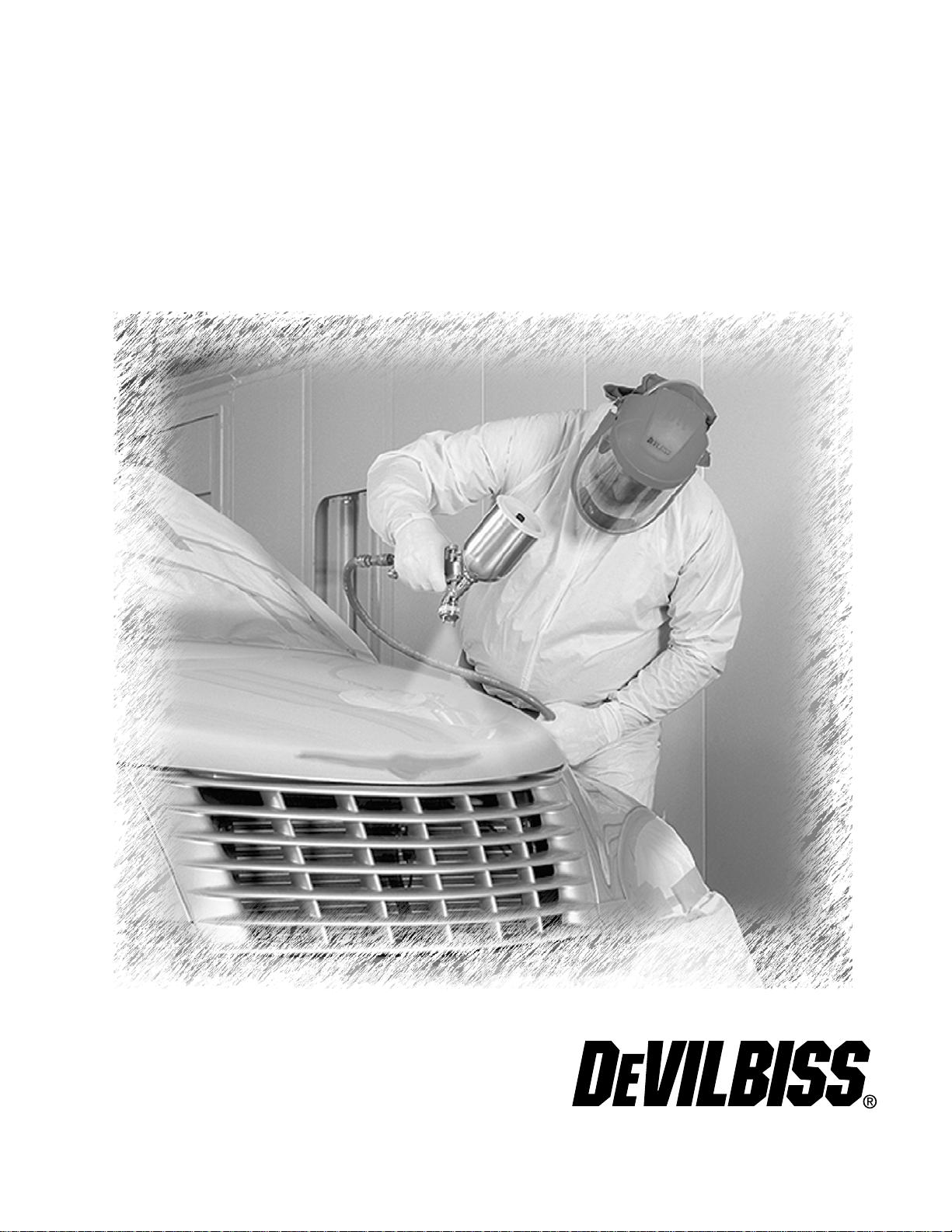
ABC’s of Spray Painting
ABC’s of Spray Painting
$10.00
A-2928-A
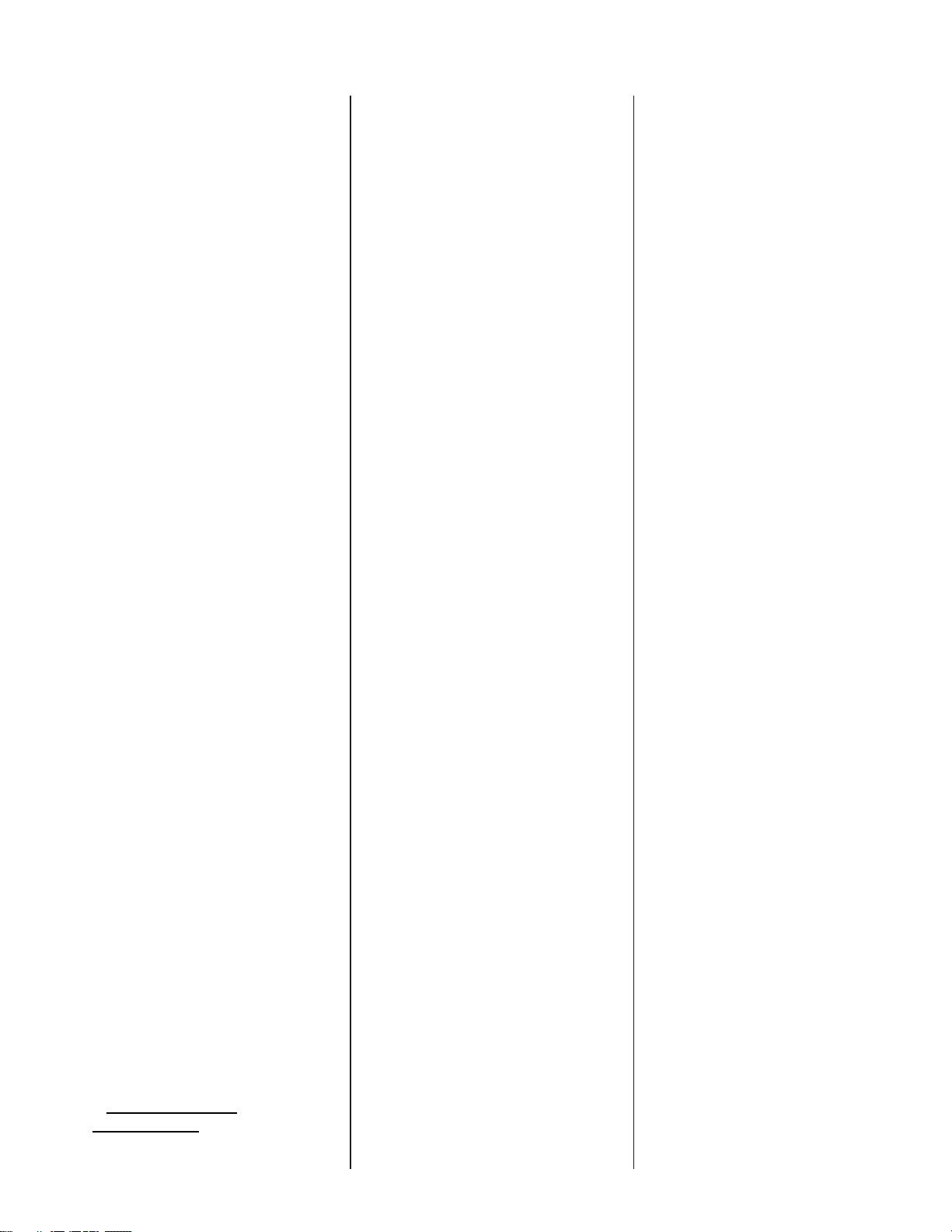
Forward Table of Contents
2
While this book examines the
spray finishing operation and its
equipment from many viewpoints,
there is still much more to be
learned to become truly proficient
at spray finishing.
