没有合适的资源?快使用搜索试试~ 我知道了~
Influence of the porosity of C/C on the characterization of C/C-...
0 下载量 157 浏览量
2020-01-08
17:00:27
上传
评论
收藏 813KB PDF 举报
温馨提示
C/C气孔率对反应熔渗法制备的C/C-SiC复合材料性能的影响,王继平,金志浩,采用反应熔渗法将四种不同密度的C/C多孔体(气孔率为12.4%~45.7%)制备为C/C-SiC复合材料。通过阿基米德法,XRD,SEM和三点弯曲强度的分析
资源推荐
资源详情
资源评论
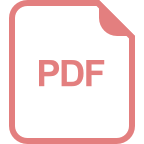
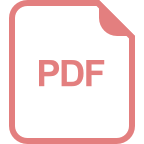
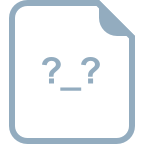
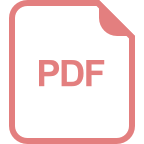
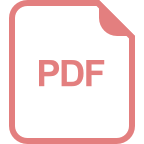
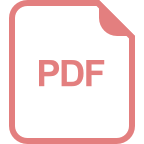
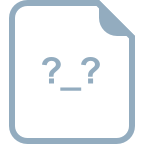
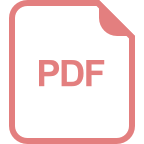
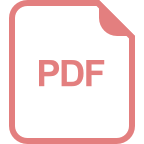
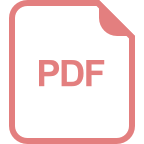
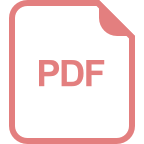
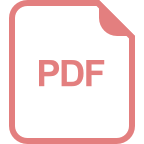
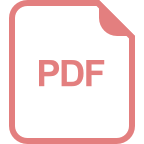
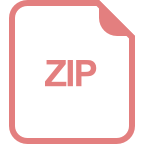
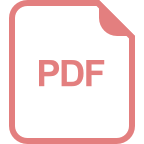
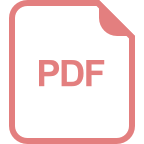
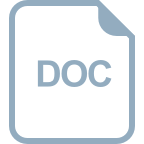
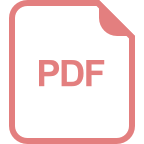
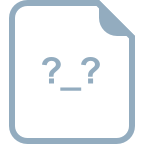
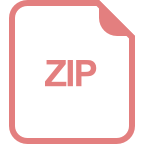
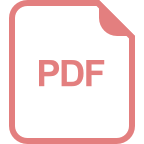
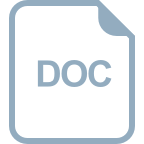
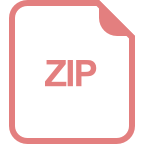
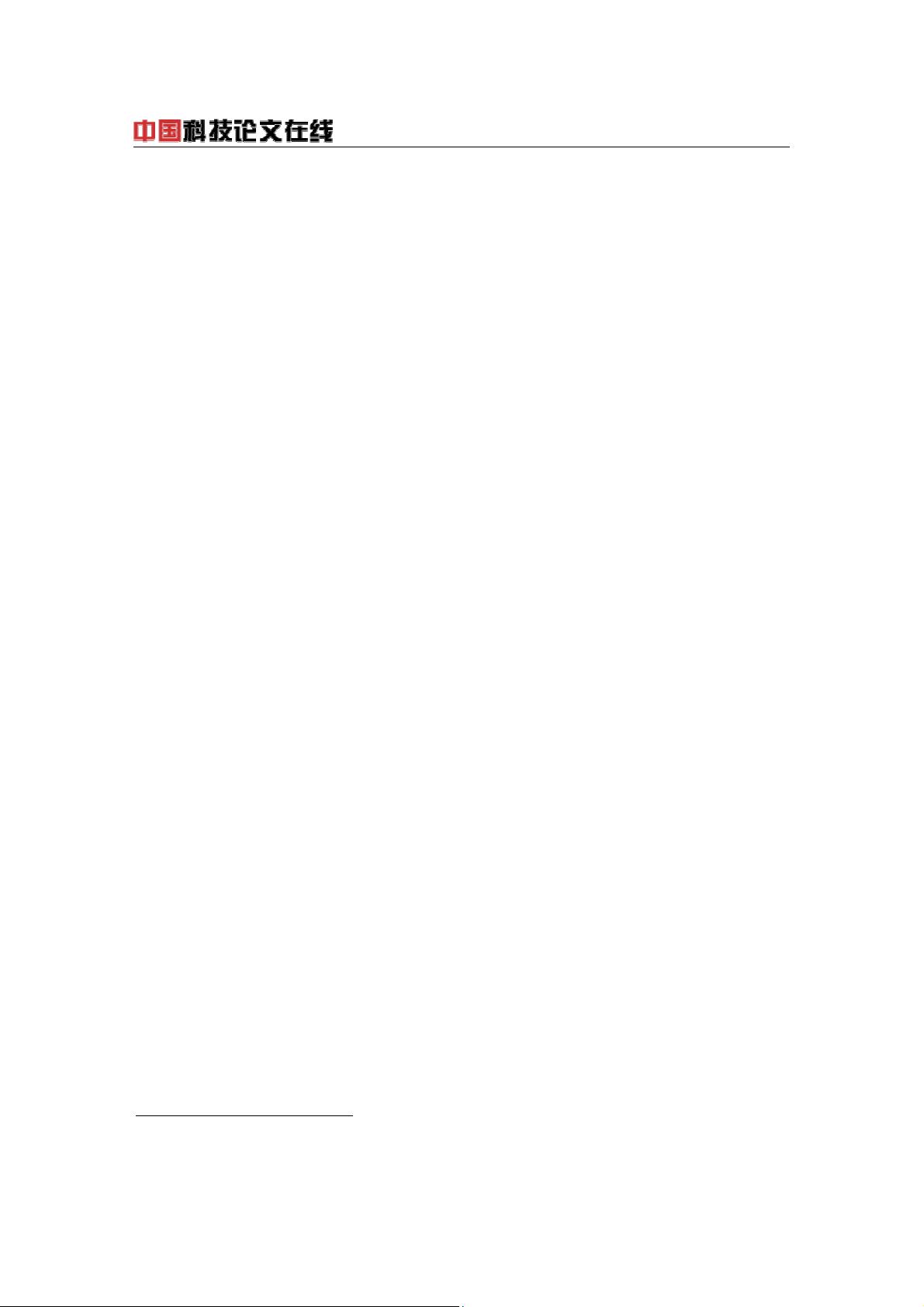
http://www.paper.edu.cn
-1-
Influence of the porosity of C/C on the
characterization of C/C-SiC composite
prepared by reactive melt infiltration
method
1
Jiping Wang
*
State Key Laboratory for Mechanical Behavior of Materials
Xi'an Jiaotong University
Xi'an 710049, China, 710049
jipingwang@gmail.com
Zhihao Jin, Min Lin, Yonghui Zhang
