没有合适的资源?快使用搜索试试~ 我知道了~
腐蚀管道评估技术指南 DNV-RP-F101
需积分: 1 0 下载量 62 浏览量
2024-11-27
09:31:13
上传
评论
收藏 364KB PDF 举报
温馨提示
内容概要:本推荐指南由挪威船级社DNV制定,详细介绍了腐蚀损伤对海底管道系统的影响以及评估方法。主要内容涵盖了不同类型的内外腐蚀缺陷及其应对策略,重点讨论了内部压力与复合轴向加载条件下安全工作压力的估算方法。文档还包括两部分不同计算方法的具体案例说明,分别适用于不同的应用场景。此外,附录部分提供了多种缺陷情况的安全评估实例和技术细节。 适用人群:从事海洋工程领域的技术人员,如管道设计、建造、检测维护等相关工作人员。 使用场景及目标:为确保海洋工程项目中的管道设备安全可靠运行,提供科学严谨的技术支持。特别是在管道长期服役过程中因腐蚀导致的性能退化评估方面有重要指导意义。 其他说明:本文档不仅对腐蚀管段进行了详细的分析与定义,还提供了具体的数学模型和算法步骤来辅助实际操作中的决策。同时强调,在进行管道完整性管理时,需要考虑到腐蚀持续发展的可能性,并采取相应的预防措施。
资源推荐
资源详情
资源评论




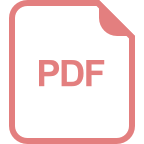














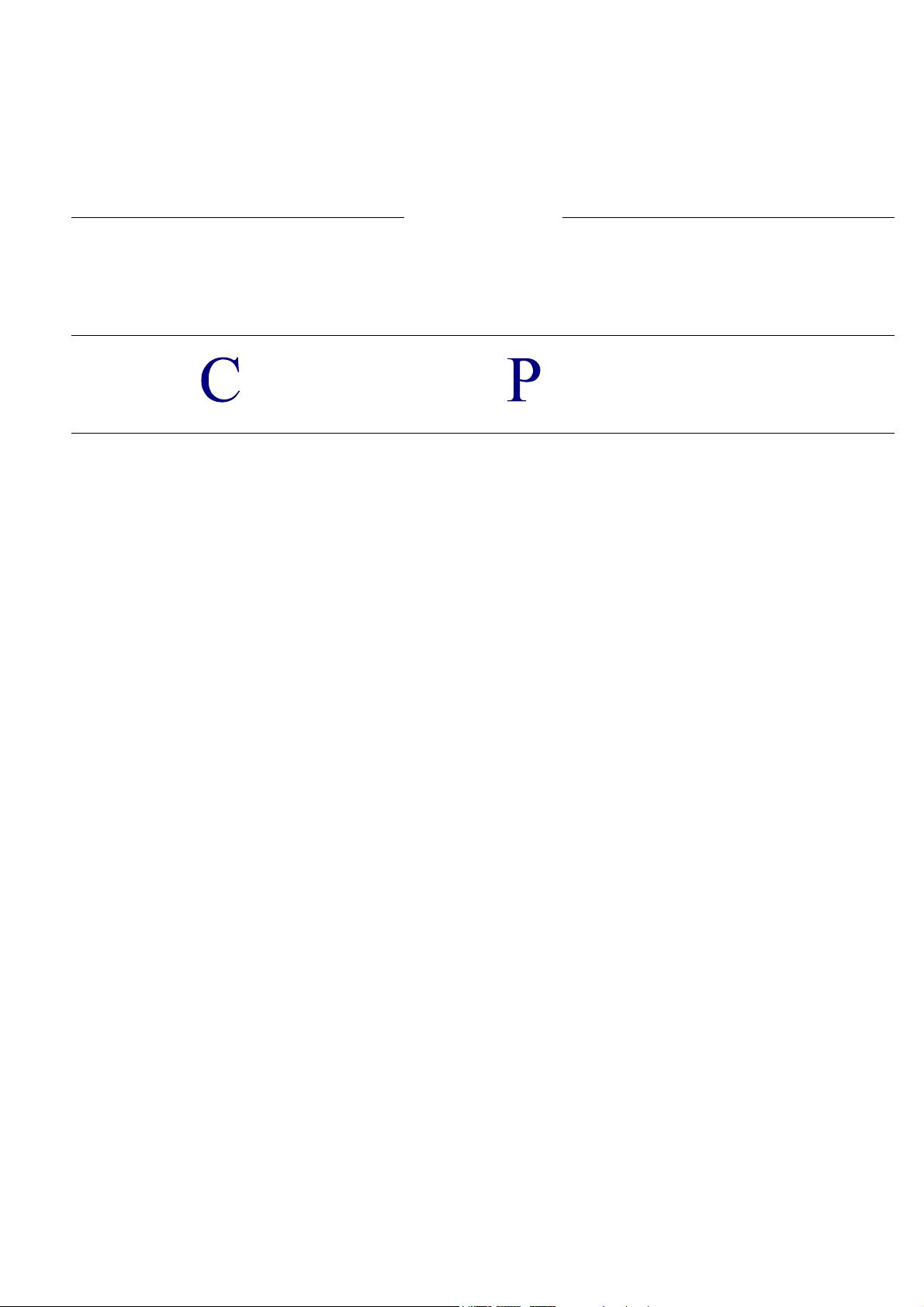
DET NORSKE VERITAS
RECOMMENDED PRACTICE
DNV-RP-F101
ORRODED IPELINES
1999
