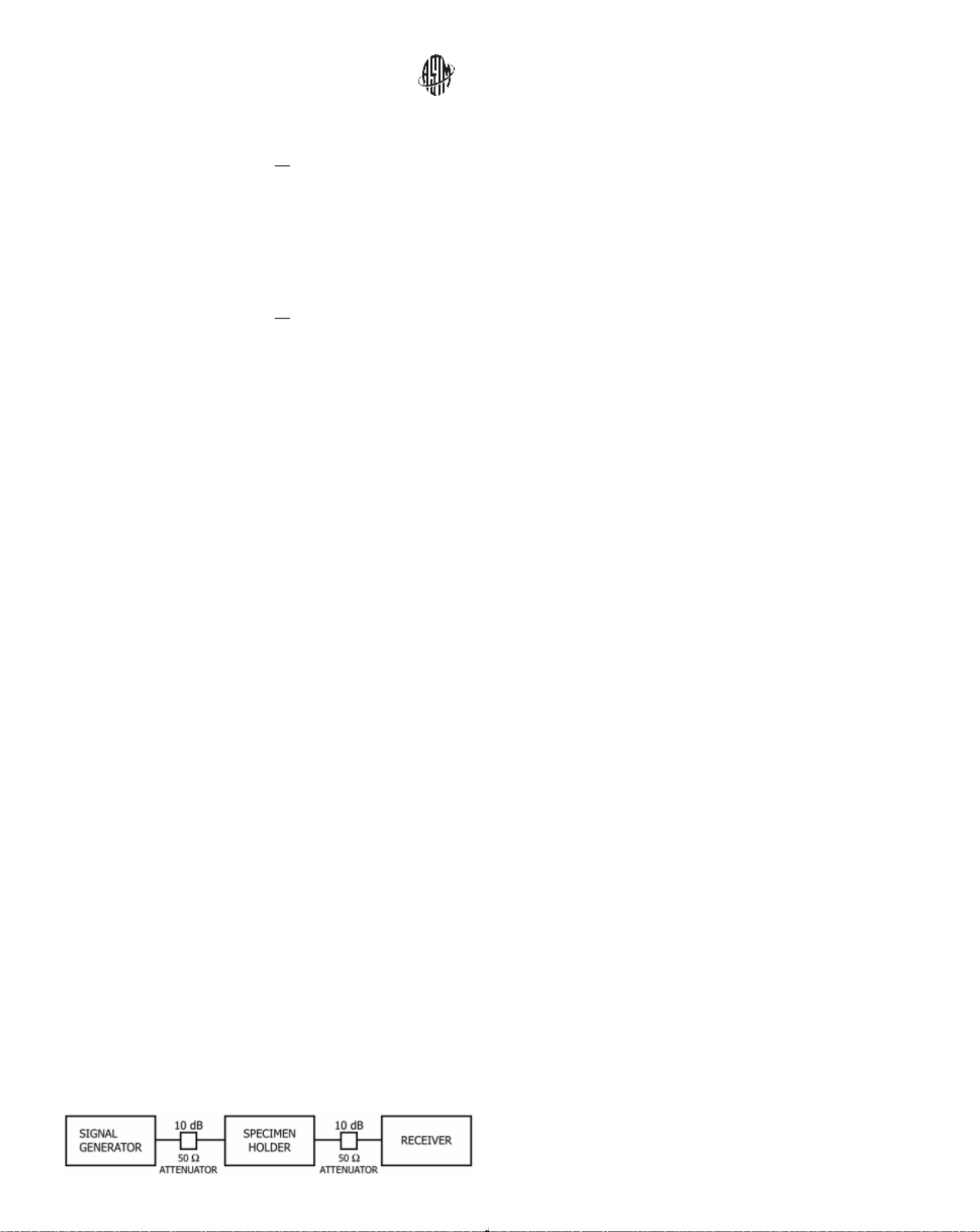
3.2.5.1 Discussion — SEis usually expressed in decibels
(dB) by the following equation:
SE5 10log
P
1
P
2
~
dB
!
(1)
where:
P
1
= received power with the material present, and
P
2
= received power without the material present.
If the receiver readout is in units of voltage, use the
following equation:
SE5 20log
V
1
V
2
~
dB
!
