
拉拉庸
- 粉丝: 21
- 资源: 66万+
最新资源
- opc da 转opc ua 、opc 隧道软件 注意:这是两个软件,安装在同一个机器上,可以实现opc da转 opc ua 安装在两个计算机上就可以实现opc tunnel功能,不需要配置d
- java Springboot网上音乐商城(源码+sql+论文)-springboot毕业项目,适合计算机毕-设、实训项目、大作业学习.zip
- 档案管理系统_g2p7x--论文-springboot毕业项目,适合计算机毕-设、实训项目、大作业学习.zip
- ffmpeg and EasyDarwin
- elk-demo 代码例子,123 45678
- 大学生创新创业训练项目管理系统设计与实现-springboot毕业项目,适合计算机毕-设、实训项目、大作业学习.zip
- 大健康养老公寓管理系统_to14d-springboot毕业项目,适合计算机毕-设、实训项目、大作业学习.zip
- 大学新生报到系统的设计与实现-springboot毕业项目,适合计算机毕-设、实训项目、大作业学习.zip
- 基于Hadoop的高校固定资产管理系统研究与实现_hot14-springboot毕业项目,适合计算机毕-设、实训项目、大作业学习.zip
- 基于Java的大学生迎新系统-springboot毕业项目,适合计算机毕-设、实训项目、大作业学习.zip
- JavaSpringboot+vue图书购物商城管理系统(源码+sql+论文)-springboot毕业项目,适合计算机毕-设、实训项目、大作业学习.rar
- JavaSpringboot学生教务管理系统(源码+sql+文档)-springboot毕业项目,适合计算机毕-设、实训项目、大作业学习.zip
- 个性化电影推荐系统-springboot毕业项目,适合计算机毕-设、实训项目、大作业学习.zip
- 儿童性教育网站-springboot毕业项目,适合计算机毕-设、实训项目、大作业学习.zip
- JavaSpringboot+vur前后端分离党员信息管理系统(源码+sql+论文)-springboot毕业项目,适合计算机毕-设、实训项目、大作业学习.rar
- 430大神asp.net基于三层商品进销存管理系统毕业课程源码设计
资源上传下载、课程学习等过程中有任何疑问或建议,欢迎提出宝贵意见哦~我们会及时处理!
点击此处反馈


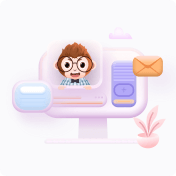