没有合适的资源?快使用搜索试试~ 我知道了~
资源推荐
资源详情
资源评论
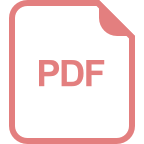
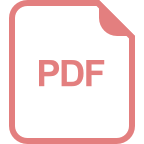
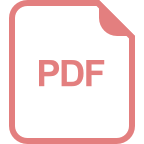
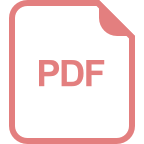
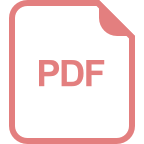
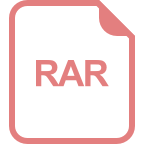
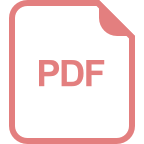
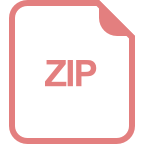
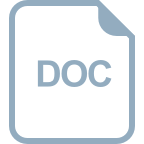
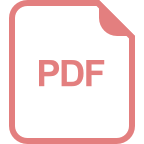
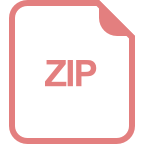
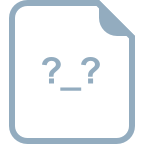
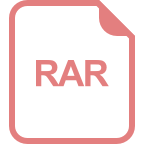
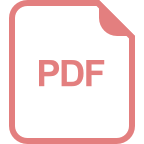
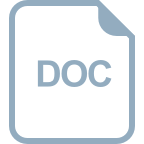
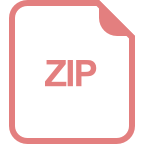
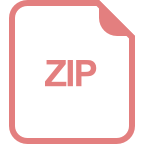
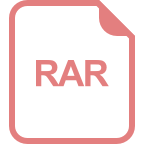
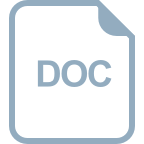
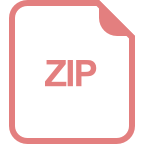
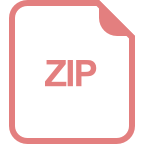
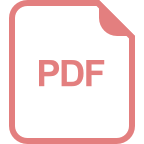
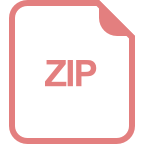
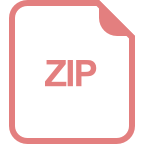
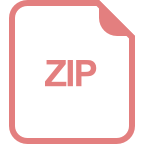
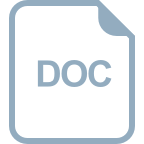
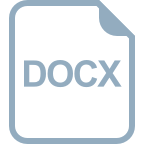
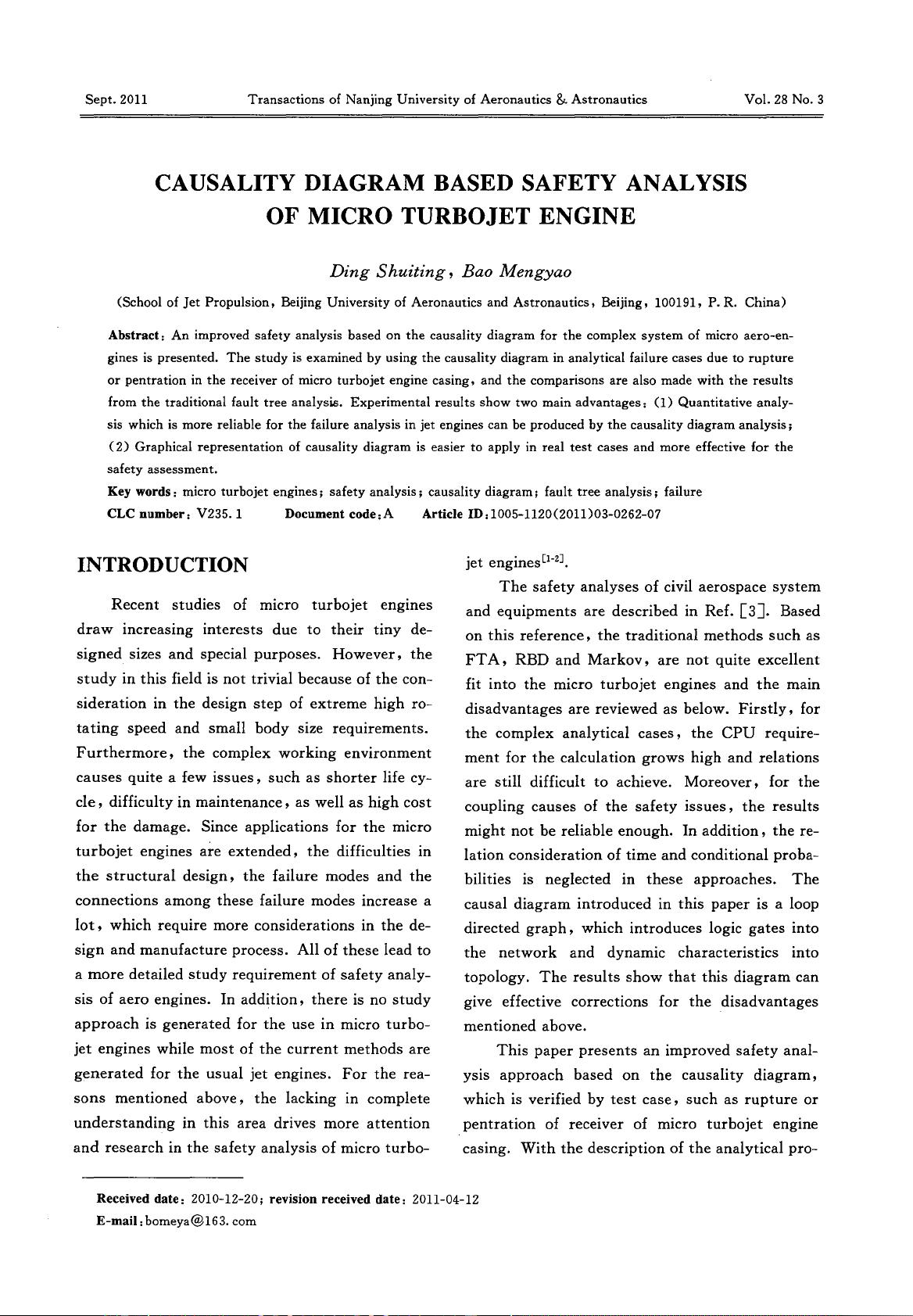
Sept.2011 Transactions
of
Nanjing University
of
Aeronautics
&.
Astronautics Vol.
28
No.
3
CAUSALITY DIAGRAM BASED SAFETY ANALYSIS
OF
MICRO
TURBOJET
