
拉拉庸
- 粉丝: 21
- 资源: 66万+
最新资源
- 基于BS模式的冷链物流系统pf-springboot毕业项目,适合计算机毕-设、实训项目、大作业学习.zip
- 基于simulink实现的110kV继电保护设计实现
- 这个程序是一个简单的git代理切换器,它的主要功能是帮助用户在需要代理的网络环境和不需要代理的网络环境之间快速切换
- java javacv jt1078 rtp流转flv
- iClient for Classic加载wmts山东天地图示例demo
- lvgl-v7版本代码示例
- 基于模型预测控制的无人驾驶车辆轨迹跟踪问题研究,matlab 附有MATLAB程序与详细的建模过程,研究车辆转向的同学可以作为参考
- 基于SpringBoot+vue的名城小区物业管理系统(含报告).zip
- Xmanager Power Suite 8.0.0005
- 阅后即焚平台系统PHP源码
- C#读写西门子PLC.OPC.数据库.Socket 1、PLC数据通信读写; 2、联合OPC; 3、联合Socket; 4、联合数据库;
- 德普微一级代理 DP023N10TGN TOLL DPMOS N-MOSFET 100V 300A 1.75mΩ
- 在线教育网校系统社区版+带安装说明
- 基于Spring+vue的智慧生活商城系统.zip
- 高可用k8s集群离线部署(五)
- 基于Java的考试系统代码pf-springboot毕业项目,适合计算机毕-设、实训项目、大作业学习.rar
资源上传下载、课程学习等过程中有任何疑问或建议,欢迎提出宝贵意见哦~我们会及时处理!
点击此处反馈


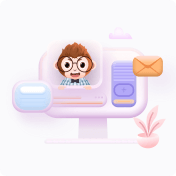