The best way to become
proficient at spray finishing is to
just do it! Many trade technical
and community colleges offer
courses in spray finishing, a great
way to improve your skills.
Many of the “tricks” of the
professional spray finisher involve
paints and coatings. The
manufacturers of these materials
routinely publish complete books
on these subjects. These
publications are available in
specialty paint stores and will
provide you with considerable
detail. Many of these books also
contain information on techniques
for surface preparation.
Another important source of
information, particularly on
equipment use and selection is
your local spray finishing
equipment distributor. No book
could ever completely cover a
specialist’s in-depth knowledge of
equipment, techniques,
maintenance and troubleshooting.
Information is available from many
resources on the subject of spray
finishing. It is our hope that this
book will provide you with a start
toward perfecting your finishing
skills.
A recent addition to resources
available to the spray finisher is
the World Wide Web. Many
manufactures are represented and
question and answer forums are
available. Please visit our websites
a
www.binks.com.
t www.devilbiss.com and
About this book
…..
This book has been updated
several times from “The ABC’s of
Spray Equipment,” originally
published by The DeVilbiss
Company in 1954. It focuses on
equipment and techniques for
spray finishing.
The format of the original book
was question-and-answer. We
have retained that format in this
edition.
This book is organized around the
major components of an air spray
system… spray guns, material
containers, hose, air control
equipment, compressors, spray
booths, respirators and a short
section on general cleanliness and
other sources of information. A
thorough understanding of the
material in this book - plus a lot of
actual spray painting practice -
should enable you to handle just
about any spray painting situation.
Although we have made an effort
to make this book as detailed and
as complete as possible, be aware
that the equipment and product
systems used to illustrate points
are entirely based on DeVilbiss
technology. DeVilbiss is the
world’s oldest and largest
manufacturer of spray painting
equipment, and has maintained
this leadership since its founding
in 1888.
Forward …..…………………..….
2
1.
Introduction
………………..3
