
拉拉庸
- 粉丝: 21
- 资源: 66万+
最新资源
- MATLAB代码《基于多智能体系统一致性算法的电力系统分布式经济调度》 软件环境:MATLAB 内容:集中式优化方法难以应对未来电网柔性负荷广泛渗透以及电力元件“即插即用”的技术要求 区别于集中式经
- Listary pro(文件搜索增强工具) v6.1.0.38 PJ版
- 无线电能传输 wpt 磁耦合谐振 过零检测 matlab simulink仿真 pwm MOSFET,过零检测模块 基于二极管整流的无线电能传输设计 基于同步整流的无线电能传输设计(含过零比较
- 混合动力汽车能量管理策略(DP-ECMS-PMP)搭建指导说明
- 全自动铝型材切割机 直切斜切一体机sw18可编辑全套技术资料100%好用.zip
- 电机标幺化、PI标幺化、锁相环PLL标幺化 详解电机模型相关标幺化处理 电流环PI控制器的标幺化处理 观测器中PLL锁相环的标幺化处理 采样时间处理 这是文档,不是代码,文档中的代码均为引用举例子的
- 全自动尼龙拉链超音波切断机(sw10可编辑+工程图+BOM)全套技术资料100%好用.zip
- 初始安全命令,方便网友查询并给予笔者返回
- abaqus轮胎建模仿真 轮胎仿真建模 基于hypermesh和abaqus联合轮胎仿真教学,hypermesh前处理,inp文件属性赋予+工作步设置,abaqus计算,有轮胎的inp文件 1.模
- electron-builder 打包setup安装程序所需包
- COMSOL注浆( 1comsol模拟随机裂隙注浆,浆液在多孔介质和裂隙中扩散,考虑浆液粘度时变性 2浆液在多孔介质和裂隙中流动 裂隙为浆液流动的优势通道,明显快与无裂隙的基质通道 注:
- r vr age.csv
- 精品-基于STM32F103的智能机械臂识别与控制项目(课件PPT+源代码).zip
- aadfhjglfdkgkbssss
- 源代码用 Amazon Bedrock 与 Nova 大模型构建客户之声解决方案
- fluent金属熔凝最强学习资料 1.流动传热传质 2.激光移动热源 3.金属熔化凝固 4.宏观偏析 5.激光熔覆 6.udf代码讲解
资源上传下载、课程学习等过程中有任何疑问或建议,欢迎提出宝贵意见哦~我们会及时处理!
点击此处反馈


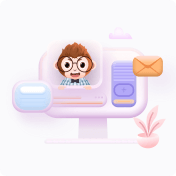