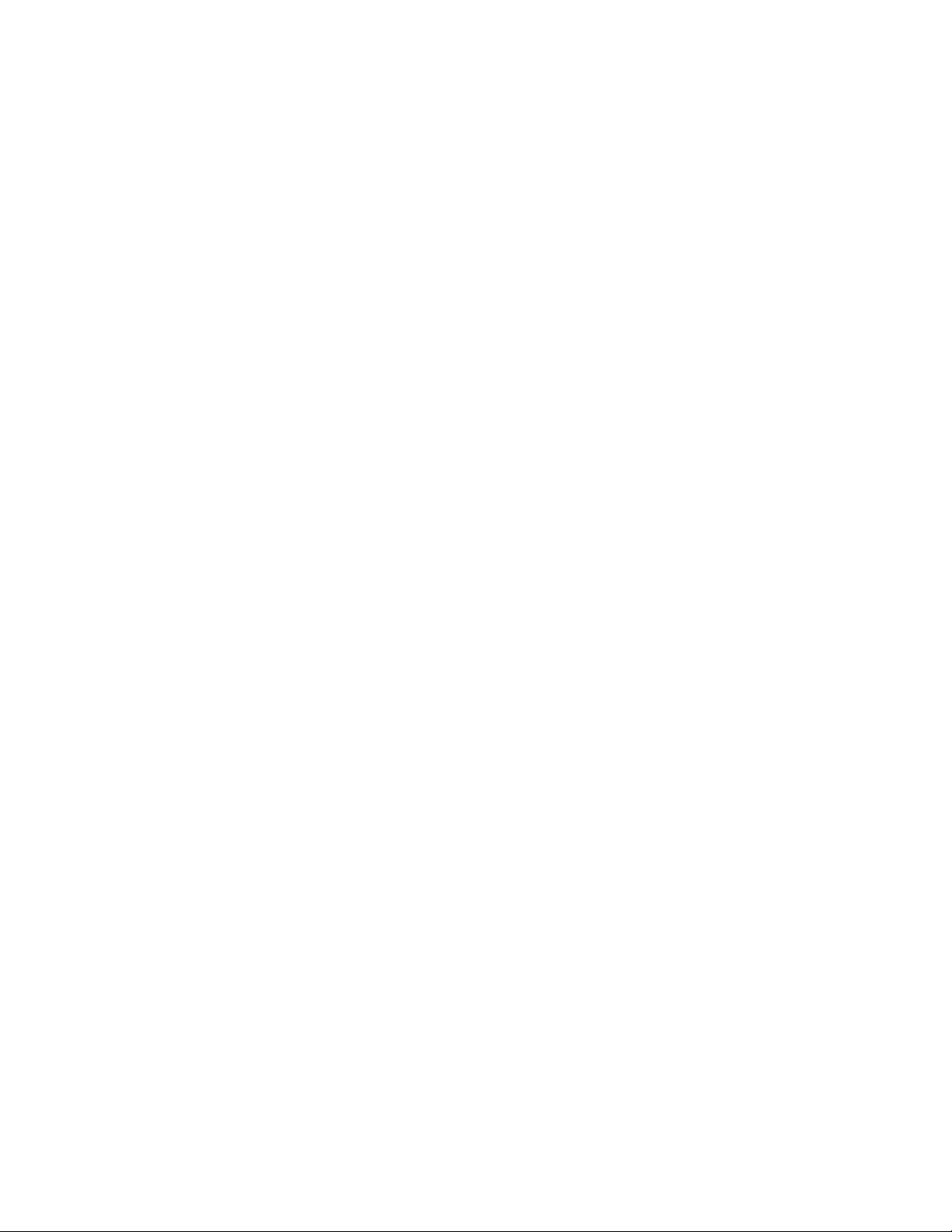
Introduction
The motor control industry is a strong, aggressive sector. To remain competitive new products must
address several design constraints including cost reduction, power consumption reduction, power factor
correction, and reduced EMI radiation. In order to meet these challenges advanced control algorithms
are necessary. Embedded control technology allows both a high level of performance and system cost
reduction to be achieved. According to market analysis, the majority of industrial motor applications
use AC induction motors. The reasons for this are higher robustness, higher reliability, lower prices and
higher efficiency (up to 80%) on comparison with other motor types. However, the use of induction
motors is challenging because of its complex mathematical model, its non linear behavior during
saturation and the electrical parameter oscillation which depends on the physical influence of the
temperature. These factors make the control of induction motor complex and call for use of a high
performance control algorithms such as “vector control” and a powerful microcontroller to execute this
algorithm.
During the last few decades the field of controlled electrical drives has undergone rapid expansion due
mainly to the benefits of micro-controllers. These technological improvements have enabled the
development of very effective AC drive control with lower power dissipation hardware and more
accurate control structures. The electrical drive controls become more accurate in the sense that not
only are the DC quantities controlled but also the three phase AC currents and voltages are managed
by so-called vector controls. This document briefly describes the implementation of the most efficient
form of a vector control scheme: the Field Orientated Control method. It is based on three major points:
the machine current and voltage space vectors, the transformation of a three phase speed and time
dependent system into a two coordinate time invariant system and effective Space Vector Pulse Width
Modulation pattern generation. Thanks to these factors, the control of AC machine acquires every
advantage of DC machine control and frees itself from the mechanical commutation drawbacks.
Furthermore, this control structure, by achieving a very accurate steady state and transient control,
leads to high dynamic performance in terms of response times and power conversion.
Induction Motors
Induction motors derive their name from the way the rotor magnetic field is created. The rotating stator
magnetic field induces currents in the short circuited rotor. These currents produce the rotor magnetic
field, which interacts with the stator magnetic field, and produces torque, which is the useful mechanical
output of the machine.
The three phase squirrel cage AC induction motor is the most widely used motor. The bars forming the
conductors along the rotor axis are connected by a thick metal ring at the ends, resulting in a short
circuit as shown in Fig.1. The sinusoidal stator phase currents fed in the stator coils create a magnetic
field rotating at the speed of the stator frequency (
ω
s
). The changing field induces a current in the cage
conductors, which results in the creation of a second magnetic field around the rotor wires. As a
consequence of the forces created by the interaction of these two fields, the rotor experiences a torque
and starts rotating in the direction of the stator field.
As the rotor begins to speed up and approach the synchronous speed of the stator magnetic field, the
relative speed between the rotor and the stator flux decreases, decreasing the induced voltage in the
stator and reducing the energy converted to torque. This causes the torque production to drop off, and
the motor will reach a steady state at a point where the load torque is matched with the motor torque.
This point is an equilibrium reached depending on the instantaneous loading of the motor. In brief:
2
评论0