Surface Preparation………...3
Paint Preparation……………3
2.
Air Atomizing Spray
Guns
………………………....4
Spray Gun Types ……….….4
Part Identification and
Function……………….……..6
Operation ……………..……..9
Maintenance ……….………11
Troubleshooting …………...13
3.
Material Containers
…...…16
4.
Hose and Connections
…18
5.
Air Control Equipment.
….20
6.
Respirators
…….…….……22
7.
Air Compressors
…….……23
8.
Spray Booths
……….…….25
.
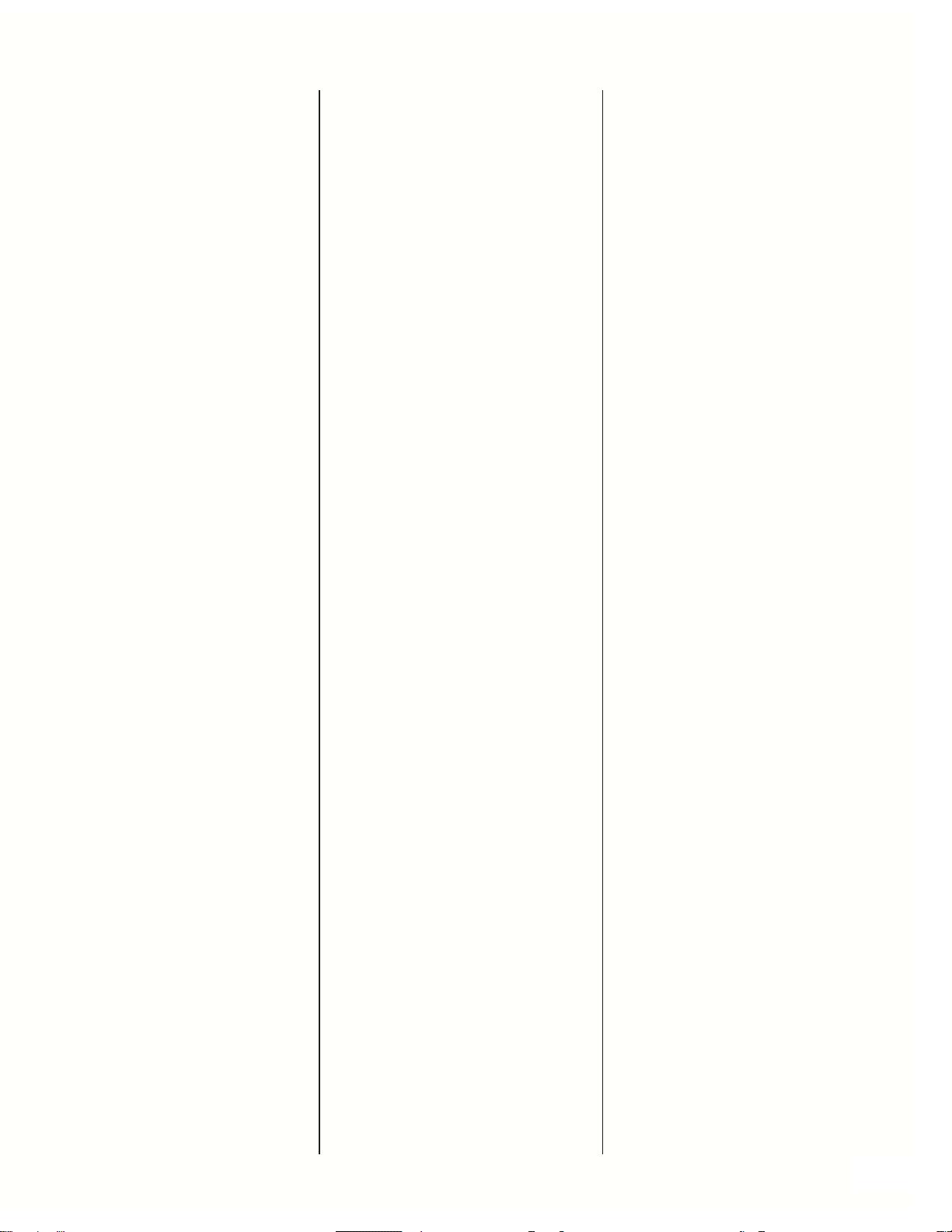
1. Introduction
3
This book is about the selection,
use and maintenance of finishing
equipment: spray guns, tanks,
cups, hoses, compressors,
regulators, spray booths,
respirators, etc. It presumes that
you are familiar with standard
surface preparation techniques
that may be required before
finishing actually begins. It also
presumes a basic knowledge of
the many different types of paints
and coatings available.
Creating a perfect finish requires a
solid knowledge of surface
preparation, finishes and spray
painting equipment. The first two
are extensively covered in many
other books. The manufacturers of
paints and coatings have gone to
great length to publish information
on their new and existing
products.
But, even an extensive knowledge
of surface preparation techniques
and paint chemistry is not enough
to assure a professional finish.
The finish must be applied by a
spray gun, and all the variables of
its use must be mastered.
The equipment necessary to apply
the finish – the spray gun, tank,
cup, regulator, hoses,
compressor, etc. – must all be
matched to the job as well as to
each other. That equipment must
be used and maintained properly,
with an appreciation of how and
why it works the way it does.
The moment of truth for any finish
happens when the trigger is
pulled. This book focuses on that
moment.
Surface Preparation
The surface to be finished should
be well cleaned before painting. If
the paint manufacturer’s
instructions call for it, the surface
should be chemically treated. Use
a blow-off gun and tack rag to
remove all dust and dirt. No
amount of primer or paint will
cover up a badly prepared
surface.
Plastic parts may contain static
electricity from the molding
process. This static attracts
particles of dust and dirt. Eliminate
them by treating with “destatisiz-
ing” air using a special blow-off
gun that imparts a neutral charge
to the airflow. A chemical anti-
static treatment is also available.