(2)
where:
V
1
and V
2
= respective voltage levels with and without a
material present.
According to these equations, SE will have a negative
value if less power is received with the material present than
when it is absent.
4. Signi?cance and Use
4.1 This test method applies to the measurement of SE of
planar materials under normal incidence, far-?eld, plane-wave
conditions (E and H tangential to the surface of the material).
4.2 The uncertainty of the measured SE values is a function
of material, mismatches throughout the transmission line path,
dynamic range of the measurement system, and the accuracy of
the ancillary equipment. An uncertainty analysis is given in
Appendix X1 to illustrate the uncertainty that may be achieved
by an experienced operator using good equipment. Deviations
from the procedure in this test method will increase this
uncertainty.
4.3 Approximate near-?eld values of SE may be calculated
for both E or H sources by using measured values of far-?eld
SE. A program may be generated from the source code in
Appendix X2 that is suitable for use on a personal computer.
4.4 This test method measures the net SE caused by
re?ection and absorption. Separate measurement of re?ected
and absorbed power may be accomplished by the addition of a
calibrated bidirectional coupler to the input of the holder.
5. Apparatus
5.1 A basic equipment setup is shown in Fig. 1.
5.2 Specimen Holder —Physical dimensions of a specimen
holder are given in Annex A1 . The specimen holder is an
enlarged, coaxial transmission line with special taper sections
and notched matching grooves to maintain a characteristic
impedance of 50 ? throughout the entire length of the holder.
This impedance is checked in accordance with 7.1, and any
variations greater than 6 0.5 ? are corrected. There are three
important aspects to this design. First, a pair of ?anges in the
middle of the structure hold the specimen. This allows capaci-
tive coupling of energy into insulating materials through
displacement current. Second, a reference specimen of the
same thickness and electrical properties as the load specimen
causes the same discontinuity in the transmission line as is
caused by the load specimen. Third, nonconductive (nylon)
screws are used to connect the two sections of the holder
together during tests. This prevents conduction currents from
dominating the desired displacement currents necessary for the
correct operation of this specimen holder.
5.3 Signal Generator, a source capable of generating a
sinusoidal signal over the desired portion of the frequency
range speci?ed in 1.2. A 50-? output impedance is needed to
minimize re?ections caused by mismatches. Precision step
attenuators are useful in increasing the effective dynamic range
for SE measurements.
5.4 Receiver, a device with a 50-? input impedance capable
of measuring signals over the same frequency range as the
signal generator in 5.3. A wide dynamic range is desirable to
achieve a wide dynamic range of measured SE values.
Typically, either a spectrum analyzer or a ?eld intensity meter
is used.
5.5 Coaxial Cables and Connectors —These are devices for
connecting power between speci?c components without caus-
ing interference with other components. These should all have
a 50-? characteristic impedance. Double-shielded cables pro-
vide lower leakage than single-shielded cables. Type N con-
nectors provide more reliability and less leakage than BNC
connectors. Precision 14-mm connectors give lower mismatch
errors and are more reliable under heavy usage than other
connectors but are more expensive and are not used on most
generators or receivers.
5.6 Attenuators —These are devices used to isolate the
specimen holder from the signal generator and the receiver.
Their main purpose in this system is for impedance matching.
A10-dB, 50-? attenuator should be used on each end of the
specimen holder. The material under test usually causesa large
re?ection of energy back into the signal generator. This may
also cause variations of the incident power by changing the
generator impedance loading. Use of a bidirectional coupler
allows monitoring and correcting any changes in incident
power as a result of this loading. Attenuators greater than 10
dB will excessively decrease the dynamic range of the mea-
surement system.
6. Test Specimens
6.1 The reference and load specimens shall be of the same
material and thickness. Both are shown in Fig. 2. Dimensions
are shown in Fig. 3. The load specimen can be larger than the
outer diameter of the ?ange on the holder but keeping them to
the dimensions shown in Fig. 3 will expedite handling.
6.2 Specimen thickness is a critical dimension. For the best
repeatability of SE measurements, reference specimen and load
specimen shall be identical in thickness. For this test method,
two specimens are considered to have identical thickness if the
FIG. 1 General Test Setup
D4935 - 10
2
Copyright ASTM International
--`,`,,``,`,,,,,``,,````,,,,`,`-`-`,,`,,`,`,,`---