Reprint with corrections 2001
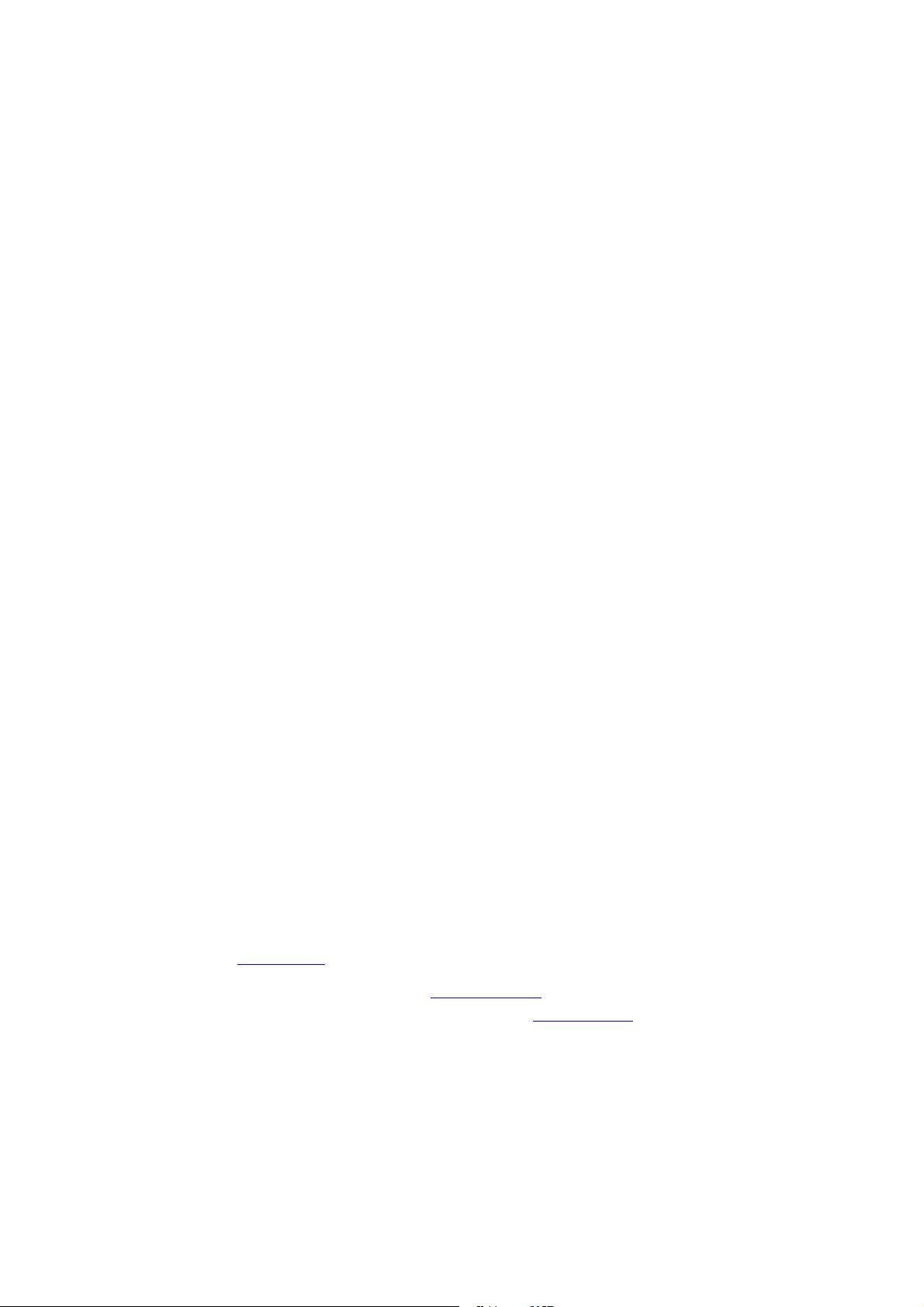
If any person suffers loss or damage which is proved to have been caused by any negligent act or omission of Det Norske Veritas, then Det Norske Veritas shall pay
compensation to such person for his proved direct loss or damage. However, the compensation shall not exceed an amount equal to ten times the fee charged for
the service in question, provided that maximum compensation shall never exceed USD 2 million. In this provision, Det Norske Veritas shall mean the Foundation
Det Norske Veritas as well as all its subsidiaries, directors, officers, employees, agents and any other acting of behalf of Det Norske Veritas.