Paint Preparation
Today’s finishes are extremely
complex chemical formulations.
They include both solvent and
waterborne types. Some may
require the addition of solvents to
form the proper spraying viscosity.
Others may simply require the
addition of a second component at
a prescribed ratio to obtain
sprayable consistency. Many of
them also have hardeners or other
chemicals, added to them to
insure correct color match, gloss,
hardness, drying time or other
characteristics necessary to
produce a first class finish. Make
sure you are familiar with the
specific finish material data sheets
accompanying each material. Do
not mix materials from various
manufacturers. Read and follow
directions carefully.
All finish materials must also be
supplied with a Material Safety
Data Sheet (MSDS). This data
provides information on proper
handling and disposal of
materials. Many states require that
MSDS be kept on file by the user.
The first step is knowing the type
and color of paint the project
requires. With this determined,
follow the manufacturer’s
instruction for preparing it exactly.
If you have any doubts about how
to proceed, don’t guess! Contact
your paint supplier for help.
Improperly prepared paint will
never produce a good finish!
The chief characteristic that
determines the sprayablility of
paint and how much film may be
applied is its viscosity … or
consistency. Following the paint
manufacturer’s instructions will get
you close, but for professional
results, use a viscosity cup. It is a
simple but very accurate way to
measure the thickness of paint.
With the cup, you can thin or
reduce the paint to the precise
consistency required by the
manufacturer.
Always prepare paint in a clean,
dust-free environment. Paint has a
remarkable ability to pick up dirt.
Dirty paint will not only clog your
spray gun, but it will also ruin your
paint job. Get in the habit of
always pouring paint into the cup
or tank through a paint strainer.
Paint is never as clean as it looks.
3
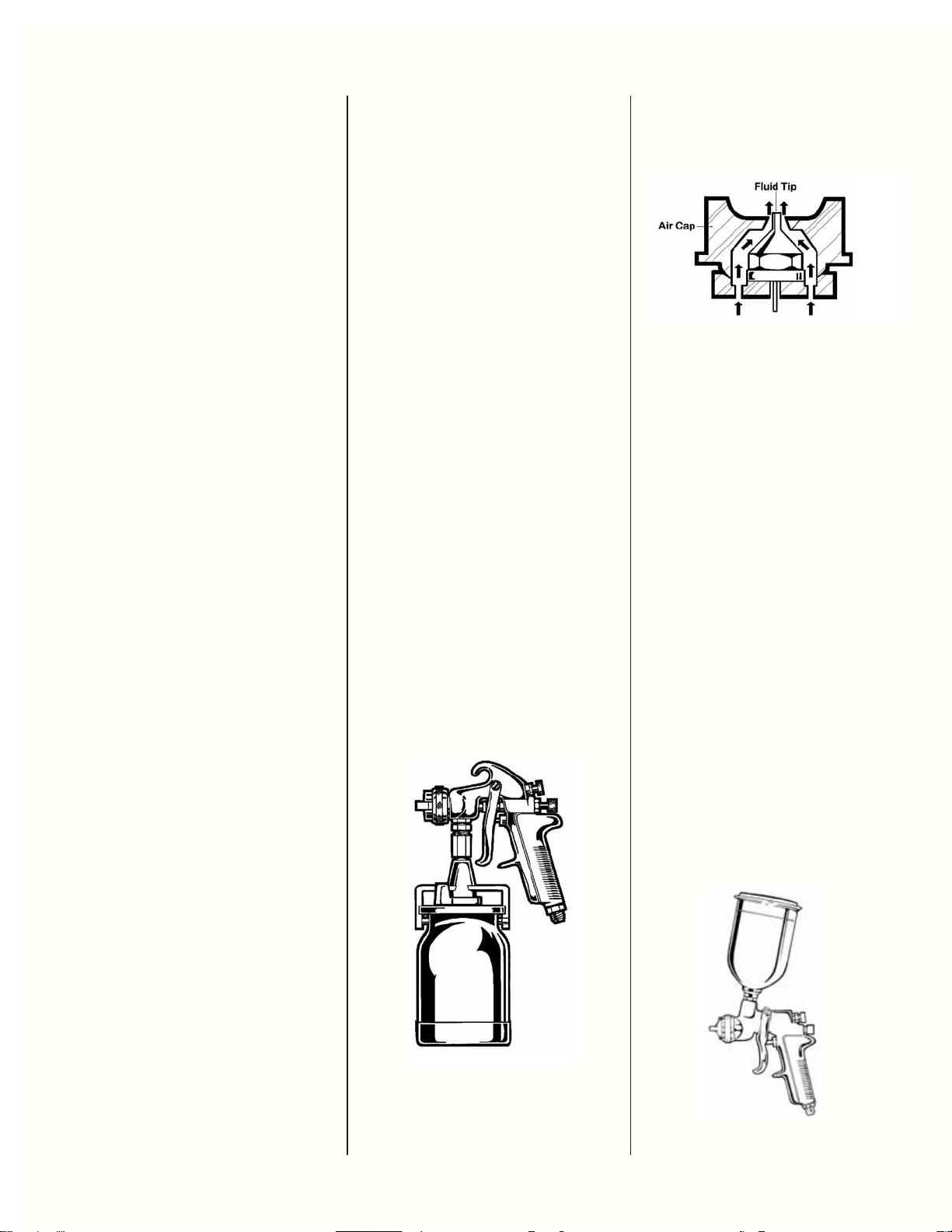
2. Air Atomizing Spray Guns
4
Introduction
The spray gun is the key
component in a finishing system. It
is a precision engineered and
manufactured instrument. Each
type and size is specifically
designed to perform a certain,
defined range of tasks.
