
xhr131452007
- 粉丝: 7
- 资源: 14万+
最新资源
- 创建颜色和颜色图的色调Matlab代码.rar
- 创建图形阴影 - 多个阴影和多个帧Matlab代码.rar
- 该程序选择一个 ROI,QNATIZE 到较低的位级并计算灰度级游程矩阵Matlab代码.rar
- 该程序以人眼虹膜的图像作为输入,并通过 fi 定位虹膜和瞳孔__ 关注MATLAB代码.rar
- 此 GUI 演示了用于颜色识别的机器视觉系统的概念MATLAB代码.rar
- 该程序用于将彩色图像转换为 RGB MATLAB代码.rar
- 该程序用于计算 2 个相同大小的灰度图像之间的帧间相关性Malab代码.rar
- 该程序允许用户查看 CT 或 MRI 体积图像的横截面视图Matlab代码.rar
- 该脚本可以直接从 Nanoscope 6 软件存储的文件中读取 AFM 图像数据MATLAB代码.rar
- 该脚本可以从 Nanoscope 5 软件存储的文件中读取 AFM 图像数据Matlab代码.rar
- 该软件包比较了两种 L1 正则化图像修复模型Matlab代码.rar
- 高通和低通滤波器的更平滑版本,其中空间频率阈值对应于基于高斯的滤波器的 FWHM Matlab代码.rar
- 改进的自适应复杂扩散去斑过滤器 (NCDF)Matlab代码.rar
- 骨架化和最大强度投影Matlab代码.rar
- 广义 Alpha 尺度 Alpha 空间正交滤波器Matlab代码.rar
- 各向异性扩散的稳定和正方案Matlab代码.rar
资源上传下载、课程学习等过程中有任何疑问或建议,欢迎提出宝贵意见哦~我们会及时处理!
点击此处反馈


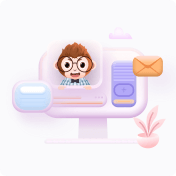