FOREWORD
DET NORSKE VERITAS (DNV) is an autonomous and independent Foundation with the objectives of safeguarding life,
property and the environment, at sea and onshore. DNV undertakes classification, certification, and other verification and
consultancy services relating to quality of ships, offshore units and installations, and onshore industries world-wide, and
carries out research in relation to these functions.
DNV publishes various documents related to the offshore industry, aimed at promoting quality and safety on offshore units
and installations.
The Recommended Practice publications (RP-series) cover proven technology and solutions which have been found by DNV
to represent good practice, and which represent one alternative for satisfying the requirements stipulated in the DNV
Offshore Standards or other codes and standards cited by DNV. The DNV RP-series is divided into 6 parts, as follows.
A. Quality and Safety Methodology
B. Materials Technology
C. Structures
D. Systems
E. Special Facilities
F. Pipelines & Risers
As well as forming the technical basis for DNV verification services, the Offshore Standards and Recommended Practices
are offered as DNV’s interpretation of safe engineering practice for general use by the offshore industry.
ACKNOWLEDGEMENTS
This Recommended Practice is based upon a project guideline developed in a co-operation between BG Technology and
DNV. The results from their respective Joint Industry Projects (JIP) have been merged and form the technical basis for this
Recommended Practice.
We would like to take this opportunity to thank the sponsoring companies / organisations for their financial and technical
contributions (listed in alphabetical order):
- BG plc
- BP Amoco
- Health and Safety Executive, UK
- Minerals Management Service (MMS)
- Norwegian Petroleum Directorate (NPD)
- PETROBRAS
- Phillips Petroleum Company Norway and Co-Ventures
- Saudi Arabian Oil Company
- Shell UK Exploration and Production, Shell Global Solutions, Shell International Oil Products B.V.
- Statoil
- Total Oil Marine plc
DNV is grateful for valuable co-operations and discussions with the individual personnel of these companies.
Comments may be sent by e-mail to dtp203@dnv.com .
For subscription orders or information about subscription terms, please use distribution@dnv.com .
Comprehensive information regarding DNV services, research and publications can be found at http://www.dnv.com, or can be obtained from DNV,
Veritasveien 1, N-1322 Høvik, Norway; Tel +47 67 57 99 00, Fax +47 67 57 99 11.
© 2001 DET NORSKE VERITAS. All rights reserved. No part of this publication may be reproduced or transmitted in any form or by any means,
including photocopying and recording, without the prior written consent of DET NORSKE VERITAS.
Printed in Norway by Det Norske Veritas
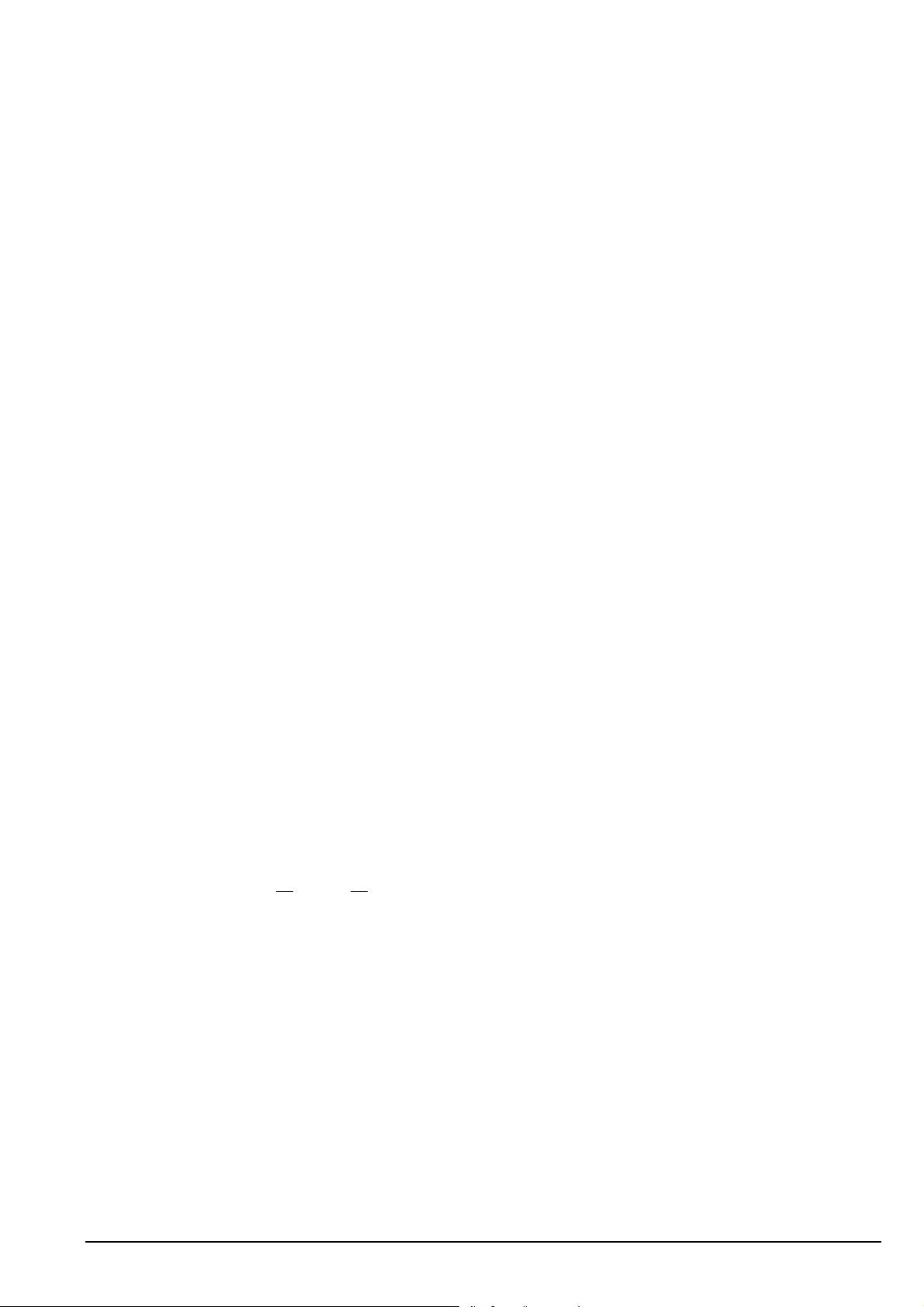
DET NORSKE VERITAS
CONTENTS
1. General ..................................................................4