ENGINE
Di
ng
Shuiting
,
Bao
Mengyao
(School of Jet Propulsion,
Be
ijing University
of
Aeronautics and Astronautics,
Be
ijing ,
100191
,
P.
R.
China)
Abstract: An improved safety analysis based
on
the causality diagram for the complex system of micro aero-en-
gines
is
presented. The study
is
examined
by
using the causality diagram
in
analytical failure cases due to rupture
or pentration
in
the receiver of micro turbojet engine casing , and the comparisons are also made with the results
from the traditional fault tree analysis. Experimental results show two main advantages:
(1)
Quantitative analy-
sis which
is
more reliable for the failure analysis
in
jet engines can
be
produced
by
the causality diagram analysis;
(2)
Graphical representation
of
causality diagram
is
easier to apply
in
real test cases and more effective for the
safety assessment.
Key
words: micro turbojet engines; safety analysis; causality diagram; fault tree analysis; failure
CLC number: V235. 1 Document code:A Article ID:1005-1120(201
1)
03-0262-07
INTRODUCTION
Recent
studies
of
micro
turbojet
engines
draw
increasing
interests
due
to
their
tiny
de-
signed
sizes
and
special
purposes.
However
,
the
study
in
this
field is
not
trivial
because
of
the
con-
sideration
in
the
design
step
of
extreme
high
ro-
tating
speed
and
small
body
size
requirements.