As in most other areas of finishing
work, having the right tool for the
job goes a long way toward get-
ting professional results.
This chapter will help you know
which is the proper gun by review-
ing the Conventional Air and High
Volume/Low Pressure spray gun
designs commonly used in finish-
ing - suction feed, gravity feed and
pressure feed. It will also review
the different types of guns and
components within each design.
A thorough understanding of the
differences between systems will
allow you to select the right gun,
to use it properly to produce a
high quality finish and to con-
tribute toward a profitable finishing
operation.
SPRAY GUN TYPES
1. What is an air spray gun?
An air spray gun is a tool which
uses compressed air to atomize
paint, or other sprayable material,
and to apply it to a surface.
Air and material enter the gun
through separate passages and
are mixed at the air cap in a
controlled pattern.
2. What are the types of air
spray guns?
Air spray guns may be classified
in various ways. One way is by the
location of the material container:
Figure 1 shows a gun with a cup
attached below it.
Figure 3 shows a gun with a cup
attached above it.
Figure 4 shows a material con-
tainer some distance away from
its pressure feed gun.
The type of material feed system
is also a way of classifying guns:
Suction Feed...
draws material to
the gun by suction as in Figure 1.
Gravity Feed...
the material travels
down, carried by its own weight
and gravity as in Figure 3.
Pressure Feed...
the material is
fed by positive pressure as in
Figure 4.
Guns may also be classified as
either external or internal mix
depending upon the type of air
cap.
3. What is a suction feed gun?
A spray gun design in which a
stream of compressed air creates
a vacuum at the air cap, providing
a siphoning action. Atmospheric
pressure on the material in the
suction cup forces it up the suction
tube, into the gun and out the fluid
tip, where it is atomized by the air
cap. The vent holes in the cup lid
must be open. This type gun is
usually limited to a one-quart, or
smaller, capacity container and
low to medium viscosity materials.
Figure 1- Suction Feed Gun with
attached cup
Suction feed is easily identified by
the fluid tip extending slightly be-
yond the face of the air cap, see
figure 2.
