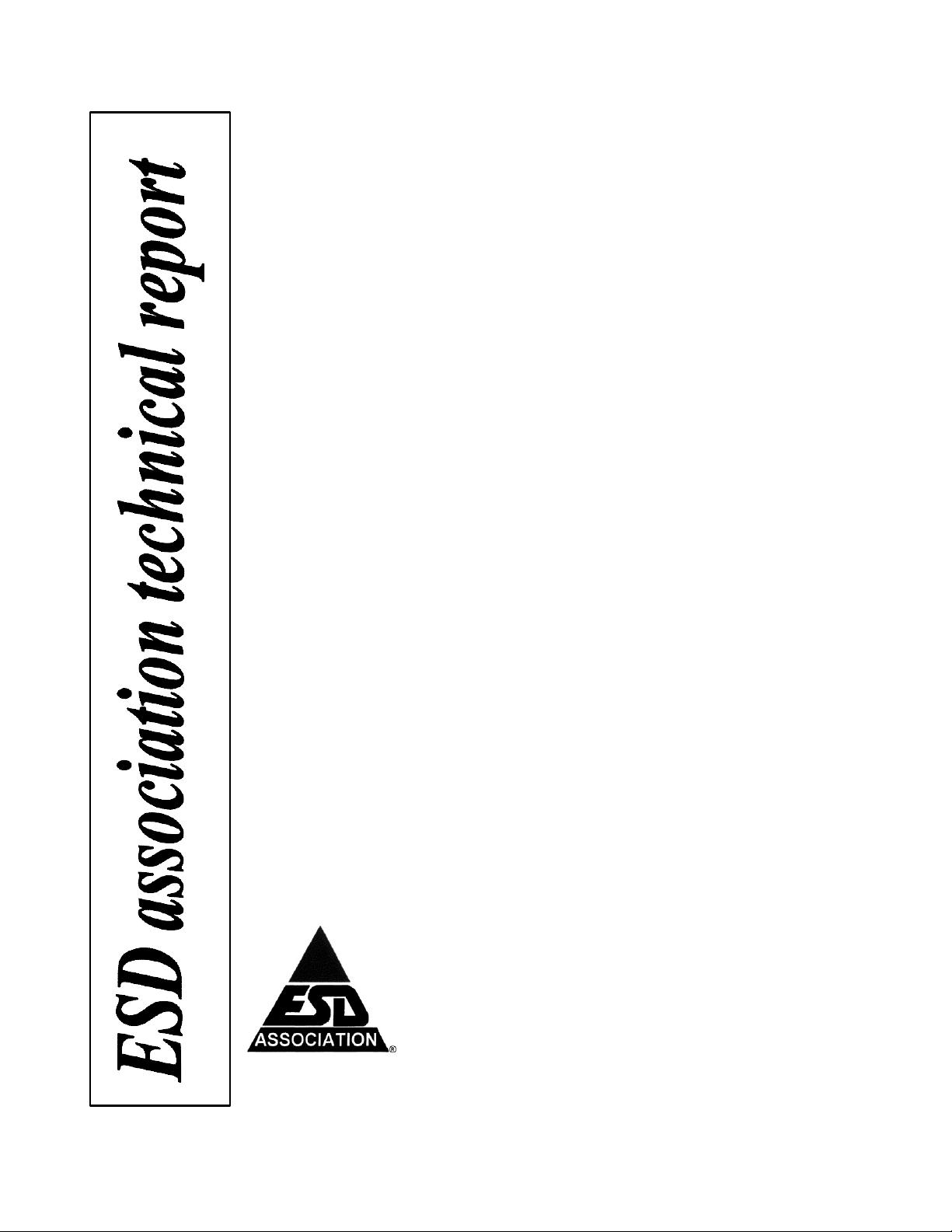
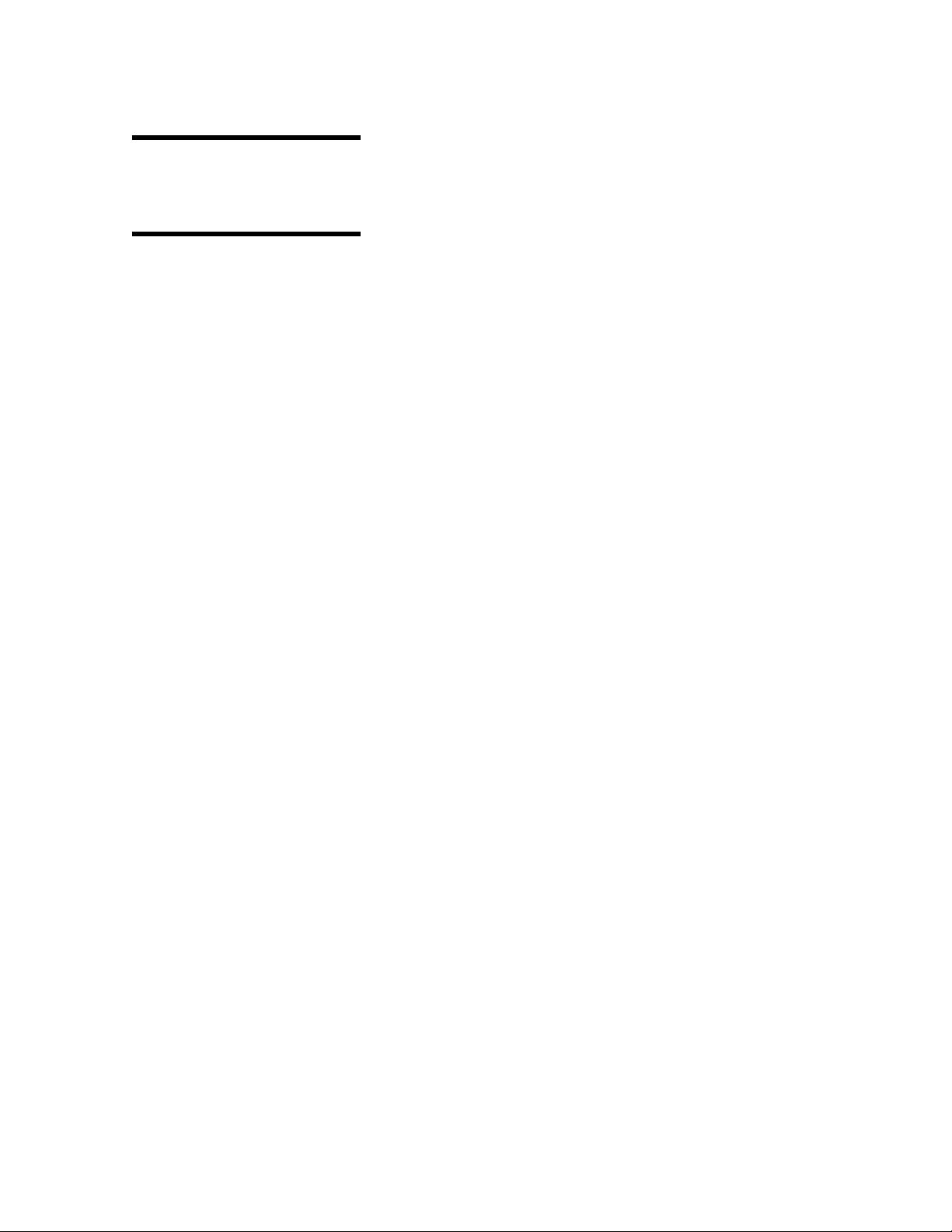