Furthermore
,
the
complex
working
environment
causes
quite
a
few
issues
,
such
as
shorter
life
cy-
cle
,
difficulty
in
maintenance
,
as
well
as
high
cost
for
the
damage.
Since
applications
for
the
micro
turbojet
engines
are
extended
,
the
difficulties
in
the
structural
design
,
the
failure
modes
and
the
connections
among
these
failure
modes
increase
a
lot
,
which
require
more
considerations
in
the
de-
sign
and
manufacture
process.
All
of
these
lead
to
a
more
detailed
study
requirement
of
safety
analy-
sis
of
aero
engines.
In
addition
,
there
is
no
study
approach
is
generated
for
the
use
in
micro
turbo-
jet
engines
while
most
of
the
current
methods
are
generated
for
the
usual
jet
engines.
For
the
rea-
sons
mentioned
above
,
the
lacking
in
complete
understanding
in
this
area
drives
more
attention
and
research
in
the
safety
analysis
of
micro
turbo-
jet
engines
口
-2J
The
safety
analyses
of
civil
aerospace
system
and
equipments
are
described
in
Ref.
[3J.
Based
on
this
reference
,
the
traditional
methods
such
as
FT
A ,
RBD
and
Markov
,
are
not
quite
excellent
fit
into
the
micro
turbojet
engines
and
the
main
disadvantages
are
reviewed
as
below.
Firstly
,
for
the
complex
analytical
cases
,
the
CPU
require-
ment
for
the
calculation
grows
high
and
relations
are
still
difficult
to
achieve.
Moreover
,
for
the
coupling
causes
of
the
safety
issues
,
the
results
might
not
be
reliable
enough.
In
addition
,
the
re-
lation
consideration
of
time
and
conditional
proba-
bilities
is
neglected
in
these
approaches.
The
causal
diagram
introduced
in
this
paper
is
a
loop
directed
graph
,
which
introduces
logic
gates
into
the
network
and
dynamic
characteristics
into
topology.
The
results
show
that
this
diagram
can
give
effective
corrections
for
the
disadvantages
mentioned
above.
This
paper presents
an
improved
safety
anal-
ysis
approach
based
on
the
causality
diagram
,
which
is
verified
by
test
case
,
such
as
rupture
or
pentration
of
