
weixin_38744375
- 粉丝: 373
- 资源: 2万+
最新资源
- 预计2030年全球青光眼分流器市场规模将达到21.6亿美元
- 预计2030年全球扫地机器人市场规模将达到87.8亿美元
- 2024年心灵状态全球报告-Six Seconds-2024-49页.pdf
- imobie DroidKit v2.3.2.20250一款(亲测有效)非常不错的安卓手机数据恢复软件.rar
- 预计2030年全球深层过滤纸板市场规模将达到1亿美元
- 预计2030年全球湿度计市场规模将达到1.7亿美元
- 使用gurobi排产建模
- 工业互联网平台发展指数2024
- 预计2030年全球食品和饮料工业消毒和清洁剂市场规模将达到26.2亿美元
- 两级式三相光伏并网逆变器的Simulink仿真 光伏pv+Boost+三相并网逆变器+LCL滤波器 PLL锁相环 MPPT最大功率点跟踪控制(扰动观察法和电导增量法可切) dq解耦控制 电流内环电压外
- 非煤矿山建设项目安全设施设计编写提纲
- c#语言编写的上位机控制软件,空压机项目 采用modbus rtu协议与西门子plc s7 200smart进行通讯 联合SQL server数据库进行数据存储,针对数据库操作增删改查功能 数据存储
- eap2025010741566905-1-1.pdf
- pt100温度变送器,支持k型热电偶 4-20mA输出全套方案资料 2线、3线、隔离型 (样板是2线电流 0-10V输出) 0-5V 0-10V输出 国产24位ADC精度0.01度,国产12位DAC
- 有源电力滤波器仿真,谢波检测用ipiq法,控制包括电流控制(滞环)电压控制(pi),驱动电路pwm,有原理全套,单独仿真,仿真失真度从25%降到2%左右整体加pq法ipiq法仿真
- 学术会议poster模板
资源上传下载、课程学习等过程中有任何疑问或建议,欢迎提出宝贵意见哦~我们会及时处理!
点击此处反馈


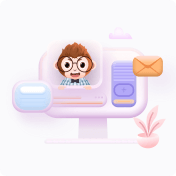