剩余12页未读,继续阅读
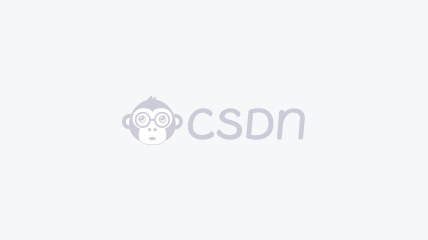

- 粉丝: 83
- 资源: 2002
我的内容管理 展开
我的资源 快来上传第一个资源
我的收益
登录查看自己的收益我的积分 登录查看自己的积分
我的C币 登录后查看C币余额
我的收藏
我的下载
下载帮助

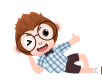
最新资源
- 【java+vue】WK系列开发框架-Java微服务+API网关+Vue3Element-Plus前后端分离.zip
- 【java+kotlin】基于无障碍服务实现的微信朋友圈多图分享方案,兼容微信各个版本.zip
- 【JavaScript】使用消息中间件设计聊天应用.zip
- 【JavaScript】基于vercel的serverless服务,把星火认知大模型接入微信公众号.zip
- 中国30个省份年末总人口数(2013-2022年)
- 【java+vue】基于uni-app的平院考试系统.zip
- 【JavaScript】云崽QQ机器人的插件.zip
- 【java考试系统】基于java开发的考试系统.zip
- 【jupyter notebook】优达学城-机器学习-毕业项目-猫狗大战.zip
- 【MATLAB】出版书籍《机器学习入门到实践——MATLAB实践应用》一书中的实例程序.zip
- 【nodejs】Nodejs、Express框架、消息中间件(实时聊天).zip
- 【MATLAB】MATLAB机器学习算法实现.zip
- 【PHP】Lumen10基础上扩展出的API启动项目.zip
- 【PHP】基于swoole实现的微信机器人,依赖vbot和微信网页版的功能,帮助管理微信群-聊天-踢人等.zip
- 前轮主动转向+直接横摆力矩联合控制的分布式驱动电动汽车模型设计开发 基于Simulink-CarSim联合仿真平台开发,主要包含模块:前轮主动转向功能模块(包含自主转向控制器、转向器模型)、直接横摆
- 【PHP】基于ThinkPHP 5.0的考试系统tp5.zip

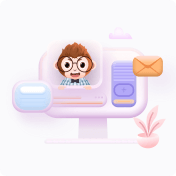