1.1 Introduction ..........................................................4
1.2 BG plc and DNV Research Projects.......................4
1.3 Application ...........................................................4
1.4 Structure of RP......................................................4
1.5 Applicable Defects................................................4
1.6 Applied Loads.......................................................5
1.7 Exclusions.............................................................5
1.8 Other failure modes...............................................5
1.9 Further Assessment...............................................5
1.10 Responsibility .......................................................5
1.11 Validation .............................................................5
1.12 Definitions............................................................6
1.13 Symbols and Abbreviations...................................6
1.14 Units.....................................................................7
2. Part A - Partial Safety Factor................................8
2.1 Introduction ..........................................................8
2.2 Reliability Levels ..................................................8
2.3 Inspection Sizing Accuracy....................................8
2.4 Partial Safety Factors and Fractile Values ..............8
2.5 Material Grade and material requirements..............9
2.6 Relative Depth Measurement.................................9
2.7 Absolute Depth Measurement..............................10
2.8 Circumferential Corrosion ...................................11
2.9 Usage Factors for Longitudinal Stress..................11
2.10 System Effect......................................................11
3. Assessment of a Single Defect (Part A)................12
3.1 Requirements......................................................12
3.2 Longitudinal Corrosion Defect, Internal Pressure
Loading Only......................................................12
3.3 Longitudinal Corrosion Defect, Internal Pressure
and Superimposed Longitudinal Compressive
Stresses...............................................................12
The corrections in this reprint are non-technical and
listed below.
Section 1.3 Typo: … code is not violated (not was missing).
Section 1.11 Typo: 914.4 (26") changed to 914.4 (36").
Section 1.13
Added definition of σ
F
.
Section 3.3 Added reference to a recent paper describing the
development of the method for superimposed
loading.
Section 10 Typo: Corrected title for reference /4/.
Added reference /17/.
Figure 16 Modified figure 16, easier to read.
Appendix D Corrected typo in STEP 2, where parts of the
equations were not shown.
Included reference to safety factor approach in
PD6493 Appendix A.
Included comments to the flow stress definition.
Whole doc. Obvious typos are corrected. Formats, as
shading etc. in figures are changed.
