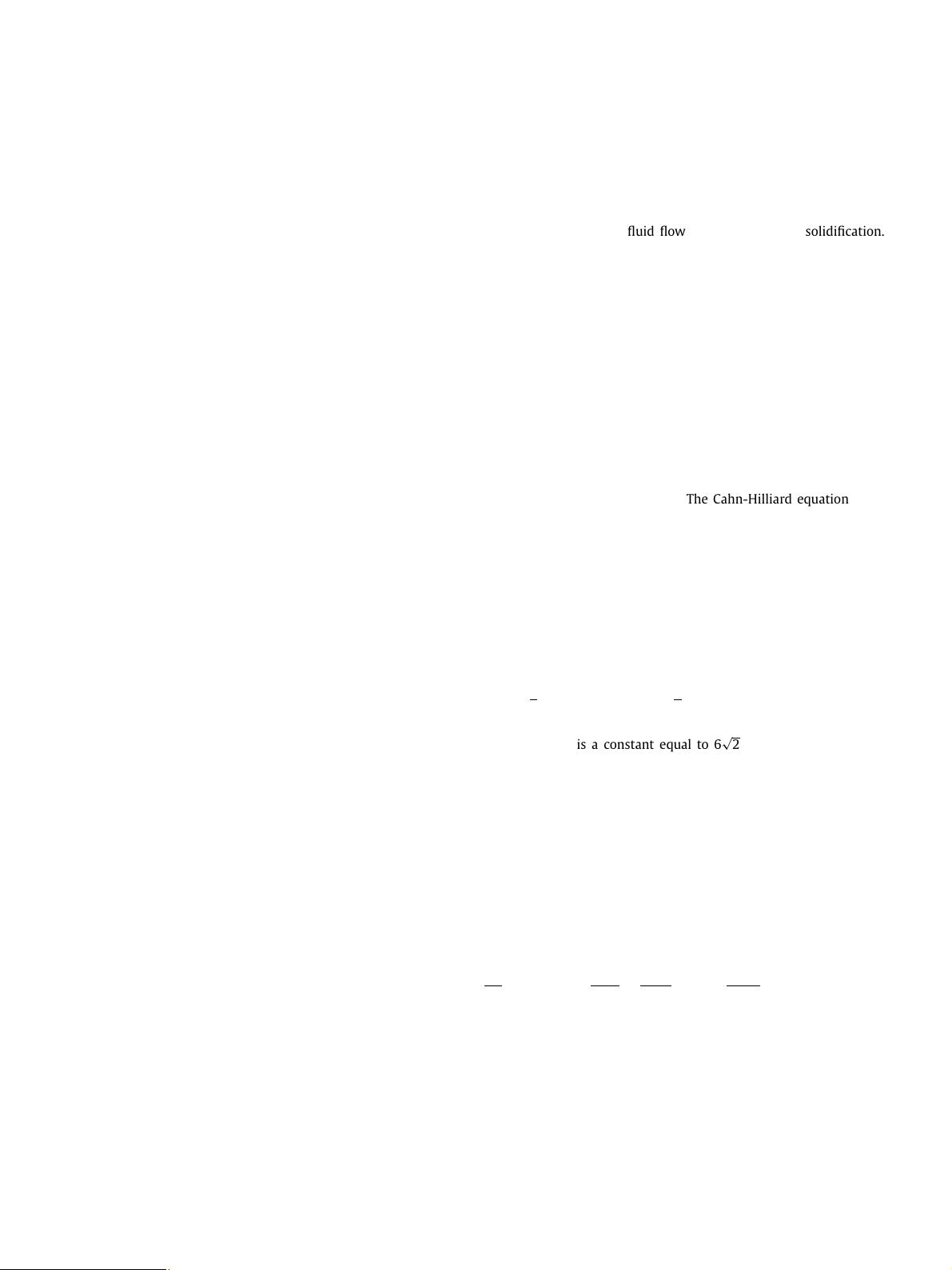
52 M. Shen, B.Q. Li and Q. Yang et al. / International Journal of Multiphase Flow 116 (2019) 51–66
required that an interface representation and advection algorithm
be clearly defined. The volume of fluid method falls into this
category. Two “volume of fluid” (VOF) based codes, FLOW-3D
and RIPPLE, were employed by Trapaga and Szekely (1991) and
Liu et al. (1993) to simulate a thermal spray process. The former
did not take solidification into consideration, but both chose par-
ticles of micrometers in diameter and impinging velocities up to
several hundred meters per second. Based on RIPPLE and a vol-
ume tracking algorithm, Bussmann et al. (1999) delved into the im-
pact of a droplet onto an oblique substrate and a sharp edge, with
surface tension converted to a volumetric force and contact angle
introduced as a boundary condition. However, heat transfer and
phase change during impact were ignored. An improved model was
proposed by Pasandideh-Fard et al. (2002) to track droplet free sur-
face and solidification front. Drawing on an enthalpy method, they
also studied the heat released during phase transformations and
obtained results in good agreement with experiments. With a VOF
model, Wilden et al. (2006) examined the flattening of particles.
Microstructure simulation was conducted as well in his work using
the phase-field method. With the penalty and Eulerian-Lagrangian
VOF methods, Vincent et al. (2015) treated droplet solidification,
and looking into thermal contact resistance, asserted that solidifi-
cation would be accelerated by lowering it. Ramanuj et al. (2017) ,
via a VOF method, investigated splat morphology and solidifica-
tion characteristics of a molten hypoeutectic alloy droplet. All these
variants of VOF methods, except that used by Vincent et al. (2015) ,
need interface reconstruction, which means the interface is not
guaranteed from local fluid volume data, and request special care
to treat the advection term. Nevertheless, the inherent mass (and
volume) conservation is a salient feature of VOF methods.