State Key Laboratory for Mechanical Behavior of Materials
Xi'an Jiaotong University
Xi'an 710049, China, 710049
Abstract
C/C performs with four different open porosities in the range of 12.4%~45.7% were
reactive-melt-infiltrated (RMI) with silicon to rapidly fabricate C/C-SiC composites.
The influence of the C/C porosity on the Si infiltration during the processing and on
the microstructure and mechanical properties of the resulting C/C-SiC composites
were investigated by means of density measurement, XRD, SEM, and three-point
bending test, respectively. The results show that the higher porosity of C/C brought
more silicon infiltration during RMI processing. The porosity also played a key role to
dominate the content of β-SiC, residual Si and C phases, as well as the porosity of the
resulting C/C-SiC composites. The flexural strength and the fracture behavior of the
composites were strong influenced by the matrix content and the interface between
different phases. C/C-SiC derived from C/C with 24.8% porosity has the highest
flexural strength (325.1MPa) and shows a brittle fracture behavior.
Keywords: C/C-SiC; open porosity; reactive melt infiltration; mechanical property;
microstructure
1 Introduction
Carbon fiber reinforced pyrocarbon and silicon carbide composites (C/C-SiC) have many outstanding
properties, such as high strength at elevated temperature, low density, superior toughness and abrasive
properties
[1]
. They are widely used as high temperature structural components in aerospace area and
also as promising candidates for advanced brake and clutch systems
[2-5]
.