-o0o-
3.4 Circumferential Corrosion Defects, Internal
Pressure and Superimposed Longitudinal
Compressive Stresses...........................................13
4. Assessment of interacting defects (Part A)..........14
4.1 Requirements ......................................................14
4.2 Allowable Corroded Pipe Pressure Estimate.........14
5. Assessment of Complex Shaped Defects (Part A)16
5.1 Requirements ......................................................16
5.2 Allowable Corroded Pipe Pressure Estimate.........16
6. Part B - Allowable Stress Approach....................19
6.1 Introduction.........................................................19
6.2 Total Usage Factor ..............................................19
7. Assessment of a Single Defect (Part B)................20
7.1 Requirements ......................................................20
7.2 Safe Working Pressure Estimate - Internal Pressure
Only....................................................................20
7.3 Safe Working Pressure Estimate - Internal Pressure
and Combined Compressive Loading...................20
8. Assessment of Interacting Defects (Part B) .....22
8.1 Requirements ......................................................22
8.2 Safe Working Pressure Estimate ..........................22
9. Assessment of a Complex Shaped Defect
(Part B) ................................................................24
9.1 Requirements ......................................................24
9.2 Safe Working Pressure Estimate ..........................24
10. References............................................................26
Appendix A Examples for Part A ..................................34
Appendix B Examples for Part B...................................40
Appendix C Correlated and uncorrelated
Measurements of Wall Thickness loss.......47
Appendix D The assessment of single defects subject
to internal pressure plus bending loads
and/or tensile longitudinal loads ...............49
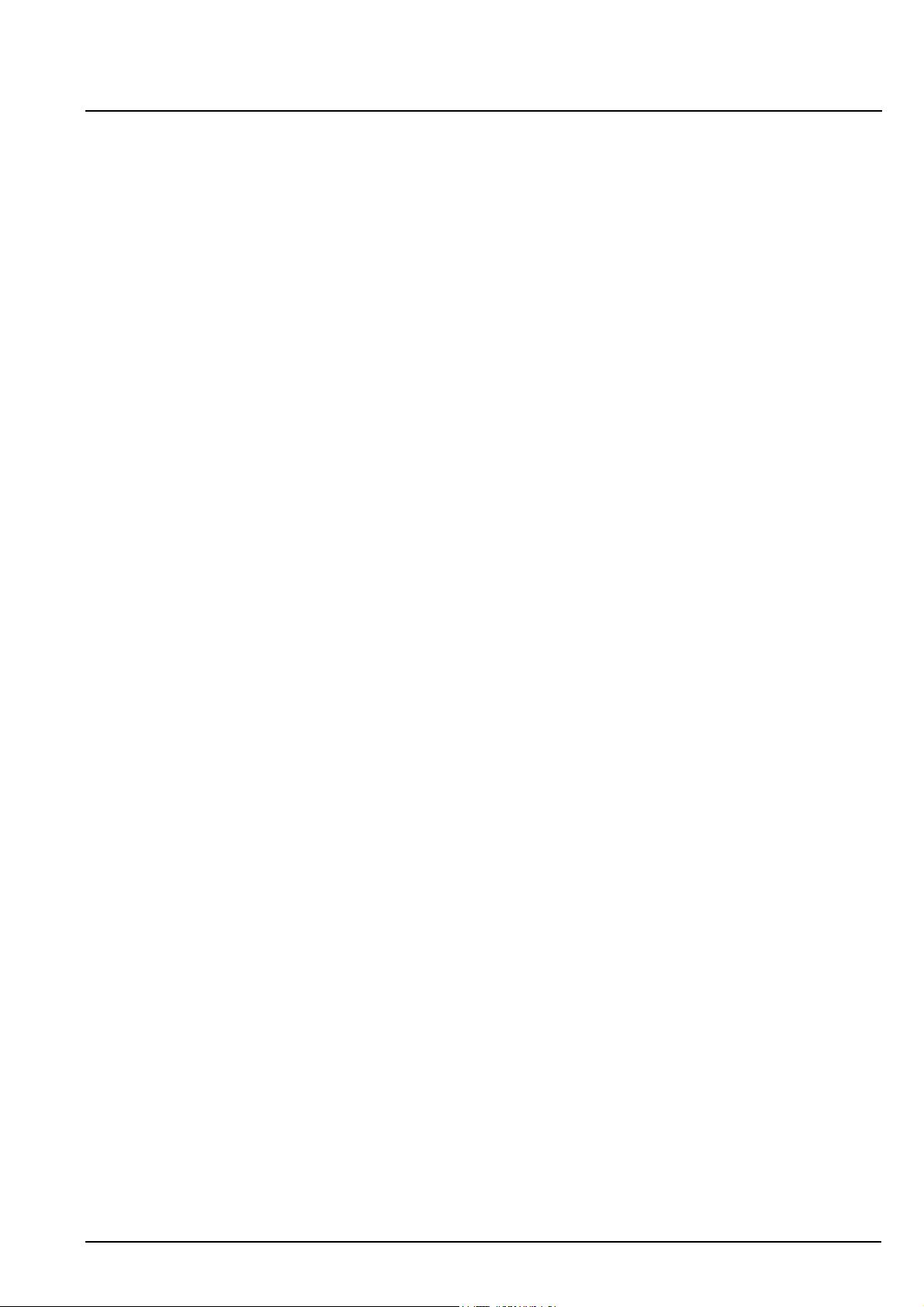
4 Recommended Practice DNV-RP-F101
April 1999
DET NORSKE VERITAS
1. General
1.1 Introduction
This document provides recommended practice for assessing
pipelines containing corrosion. Recommendations are given
for assessing corrosion defects subjected to:
1) Internal pressure loading only.
2) Internal pressure loading combined with longitudinal
compressive stresses.
This Recommended Practice (RP) document describes two
alternative approaches to the assessment of corrosion, and
the document is divided into two parts. The main difference
between the two approaches is in their safety philosophy:
− The first approach, given in Part A, is in accordance to
the safety philosophy adopted in the DNV Offshore
Standard DNV-OS-F101, Submarine Pipeline Systems
(/8/). This part of the RP is a supplement to, and
complies with, DNV-OS-F101. Uncertainties associated
with the sizing of the defect depth and the material
properties are specifically considered. Probabilistic
calibrated equations (with partial safety factors) for the
determination of the allowable operating pressure of a
corroded pipeline are given.
