
xxpr_ybgg
- 粉丝: 6831
- 资源: 3万+
最新资源
- 软路由安装飞牛OS NAS图文教程
- 2024-2025-1成绩.dbf
- STM32F103C8T6 数据表 (PDF)
- 电网电压不平衡环境下三相三电平PWM整流器仿真模型:基于基波正负序分离的解耦控制策略与功率平衡控制实现直流侧电压稳定,电网电压不平衡下PWM整流器仿真控制,电网电压不平衡下三相三电平PWM整流器仿真模
- MATLAB仿真m序列、Gold序列和Kasami序列扩频码性能分析及生成方法探究,MATLAB仿真分析m序列、Gold序列与Kasami序列的扩频码性能 该程序涵盖生成与特性分析,助您深入理解与选
- 基于北方苍鹰优化算法的径向基函数神经网络时间序列预测模型:参数优化与交叉验证策略在Matlab中的实现,基于NGO-RBF神经网络的优化时间序列预测算法:参数优化及交叉验证防过拟合的Matlab实现
- Carsim与Matlab Simulink联合仿真四轮电动汽车转向容错控制模型,基于Carsim与Matlab Simulink联合仿真的四轮电动汽车线控转向失效容错控制模型研究及参考文献分析,Ca
- 【STM32学习笔记】FATFS管理SD卡+FreeRTOS+ESP8266的无线文件传输功能模块程序框图
- 激光打孔熔池模拟:COMSOL专业模型与视频教程,助力激光研究人员与工程师的高效实践 ,激光打孔熔池模拟与服务:COMSOL专业建模与教程视频助力激光研究人员与工程师深化研究,COMSOL 激光 激光
- 《Java+Web应用程序开发》Java实用技术应用案例.ppt
- Oracle数据导入导出小工具(主要用于导入导出小批量含大字段的数据)源码.rar
- 《ARM9嵌入式系统设计基础教程》第12章嵌入式Linux软件设计.ppt
- 运维服务成熟度二级标准助力企业服务能力提升及业务发展的实践案例
- 微控制器领域_STM32F746_示波器_可视化工具_1741146546.zip
- 自考离散数学02324
- 嵌入式开发_Stm32工具评估_项目创建与配置_1741142736.zip
资源上传下载、课程学习等过程中有任何疑问或建议,欢迎提出宝贵意见哦~我们会及时处理!
点击此处反馈


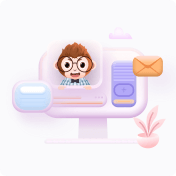