Figure 2 - Suction Feed Air Cap
Suction feed guns are suited to
many color changes and to small
amounts of material, such as in
automotive panel/bumper repairs
and "completes," touchup, or
lower production operations.
4. What is a gravity feed gun?
This design uses gravity to flow
the material from the cup, which is
mounted above the gun, into the
gun for spraying. No fluid pickup
tube is used, since the fluid outlet
is at the bottom of the cup.
This cup has a vent hole at the top
of the cup that must remain open.
It is limited to 34 ounce capacities
due to weight and balance.
Gravity feed guns are ideal for
small applications such as
automotive panel/bumper repairs
and "completes," spot repair,or
for finishing in a limited space.
They require less air than a suction
feed gun, and usually have less
overspray.
Figure 3- Gravity Feed Gun with
attached cup
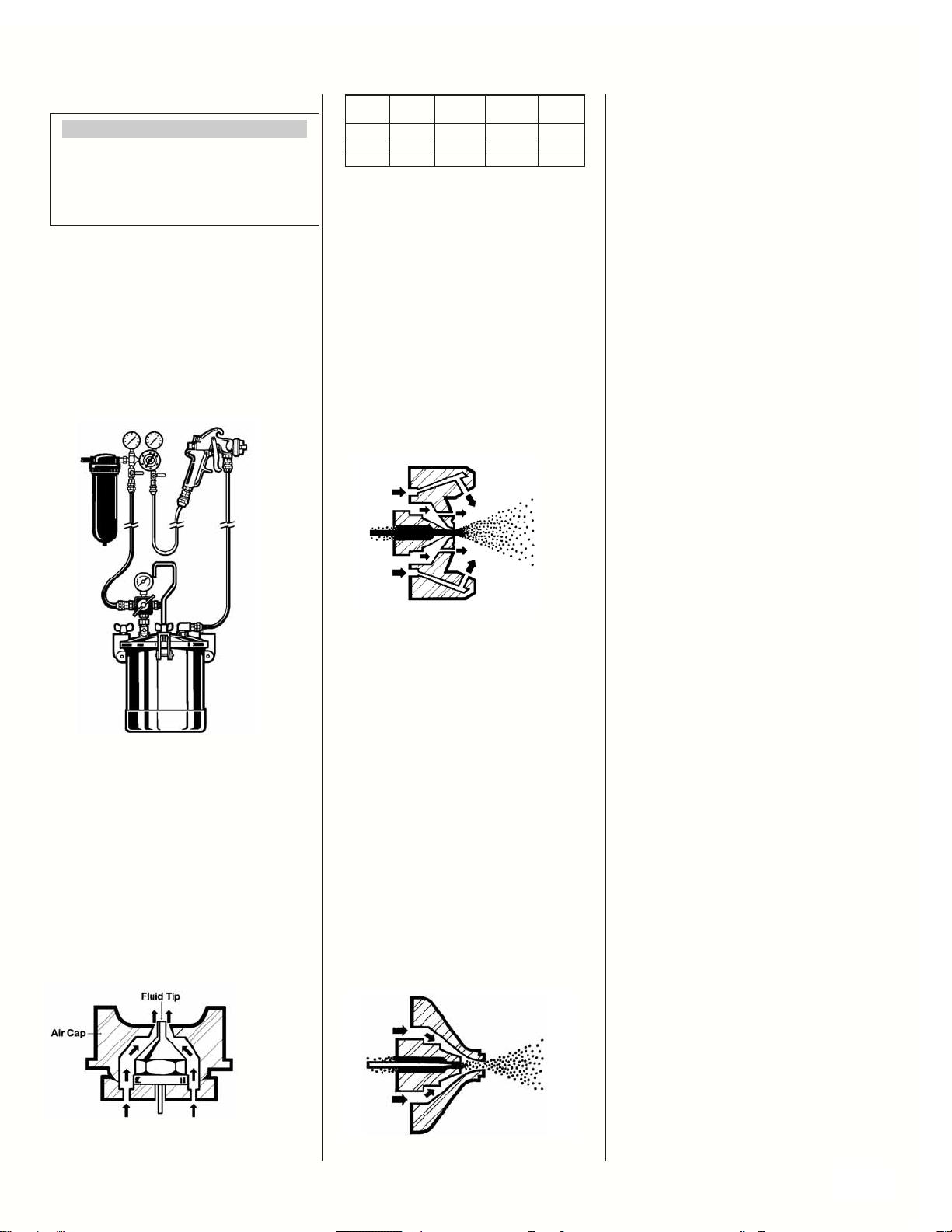
2. Air Atomizing Spray Guns (Cont’d)
5
5. What is a pressure feed gun?
In this design, the fluid tip is flush
with the face of the air cap (see
Figure 5). The material is
pressurized in a separate cup,
tank or pump. The pressure forces
the material through the fluid tip
and to the air cap for atomization.
Figure 4 - Typical Pressure Feed Gun
with remote pot
This system is normally used
when large quantities of material
are to be applied, when the
material is too heavy to be
siphoned from a container or
when fast application is required.
Production spraying in a
manufacturing plant or fleet
refinishing operation is a typical
use of a pressure feed system
Figure 5 - Pressure Feed Air Cap
Type Viscosity Fluid Atomizing Type
Feed (#2 Zahn) Oz/Minute Pressure Production
Suction up to 24 10-12 40-50 Low
Gravity up to 24 10-12
12-24
30-50 Low
Pressure up to 29 50-60 High
6. What is an external mix air
cap?
This gun mixes and atomizes air
and fluid outside the air cap.
It can be used for applying all
types of materials, and it is
particularly desirable when
spraying fast drying paints such as
basecoat and lacquer. It is also
used when a high quality finish is
desired.
Figure 6 - External Mix Gun
7. What is an internal mix cap?
This cap mixes air and material