− The second approach, given in Part B, is based on the
ASD (Allowable Stress Design) format. The failure
pressure (capacity) of the corrosion defect is calculated,
and this failure pressure is multiplied by a single usage
factor based on the original design factor. Consideration
of the uncertainties associated with the sizing of the
corrosion defect is left to the judgement of the user.
1.2 BG plc and DNV Research Projects
This document is a result of co-operation between BG
Technology (part of BG plc) and DNV. The results from
their respective joint industry projects have been merged, and
form the technical basis for this recommended practice
(/3/,/4/ and /16/).
The BG Technology project generated a database of more
than 70 burst tests on pipes containing machined corrosion
defects (including single defects, interacting defects and
complex shaped defects), and a database of linepipe material
properties. In addition, a comprehensive database of 3D
non-linear finite element analyses of pipes containing defects
was produced. Criteria were developed for predicting the
remaining strength of corroded pipes containing single
defects, interacting defects and complex shaped defects.
The DNV project generated a database of 12 burst tests on
pipes containing machined corrosion defects, including the
influence of superimposed axial and bending loads on the
failure pressure. A comprehensive database of 3D non-linear
finite element analyses of pipes containing defects was also
produced. Probabilistic methods were utilised for code
calibration and the determination of partial safety factors.
1.3 Application
The methods provided in this document are intended to be
used on corrosion defects in carbon steel pipelines (not
applicable for other components) that have been designed to
the DNV Offshore Standard DNV-OS-F101 Submarine
Pipeline Systems, /8/,/9/ or other recognised pipeline design
code as (but not limited to) ASME B31.4 /1/, ASME B31.8
/2/, BS8010 /5/, IGE/TD/1 /10/, ISO/DIS 13623 /11/,
CSA Z662-94 /7/, provided that the safety philosophy is the
design code is not violated.
When assessing corrosion, the effect of continued corrosion
growth should be considered. If a corroded region is to be
left in service then measures should be taken to arrest further
corrosion growth, or an appropriate inspection programme
should be adopted. The implications of continuing defect
growth are outside the scope of this document.
This RP does not cover every situation that requires a fitness-
for-purpose assessment and further methods may be
required.
1.4 Structure of RP
The RP describes two alternative approaches. The first
approach is given in Part A, which consists of section 2
through 5. The second approach is given in Part B, which
consists of section 6 through 9.
A flow chart describing the assessment procedure (for both
Part A and Part B) is shown in Figure 5.
Worked examples are given in Appendix A for the methods
described in Part A. and Appendix B (for the methods
described in Part B).
1.5 Applicable Defects
The following types of corrosion defect can be assessed
using this document:
1) Internal corrosion in the base material.
2) External corrosion in the base material.
3) Corrosion in seam welds.
4) Corrosion in girth welds.
5) Colonies of interacting corrosion defects.
6) Metal loss due to grind repairs (provided that the
grinding leaves a defect with a smooth profile, and that
