
weixin_38743602
- 粉丝: 396
- 资源: 2万+
最新资源
- 手套手势检测7-YOLO(v5至v11)、COCO、CreateML、Paligemma、TFRecord、VOC数据集合集.rar
- CentOS bridge 工具包 bridge-utils-1.6-1.33.x86-64.rpm
- 手势检测7-YOLO(v5至v11)、COCO、CreateML、Paligemma、TFRecord、VOC数据集合集.rar
- 基于python flask实现某瓣数据可视化数据分析平台
- awewq1132323
- 手写流程图检测31-YOLO(v5至v8)、COCO、CreateML、Darknet、Paligemma、TFRecord数据集合集.rar
- frida拦截微信小程序云托管API
- 肝脏及其肿瘤分割的 CT 数据集,已经切片成jpg数据,约2w张数据和mask
- 基于Java的网上教务评教管理系统的设计与实现.doc
- 2024圣诞节海外消费市场趋势及营销策略分析报告
资源上传下载、课程学习等过程中有任何疑问或建议,欢迎提出宝贵意见哦~我们会及时处理!
点击此处反馈


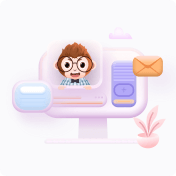