Except being tracked explicitly, the moving boundaries can also
be traced implicitly. Lattice Boltzmann method is such a strat-
egy, but it is on a mesoscale. A Lattice Boltzmann equation (LBE)
method for incompressible binary fluids was invoked by Lee and
Liu (2010) to model contact line dynamics, solidification not be-
ing considered. With a LBE method, Sun et al. (2015) , resting on
the pseudo-potential model and enthalpy formation, explored wa-
ter droplet solidification. Though this method can capture inter-
faces implicitly and is simple to implement, yet it is impossible
to prescribe macroscopic fluid properties as input parameters. In-
stead, they are input as functions of microscopic parameters, which
are to be adjusted in a model. Besides, hydrodynamic conditions
are difficult to satisfy on a grid node exactly.
Retaining the appealing merit of implicitly capturing interfaces,
the phase-field method has emerged as a powerful tool in simulat-
ing multiphase flows, with the ease of numerical implementation
and ready extension to three dimensions. It can also be applied
to treat moving boundaries at both micro and macro scales. With
a phase-field method, Lim and Lam (2014) studied the impinge-
ment and spreading of micro-sized droplets on surfaces of het-
erogeneous wettability at nonzero impacting velocities. For a bet-
ter understanding of the underlying physics behind droplet impact,
Zhang et al. (2016) , using a phase-field method, examined different
impact phenomena, such as bouncing and splashing, under isother-
mal conditions. Luo et al. (2017) delved into droplet spreading on
topologically rough substrate surfaces, and moreover, over various
textures of substrate surface in three dimensions with a phase-
field method. They focused on pure fluid flow, without consider-
ing heat transfer and solidification. However, it is of crucial impor-
tance to incorporate these two thermal elements into a phase-field
model to bring out its best in predicting droplet behavior during
plasma spraying, especially at supersonic velocities. Nevertheless,
to the authors’ best knowledge, few articles appear to have been
reported on the phase-field modeling of coupled thermal and fluid
dynamics of an impacting droplet. The paper is therefore devoted
to developing a phase-field model for such purpose. At length, the
paper is organized as follows. First, the model was put forward and
verified against three low speed impacts, and then was applied to
a supersonic impact under practical conditions. The results show
good agreement with experiments.
2. Mathematical statement
During droplet impact in thermal spray, three physical pro-
cesses are coupled, i.e. , fluid flow, heat transfer, and solidification.
Thus in this section the governing equations for these three fields
are given. Beginning from the flow field, these equations are to be
expounded, in turn and in a detailed manner.
2.1. Fluid flow
As for two-phase flows, the convective Cahn-Hilliard equation
( Jacqmin, 20 0 0 ) is employed to describe the evolution of the or-
der parameter c , which is a measure of phase, or a phase indicator.
Generally, two different integers will be assigned to c , each denot-
ing a distinct phase. A transition between the two phases is con-
sidered to occur over a thin region where c changes drastically but
continuously. With such a description, all physical quantities at a
fixed point in space can be seen as functions of c . Once it is deter-
mined, the physical quantities can be calculated through a simple
liner relation as introduced later. The Cahn-Hilliard equation takes
the following form,
c
t
+ u · ∇ c − M∇
2
φ = 0 ∈ × T (1)
where represents the geometric computational domain, T the
computing time duration, u the velocity field, and M the strength
of diffusion. In this way, Eq. (1) describes the evolution of the or-
der parameter c via diffusion and convection, the first mechanism
of which is due to the gradient of chemical potential φ = δ f /δc. It
is derived from the free energy density f per unit volume, a func-
tion of c ,
f
(
c
)
=
1
2
ξγα
|
∇c
|
2
+ ξ
−1
γα·
1
4
c
2
(
1 − c
)
2
∈ × T (2)
where ξ stands for a measure of interfacial thickness, γ surface
tension, and α is a constant equal to 6
√
2 . It is noted that in this
paper c = 1 is to denote a gas and c = 0 a liquid, with the value in
between indicating the interface. The first term on the right hand
side of Eq. (2) accounts for the energy density due to phase gra-
dients and the second due to bulk phases. Additionally, the second
term has two stable minima, corresponding to two distinct phases.
The equilibrium phase profile is determined through minimizing
the total free energy F =
f d V .
Now we turn to fluid motion. With an assumption about the in-
compressibility of Newtonian fluids, the equations governing mass
and momentum conservation are obtained as follows:
∇ · u = 0 (3)
∂u
∂t
+ u · ∇u = −
∇p
ρ
(
c
)
+
∇ · σ
ρ
(
c
)
+ g +
φ∇c
ρ
(
c
)
+ S (4)
in which φ∇c , signifying surface tension, has been converted,
equivalently, into a body force. S is a source term. σ = μ(c)[ ∇u +
(∇u )
T
] is the Newtonian stress tensor. Also, g is the local gravita-
tional acceleration. Note that density and viscosity have been re-
cast as functions of the order parameter c in such a form that
ρ
(
c
)
=
(
ρ
1
− ρ
2
)
c + ρ
2
μ
(
c
)
=
(
μ
1
− μ
2
)
c + μ
2
ρ
1
and ρ
2
indicate the densities of a gas and a liquid, respec-
tively, in this paper. If physical properties change much after solidi-
fication, ρ
2
, for example, should be further interpreted as functions