the removal of the original defect has been verified using
appropriate NDT methods).
When applying the methods to corrosion defects in seam
welds and girth welds, it should be demonstrated that there
are no significant weld defects present that may interact with
the corrosion defect, that the weld is not undermatched, and
that the weld has an adequate toughness.
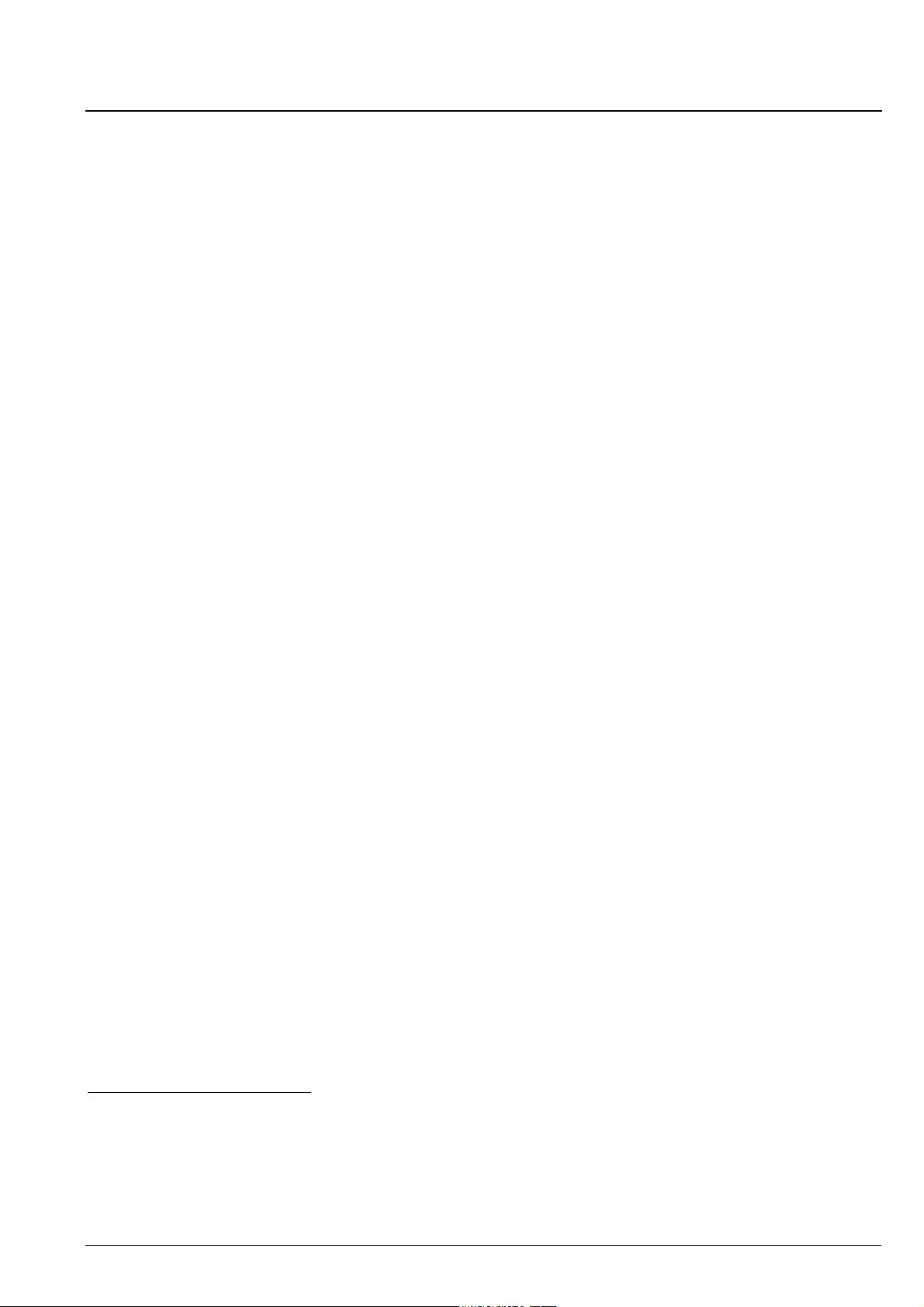
Recommended Practice DNV-RP-F101 5
April 1999
DET NORSKE VERITAS
1.6 Applied Loads
Internal pressure, and axial and/or bending loads may
influence the failure of a corroded pipeline. The following
combinations of loading/stresses and defects are covered by
this RP:
Internal pressure loading for:
1) Single defect
2) Interacting defects
3) Complex shaped derfects
Internal pressure loading and combined with longitudinal
compressive stresses for:
1) Single defects
The compressive longitudinal stress can be due to axial
loads, bending loads, temperature loads etc..
Methods for assessing defects under combined internal
pressure and tensile longitudinal stresses are given in
Appendix D for the ASD approach (Part B).
The recommended practice given in this document is
confined to the effects of internal pressure and compressive
longitudinal loading on longitudinal failure because the
validation of these effects was addressed in the DNV and
BG Technology projects.
The behaviour of corrosion defects under combined internal
pressure and bending loads, and/or tensile longitudinal loads,
was outside the scope of the DNV and BG Technology
projects and, therefore, this loading combination has not
been included as part of the RP. Methods for assessing
defects under combined internal pressure and bending loads,
and/or tensile longitudinal loads, are recommended in other
documents (e.g. /6/ and /12/). These methods have been
included in Appendix D, in a format compatible with the rest
of this document, for those who wish to use these methods.
1.7 Exclusions
The following are outside the scope of this document:
1) Materials other than carbon linepipe steel.
2) Linepipe grades in excess of X80
1
.
3) Cyclic loading.
4) Sharp defects (i.e. cracks)
2
.
5) Combined corrosion and cracking.
6) Combined corrosion and mechanical damage.
7) Metal loss defects attributable to mechanical damage
(e.g. gouges)
3
.
8) Fabrication defects in welds.
9) Defect depths greater than 85% of the original wall
thickness (i.e. remaining ligament is less than 15% of the
original wall thickness).
1
The validation of the assessment methods comprised full scale tests on
grades up to X65, and material tests on grades up to X80 (inclusive).
2
Cracking, including environmentally induced cracking such as SCC
(stress corrosion cracking), is not considered here. Guidance on the
assessment of crack-like corrosion defects is given in References 8, 9, 10.
3
Metal loss defects due to mechanical damage may contain a work
hardened layer at their base and may also contain cracking.
The assessment procedure is only applicable to linepipe
steels that are expected to fail through plastic collapse. The
procedure is not recommended for applications where
fracture is likely to occur. These may include:
10) Any material that has been shown to have a transition
temperature above the operating temperature.
11) Material of thickness greater than 12.7 mm (1/2"), unless
the transition temperature is below the operating
temperature.
