
xiaowu198809
- 粉丝: 13
- 资源: 17万+
最新资源
- 终于解决了windows的文件和文件夹的不自动刷新问题,历时数月
- OCR文字检测和识别 MMOCR PaddleOCR 环境配置,程序调试,代码复现 各种前沿文字检测和识别算法复现
- 基于反向策略的麻雀搜索算法:通过不断的生成候选位置、评估选择最佳位置、放置麻雀、回溯等步骤,逐步扩展棋盘状态,寻找解决麻雀问题的最优解 (内附改进原理文档,包您看懂,有意咨询,非诚勿扰) 基于反向策
- 8ASK调制解调通信链路matlab误码率仿真【包括程序,中文注释,程序讲解和操作视频】
- 桌上型三工位热熔机(sw08+工程图+bom)全套技术资料100%好用.zip
- 基于主从博弈的社区综合能源系统分布式协同优化运行策略 平台:Matlab+yalmip+cplex 随着能源市场由传统的垂直一体式结构向交互竞争型结构转变,社区综合能源系统的分布式特征愈发明显,传统的
- 期末操作系统期末复习资料
- 自动晾衣架sw20可编辑全套技术资料100%好用.zip
- autosar官方文档
- 数据结构线性表的顺序表示代码
- 2ASK、2FSK、2PSK、2DPSK等各种调制方式及相应的解调方式
- 雷达信号相干积累与非相干积累对比研究
- 科研工作量管理系统 JAVA毕业设计 源码+数据库+论文 Vue.js+SpringBoot+MySQL.zip
- 科研工作量管理系统 源码+数据库+论文(JAVA+SpringBoot+Vue.JS+MySQL).zip
- 情人节表白网页源码.zip
- 表白网页款式四源码.zip
资源上传下载、课程学习等过程中有任何疑问或建议,欢迎提出宝贵意见哦~我们会及时处理!
点击此处反馈


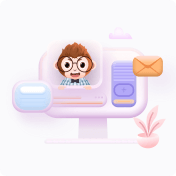