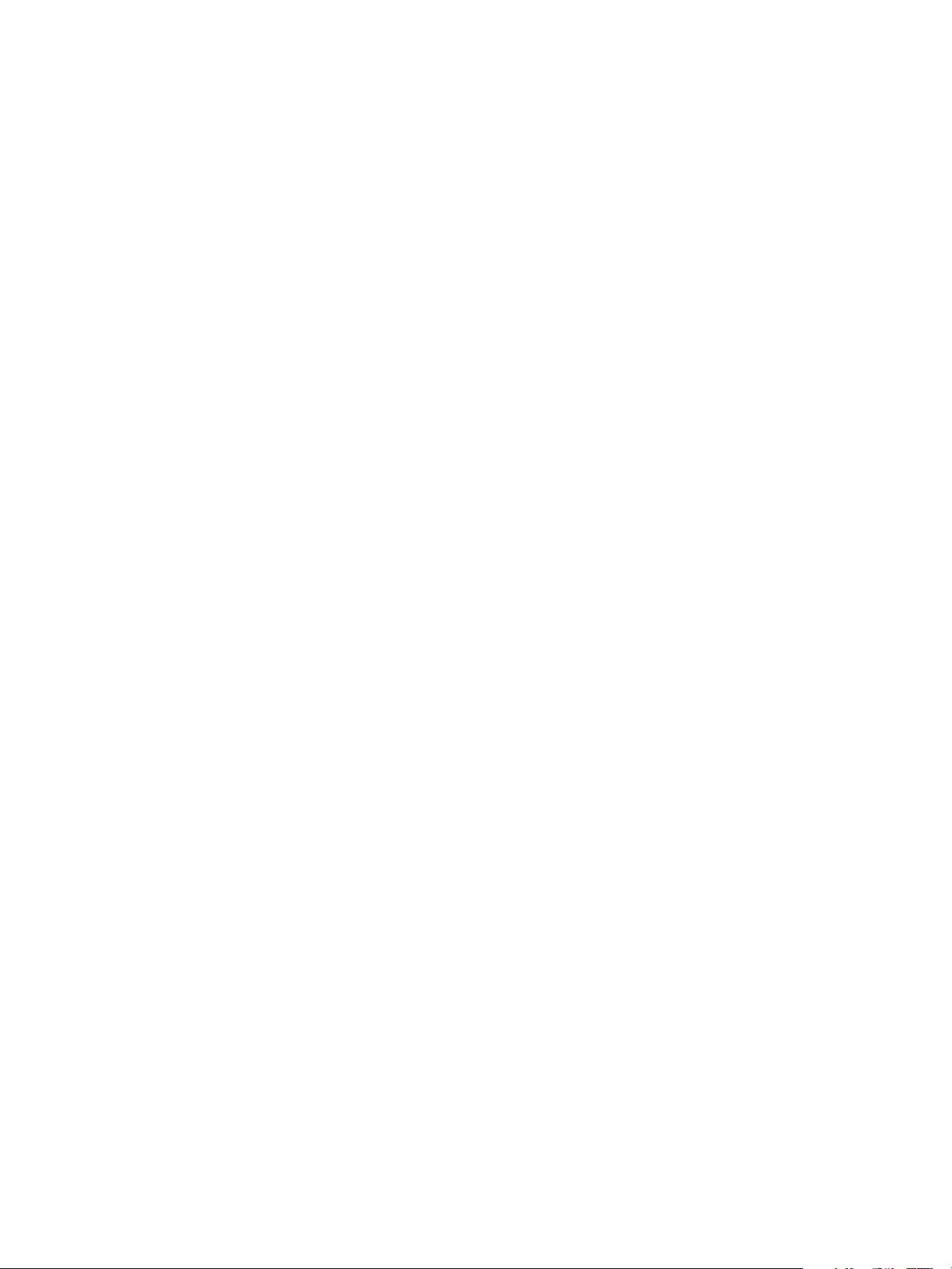
IEEE TRANSACTIONS ON INDUSTRIAL ELECTRONICS, VOL. 60, NO. 3, MARCH 2013 885
Analytical and Offline Approach to Select Optimal
Hysteresis Bands of DTC for PMSM
Shashidhar Mathapati and Joachim Böcker, Member, IEEE
Abstract—The switching frequency of an inverter under direct
torque control is mainly decided by the flux- and torque-controller
output switching counts. It is known that, with fixed hysteresis
bands, the switching frequency varies as the operating point
changes. It is possible, however, to keep the switching frequency
constant by the adaptation of hysteresis bands. The switching
frequency is a function of both torque and flux bands. Different
combinations of flux and torque bands can be used to achieve
a desired switching frequency. However, for optimal control, one
among the many available combinations has to be chosen. In
this contribution, it is proposed to select the hysteresis bands
based on the criterion of the minimum harmonic distortion in the
motor currents for the required switching frequency. An analytical
procedure is presented to calculate these optimal bands for the
permanent-magnet synchronous motor. The analytical results
were cross checked with simulation studies and validated by
detailed experimentation. In order not to degrade the control
performance by computational delay, a field-programmable-gate-
array-based control platform is being used for implementation.
