
xiaowu198809
- 粉丝: 13
- 资源: 17万+
最新资源
- linux常用命令大全.txt
- linux常用命令大全.txt
- linux常用命令大全.txt
- djyos都江堰操作系统与嵌入式系统设计
- [电子商务]BIWEB 网务通商务智能网站系统 v5.5.0_biweb_v5.5.0_sc_utf8_build090324.rar
- [电子商务]B2Bbuilder 2009.6 UTF-8_b2bbuilder.rar
- [电子商务]Buymall网上商城系统 v2.30_buymallshopv2.30.rar
- [电子商务]citySHOP 多用户商城系统 v5.2.1_trade.rar
- [电子商务]citySHOP城市多用户商城(整合Discuz!论坛) v5.6.5_cityshop5.6.5.rar
- [电子商务]EasyShop v1.2_easyshop_gb2312_v_1.2.rar
- [电子商务]Destoon B2B网站管理系统 1.0 GBK Build 20090822_destoon_1.0_gbk.rar
- [电子商务]Destoon B2B网站管理系统 1.0 UTF-8 Build 20090822_destoon_1.0_utf8.rar
- [电子商务]EasyShop V1.2繁体版_easyshop_big5_v_1.2.rar
- [电子商务]ECMall 2.0 正式版 Build 090821 GBK 简体_ecmall20final-0821-scgbk.rar
- [电子商务]ECMall 2.0 正式版 Build 090821 BIG5 繁体_ecmall20final-0821-tcbig5.rar
- [电子商务]ECShop 2.6.1 正式版 Bulid 081208 GBK_ecshop_v2.6.1_gbk_build1208.rar
资源上传下载、课程学习等过程中有任何疑问或建议,欢迎提出宝贵意见哦~我们会及时处理!
点击此处反馈


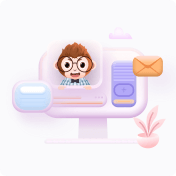