
xiaowu198809
- 粉丝: 13
- 资源: 17万+
最新资源
- 电子商务_网上商城管理系统_用户身份验证_便捷购物_1740825436.zip
- 商城管理_System_SCUM_1740825333.zip
- 智能公交系统电子站牌设计_STM32_微信小程序_毕业设_1740825532.zip
- 全国地图 省GeoJson 市GeoJson
- MATLAB实现领航追随法与人工势场法融合的车辆编队避障控制策略,MATLAB领航追随法融合人工势场法的车辆编队避障控制策略实现研究,MATLAB基于领航追随法的车辆编队控制,领航追随者与人工势场法的
- 迪恩在线教育素材培训课程网站源码 discuz内核完整资料带数据
- 基于手性光学效应的连续介质束缚态研究:从三维图谱到Q因子图的所见即所得超表面复现分析,基于Comsol模拟:三次谐波效应下的本征手性BIC超表面研究-远场偏振图、手性透射曲线与光学响应的可见性分析
- 和材料性能分析** COMSOL 培训视频,深入解析多物理场仿真技术与应用 **深入解析COMSOL多物理场仿真技术与应用:从结构力学到化学反应的全面分析**,界面仿真和流控模拟 COMSO
- 找高手:应该如何训练工程造价的大模型?
- NOIP2009年提高组NOI Linux和Cena测评环境与数据
- 手把手项目实践:用Labview制作一个电子秤的485上位程序
- golang画图库演示程序源码
- IntelCacheAccelerationSoftware,傲腾加速软件
- 昆仑通态MCGS与欧姆龙E5CC温控器通讯:PID控制及输出启停功能实现,欧姆龙E5CC温控器与昆仑通态MCGS的PID通讯方式及输出启停(KUNL-1),昆仑通态MCGS与欧姆龙E5CC温控器通讯+
- 补码计算与进制转码学习
- 《从0到1:手把手教你OpenCV下载安装秘籍》
资源上传下载、课程学习等过程中有任何疑问或建议,欢迎提出宝贵意见哦~我们会及时处理!
点击此处反馈


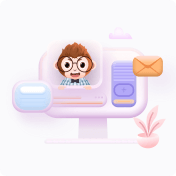