
若♡
- 粉丝: 6442
- 资源: 1万+
最新资源
- CC2530无线zigbee裸机代码实现液晶LCD显示.zip
- CC2530无线zigbee裸机代码实现中断唤醒系统.zip
- 车辆、飞机、船检测24-YOLO(v5至v11)、COCO、CreateML、Paligemma、TFRecord、VOC数据集合集.rar
- 基于51单片机的火灾烟雾红外人体检测声光报警系统(protues仿真)-毕业设计
- 高仿抖音滑动H5随机短视频源码带打赏带后台 网站引流必备源码
- 车辆、飞机、船检测25-YOLO(v5至v11)、COCO、CreateML、Paligemma、TFRecord、VOC数据集合集.rar
- 四足机器人示例代码pupper-example-master.zip
- Python人工智能基于深度学习的农作物病虫害识别项目源码.zip
- 基于MIT mini-cheetah 的四足机器人控制quadruped-robot-master.zip
- 菠萝狗四足机器人py-apple-bldc-quadruped-robot-main.zip
- 基于51单片机的篮球足球球类比赛计分器设计(protues仿真)-毕业设计
- 第3天实训任务--电子22级.pdf
- 基于FPGA 的4位密码锁矩阵键盘 数码管显示 报警仿真
- 车辆、飞机、船检测5-YOLO(v5至v11)、COCO、CreateML、Paligemma、VOC数据集合集.rar
- 河南大学(软工免浪费时间)
- NOIP-学习建议-C++
资源上传下载、课程学习等过程中有任何疑问或建议,欢迎提出宝贵意见哦~我们会及时处理!
点击此处反馈


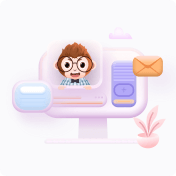