12) Defects in bond lines of flash welded (FW) pipe.
13) Lap welded or furnace butt welded pipe.
14) Semi-killed steels.
1.8 Other failure modes
Other failure modes, such as buckling, wrinkling, fatigue and
fracture, may need to be considered. These failure modes are
not addressed in this document, and other methods may be
applicable, ref., (/6/, /12/, /14/).
1.9 Further Assessment
The intent of this RP is to provide simplified procedures for
the assessment of corroded pipe. The results of the analysis
should be conservative. If the corrosion defects are not
found to be acceptable using the procedures given in this RP,
then the user has the option of considering an alternative
course of action to more accurately assess the remaining
strength of the corroded pipeline. This could include, but is
not limited to, detailed finite element analysis and/or full
scale testing.
1.10 Responsibility
It is the responsibility of the user to exercise independent
professional judgement in application of this recommended
practice. This is particularly important with respect to the
determination of defect size and associated sizing
uncertainties.
1.11 Validation
The methods given in this RP for assessing corrosion under
internal pressure loading only have been validated against
138 full scale vessel tests, including both machined defects
and real corrosion defects. The range of test parameters is
summarised below:
Pipeline:
Pipe Diameter, mm 219.1 (8") to 914.4 (36")
Wall Thickness, mm 3.40 to 25.40
D/t ratio 8.6 to 149.4
Grade (API/5L) X42 to X65
Defects:
d/t 0 to 0.97
l/(Dt)
0.5
0.44 to 35
c/t (circumferential) 0.01 to 22
(Shortest defect was l= 2.1 t)
For nomenclature, see section 1.13.
剩余49页未读,继续阅读
资源评论
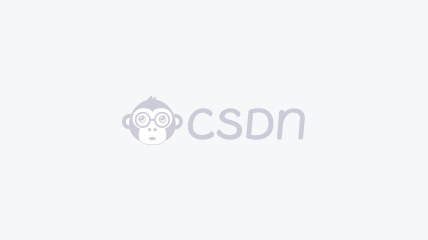

weixin_3633
- 粉丝: 0
- 资源: 5
上传资源 快速赚钱
我的内容管理 展开
我的资源 快来上传第一个资源
我的收益
登录查看自己的收益我的积分 登录查看自己的积分
我的C币 登录后查看C币余额
我的收藏
我的下载
下载帮助

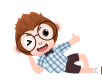
最新资源
- FDR InfiniBand技术创新及其对高性能计算与数据中心网络性能优化的应用
- Ue5+Vue3像素流,保姆级教程
- COMSOL V6.0仿真研究流体对电火花放电或电弧的影响:击穿放电后等离子体行为分析,comsol仿真流体对电火花放电或电弧的影响 版本6.0,问前询问清楚,联系不 不 模拟击穿放电后等离子体受电
- Java毕业设计-springboot-vue-教学辅助平台(源码+sql脚本+29页零基础部署图文详解+28页论文+环境工具+教程+视频+模板).zip
- Java毕业设计-springboot-vue-江理工文档管理系统(源码+sql脚本+29页零基础部署图文详解+31页论文+环境工具+教程+视频+模板).zip
- 基于Multisim14的直流可调稳压电源设计仿真报告:集成芯片实现0~15V大功率稳压,过压过流保护及电源指示功能,模电 直流可调稳压电源设计 Multisim14 仿真报告 利用三极管、二极管基本
- 基于ssm+jsp简易版营业厅宽带系统源码数据库.doc
- Java毕业设计-springboot-vue-可盈保险合同管理系统(源码+sql脚本+29页零基础部署图文详解+31页论文+环境工具+教程+视频+模板).zip
- Java毕业设计-springboot-vue-科研工作量管理系统(源码+sql脚本+29页零基础部署图文详解+31页论文+环境工具+教程+视频+模板).zip
- Java毕业设计-springboot-vue-景区民宿预约系统(源码+sql脚本+29页零基础部署图文详解+36页论文+环境工具+教程+视频+模板).zip
- 数据互连技术InfiniBand市场分析与未来展望(2007-2011)
- Java毕业设计-springboot-vue-客户关系管理系统(源码+sql脚本+29页零基础部署图文详解+31页论文+环境工具+教程+视频+模板).zip
- Java毕业设计-springboot-vue-林业产品推荐系统(源码+sql脚本+29页零基础部署图文详解+37页论文+环境工具+教程+视频+模板).zip
- 华为ensp单臂路由实验
- java-jsp宠物领养管理系统计算机毕业设计程序.zip
- 源自由无监督领域适应语义分割中的稳定邻居去噪算法(CVPR 2024)
资源上传下载、课程学习等过程中有任何疑问或建议,欢迎提出宝贵意见哦~我们会及时处理!
点击此处反馈


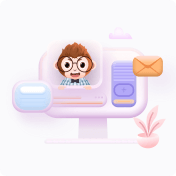
安全验证
文档复制为VIP权益,开通VIP直接复制