inside the air cap, before expelling
them.
It is normally used where low air
pressures and volumes are
available, or where slow-drying
materials are being sprayed.
A typical example is spraying flat
wall paint, or outside house paint,
with a small compressor.
Internal mix caps are rarely used
for finishing when a fast-drying
material is being sprayed, or when
a high quality finish is required.
Figure 7 - Internal Mix Air Cap
8. What is HVLP?
HVLP, or High-Volume/Low
Pressure, uses a high volume of
air (typically between 15-26 CFM)
delivered at low pressure (10 PSI
or less at the air cap) to atomize
paint into a soft, low-velocity
pattern of particles.
In many cases, less than 10 psi is
needed in order to atomize.
Proper setup utilizes no more fluid
and air pressure than is needed to
produce the required quality and a
flow rate that will meet production
requirements.
As a result, far less material is lost
in overspray, bounceback and
blowback than with conventional
air spray. This is why HVLP
delivers a dramatically higher
transfer efficiency (the amount of
paint that adheres to the substrate
compared to the amount of paint
sprayed) than spray systems
using a higher atomizing pressure.
The HVLP spray gun resembles a
standard spray gun in shape and
operation. Models that use high
inlet pressure (35-80 psi) and
convert to low pressure internally
within the spray gun are called
HVLP conversion guns.
Some HVLP models, particularly
those using turbines to generate
air, bleed air continuously to
minimize back- pressure against
the air flow of the turbine.
The air cap design is similar to
that of a standard spray gun, with
a variety of air jets directing the
atomizing air into the fluid stream,
atomizing it as it leaves the tip.
HVLP is growing in popularity and
new environmental regulations are
requiring it for many applications.
HVLP can be used with a wide
variety of materials, including
two-component paints, urethanes,
acrylics, epoxies, enamels,
lacquers, stains, primers, etc.
A DeVilbiss Pro Tip:
When using a gravity feed system,
downsize the tip one size from suction.
If the suction system calls for a .070”,
use a .055” or .063”
5