Index Terms —Direct torque control (DTC), field-
programmable gate array (FPGA), optimal control, permanent-
magnet synchronous motor (PMSM), total harmonic distortion
(THD).
I. INTRODUCTION
T
HE direct torque control (DTC) [1] of ac motor drives
has been known in the drives industry for more than two
decades. Another control similar to the DTC is the direct self-
control (DSC) [2]. Both inventions had been published around
the same time in the mid-80s. These controls are known for their
highest control dynamics of torque regulation, and both of them
utilize hysteresis controllers to regulate the torque and the flux
of the motor. The main difference exists in the trajectory of the
flux control; the DSC guides the flux vector along a hexagonal
trajectory (or 18 corners), whereas with the DTC, it is circular.
The application of the DSC is mainly seen in traction drives
because it can cope with rather low switching frequencies. The
DTC is utilized with low and medium power drives due to its
better total harmonic distortion (THD) and higher switching
frequency [3], [4]. Our discussion in this paper is limited only
to the DTC.
The DTC however has the i nherent problem of varying
switching frequency with constant hysteresis bands, which is
undesired for some applications. In order to improve this,
Manuscript received July 22, 2010; revised November 11, 2010 and
February 23, 2011; accepted September 22, 2011. Date of publication
February 29, 2012; date of current version October 16, 2012.
S. Mathapati is with the Delta India Electronics, Bangalore 560068, India
(e-mail: Mathapati.Shashidhar@googlemail.com).
J. Böcker is with the University of Paderborn, 33098 Paderborn, Germany
(e-mail: boecker@lea.upb.de).
Digital Object Identifier 10.1109/TIE.2012.2189530
researchers have worked on different approaches. Contributions
[5] and [6] present a similar control s tructure, which had the
similar concept for torque control as in [1] and [2] but combined
with space-vector modulation (SVM). That indeed ensures the
constant switching frequency; however, the inherent robustness
and dynamics of the original DTC or DSC is lost with this ap-
proach. Extensive research has been seen in this direction; a de-
tailed survey on the DTC for induction machines can be found
in [7]. The research on the SVM-DTC of the permanent-magnet
synchronous motor (PMSM) is also intensively covered; some
of the recent references can be found in [8] and [9]. In [10]
and [11], some additional modifications of the basic DTC are
proposed to improve the switching frequency performance.
Very few publications worked on detailed analytical approaches
to analyze the DTC. In [12], an evaluation of the switching fre-
quency as a function of the hysteresis bands is given with a fo-
cus on the reduction of iron loss due to the higher flux ripple. A
similar analysis is also presented in [13], where analytical cal-
culations of the flux- and torque-controller switching are dealt
to evaluate the switching frequency. Both publications [12] and
[13] state that the switching frequency is not linearly related
to the THD and suggest that the flux-controller band should be
small in comparison with the torque-controller band. Similarly,
a prediction technique is employed to improve the conventional
DTC’s torque and flux ripple performance in [14] and [15]. In
spite of many such developments in the DTC, they have not
been able to make a significant impact in capturing the market
of standard and servodrives. In fact, this is still dominated by
pulsewidth-modulation ( PWM) controls; the reasons lie in their
lower THD and the constant switching frequency of the inverter.
None of the publications from the literature survey has
proposed a strategy to select the hysteresis bands in order
to keep the switching frequency constant and/or to aim for
the optimal THD design. In this paper, the main focus is to
present a completely analytical and offline approach to evaluate
the optimal hysteresis bands, which ensure constant switching
frequency for the whole operating region of the drive. The
criterion for the selection of the hysteresis bands is based on
the minimum harmonics in the motor currents. In the course
of the proposed method’s evaluation procedure, comparisons
with simulation results are given at every step. After the offline
evaluation of the optimal hysteresis bands, experiments are
carried out for the validation.
It is well known that the performance of the hysteresis
controllers depends very much on the computational delay
or the dead time of the control. In order to ensure that the
control realization behaves very close to the continuous-time
performance, a field-programmable gate array (FPGA) is used
0278-0046/$31.00 © 2012 IEEE