receiver
of
micro
turbojet
engine
casing.
With
the
description
of
the
analytical
pro-
Received date: 2010-12-20; revision received date: 2011-04-12
E-mail: bomeya@163.com
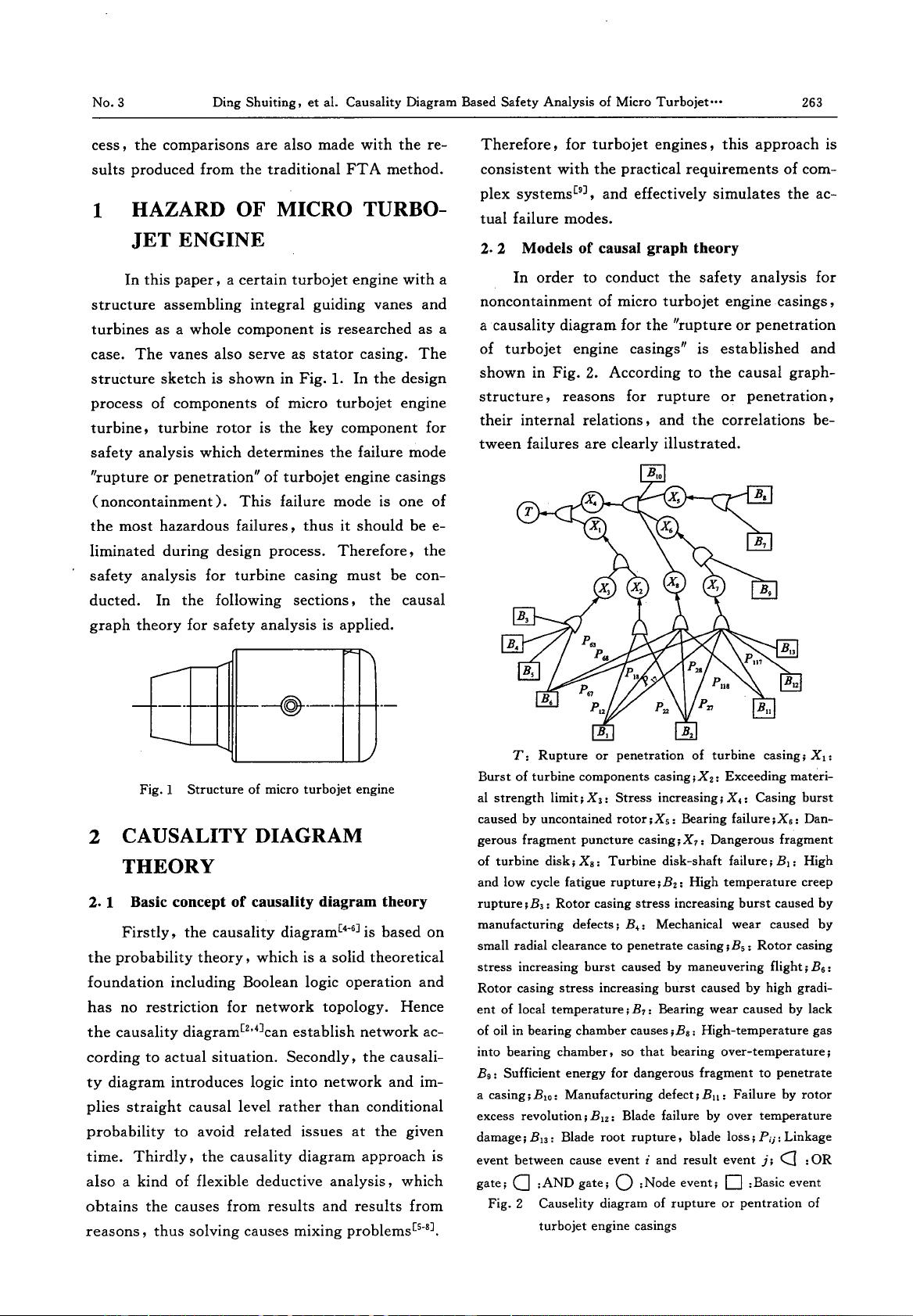
No.3
Ding Shuiting
, et al. Causality Diagram
Ba
sed Safety Analysis of Micro Turbojet...
263
cess
,
the
comparisons
are
also
made
with
the
re-
sults
produced
from
the
traditional
FT
A
method.
1
HAZARD
OF
MICRO
TURBO-
JET
ENGINE
In
this
paper
, a
certain
turbojet
engine
with
a
structure
assembling
integral
guiding
vanes
and
turbines
as
a
whole
component
is
researched
as
a
case.
The
vanes
also
serve
as
stator
casing.
The
structure
sketch
is
shown
in
Fig.
1.
In
the
design
process
of
components
of
micro
turbojet
engine
turbine
,
turbine
rotor
is
the
key
component
for
safety
analysis
which
determines
the
failure
mode
"rupture
or
penetration"
of
turbojet
engine
casings
(noncontainment).
This
failure
mode
is
one
of
the
most
hazardous
failures
,
thus
it
should
be
e-
liminated
during
design
process.
Therefore
,
the
safety
analysis
for
turbine
casing
must
be
con-
ducted.
In
the
following
sections
,
the
causal
graph
theory
for
safety
analysis
is
applied.
一⑨一
Fig. 1 Structure of micro turbojet engine
2 CAUSALITY
DIAGRAM
THEORY
2.
1
Basic
concept
of
causality
diagram
theory
Firstly
,
the
causality
diagram[
4-6]
is
based
on
the
probability
theory
,
which
is a
solid
theoretical
foundation
induding
Boolean
logic
operation
and
has
no
restriction
for
network
topology.
Hence
the
causality
diagram[2,4]can
establish
network
ac-
cording
to
actual
situation.
Secondly
,
the
causali-
ty
diagram
introduces
logic
into
network
and
im-
plies
straight
causal
level
rather
than
conditional
probability
to
avoid
related
issues
at
the
given
time.
Thirdly
,
the
causality
diagram
approach
is
also
a
kind
of
flexible
deductive
analysis
,
which
obtains
the
causes
from
results
and
results
from
reasons
,
thus
solving
causes
mixing
problems[5-8].
