
拉拉庸
- 粉丝: 22
- 资源: 66万+
最新资源
- 【world bank wroup-2025研报】世界银行-经济快速增长但贫困隔离加剧:越南能否实现公平发展的可持续发展目标?(英).pdf
- 【Fortinet-2025研报】2025年网络威胁趋势预测报告.pdf
- 【世界银行-2025研报】能源价格、能源强度和企业绩效(英).pdf
- 【深交所-2025研报】粤高速B:2024年年度报告(英文版).pdf
- 【之诺咨询-2025研报】全球云计算市场研究系列2025年第一期.pdf
- 【莱坊-2025研究报告】Sydney CBD Office Market February 2025.pdf
- 【European Central Bank-2025研报】欧洲央行-欧洲与世界经济(英).pdf
- 【未来能源研究所-2025研报】建立技术绩效保险市场的政策(英).pdf
- 【艾瑞咨询-2025研报】iR-跨境出海行业周度市场观察-2025年第7周.pdf
- 【猎聘-2025研报】2025+AI技术人才供需洞察报告-猎聘.pdf
- 基于Spring Boot的在线拍卖系统设计与实现
- 信捷XC PLC与西门子V20变频器通讯程序:实现精准控制及状态指示,附触摸屏程序与详细设置指南,信捷XC PLC与西门子V20变频器通讯程序:实现精准控制及状态指示,附触摸屏程序与详细设置指南,信捷
- 全国各个省市区 json
- https://blog.csdn.net/cb181002/article/details/146073112?spm=1001.2014.3001.5501
- 起源视频播放器安装包,刚出炉不久的视频播放器
- 厦门大学智能信息检索实验数据
资源上传下载、课程学习等过程中有任何疑问或建议,欢迎提出宝贵意见哦~我们会及时处理!
点击此处反馈


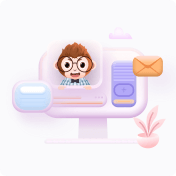