Therefore
,
for
turbojet
engines
,
this
approach
is
consistent
with
the
practical
requirements
of
com-
plex
systems[9],
and
effectively
simulates
the
ac-
tual
failure
modes.
2. 2
Models
of
causal
graph
theory
In
order
to
conduct
the
safety
analysis
for
noncontainment
of
micro
turbojet
engine
casings
,
a
causality
diagram
for
the
"rupture
or
penetration
of
turbojet
engine
casings"
is
established
and
shown
in
Fig.
2.
According
to
the
causal
graph-
structure
,
reasons
for
rupture
or
penetration
,
their
internal
relations
,
and
the
correlations
be-
tween
failures
are
clearly
illustrated.
T:
Rupture or penetration of turbine casing; X 1 :
Burst of turbine components casing;X
2
: Exceeding materi-
al
strength limit; X
3:
Stress increasing; X‘ Casing burst
caused
by
uncontained rotor
;X
s
:
Be
aring failure
;X
s: Dan-
gerous fragment puncture
casing;X
n
Dangerous fragment
of turbine disk; X
a
:
Turbine disk-shaft failure; B
1
:
High
and
low
cycle
fatigue rupture; B
2
:
High temperature creep
rupture
;B
3
:
Rotor casing stress increasing burst caused
by
manufacturing defects;
B.:
Mechanical wear caused
by
small radial clearance to penetrate casing;
Bs:
Rotor casing
stress increasing burst caused by maneuvering flight;
B
6
:
Rotor casing stress increasing burst caused by high gradi-
ent of local temperature;
B
7
:
Be
aring wear caused
by
lack
of
oil
in
bearing chamber causes;
Ba:
High-temperature gas
into bearing chamber
,
so
that bearing over-temperature;
B
g
:
Sufficient energy for dangerous fragment to penetrate
a casing;
B
lO
:
Manufacturing defect; B
ll
: Failure
by
rotor
excess revolution;
B
12
:
Blade failure
by
over temperature
damage;
B
13
:
Blade root rupture , blade loss; P
ij
:
Li
nkage
event between cause event
i
and
result event
j;
cl : OR
gate;
0 :AND gate; 0
:Node
何
nt;
口:
Basic
event
Fig.
2 Causelity diagram
of
rupture
or
pentration
of
turbojet engine casings
剩余6页未读,继续阅读
资源评论
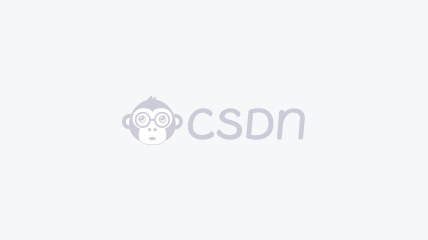

weixin_38742951
- 粉丝: 16
- 资源: 938
上传资源 快速赚钱
我的内容管理 展开
我的资源 快来上传第一个资源
我的收益
登录查看自己的收益我的积分 登录查看自己的积分
我的C币 登录后查看C币余额
我的收藏
我的下载
下载帮助

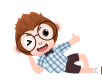
最新资源
- 安卓期末大作业-android垃圾分类app项目源码(高分项目).zip
- 基于go语言和vue3的简易图书管理系统.zip
- XYZ7-Matlab Code.zip
- 基于go语言与websocket实现的简易聊天室.zip
- 基于Go语言Gin框架的订单管理系统,正在建设中,本身为简单Demo,有助于掌握Go语言语法以及Gin开发框架简单使用,喜欢就点个Star吧!.zip
- 基于go-cqhttp的易语言SDK.zip
- 18717844379-2402241500.awb
- 基于Eytion的语言,在沿着用了Eytion的部分内容的基础上,做出了结构,制定得更加简洁,易懂.zip
- 基于C语言的简单在线词典.zip
- 基于C语言Socket编程的简易公告发布程序.zip
资源上传下载、课程学习等过程中有任何疑问或建议,欢迎提出宝贵意见哦~我们会及时处理!
点击此处反馈


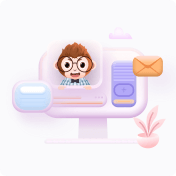
安全验证
文档复制为VIP权益,开通VIP直接复制