The methods for fabricating C/C-SiC composites from porous carbon/carbon composites (C/C)
include chemical vapor infiltration (CVI) technique
[6-8]
, liquid precursor infiltration and pyrolysis (PIP)
processing
[9-10]
, and reactive melt infiltration (RMI) method (or called as liquid silicon infiltration)
[11-12]
. For CVI processing, methyltrichlorosilane (CH
3
SiCl
3
) in gas phase was infiltrated and
1
Support by Research Fund for the Doctoral Program of Chinese Higher Education (No. 20070698104)
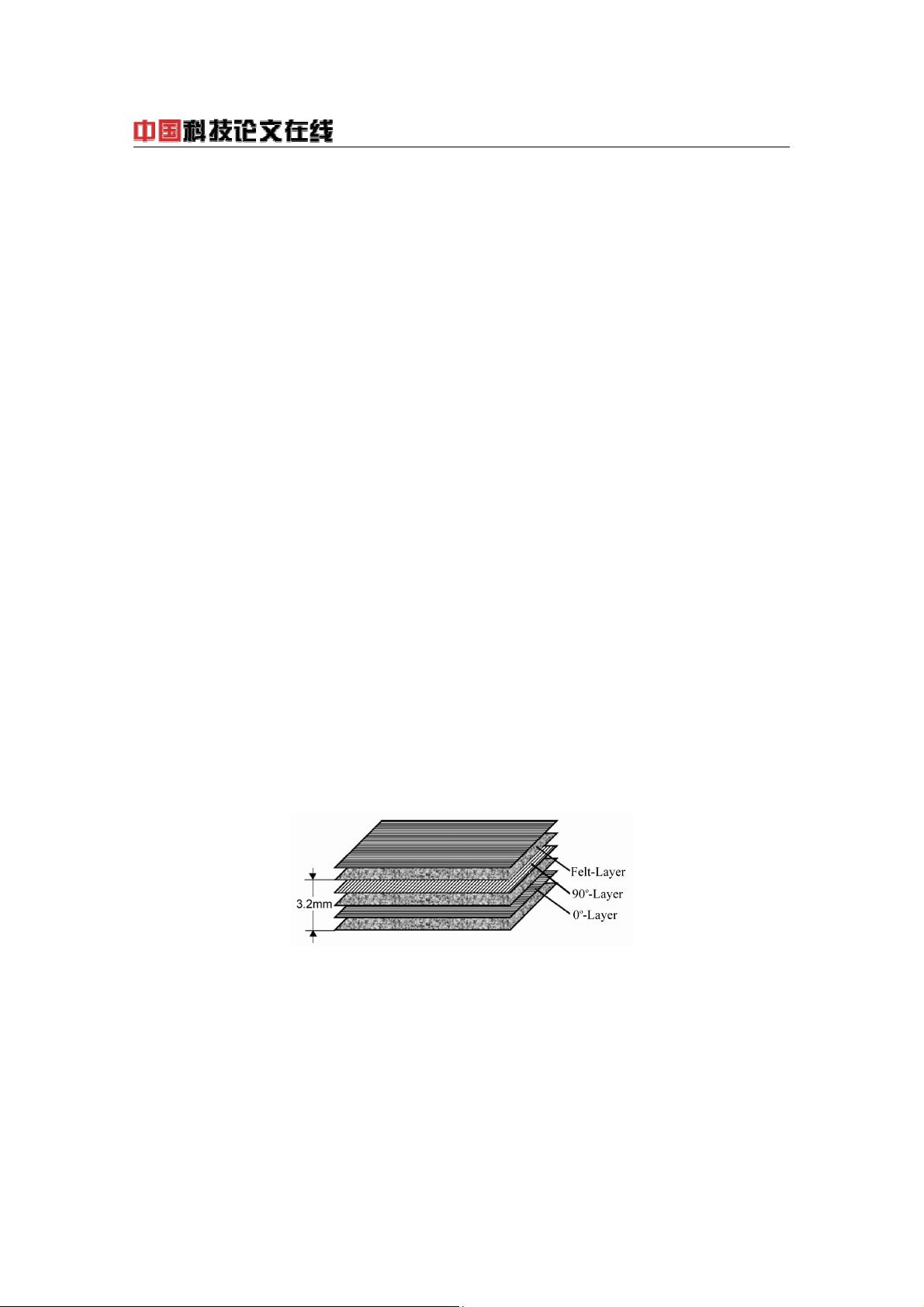
http://www.paper.edu.cn
-2-
decomposed at high temperature (1000~1200
o
C) to form SiC phase in the pores of C/C. However, CVI
processing need a long period to obtain densified C/C-SiC composites. PIP route uses liquid precursors
as SiC sources to fabricate C/C-SiC composites. Common precursors are such high molecular weight
polymers as polycarbosilane (PCS), polymethlsilane (PMS) and hexamethyldisilazane (HMDS).
However, most of them have high price because they are not commercial production. Moreover, in
order to achieve high densified composites more than 5 cycles were required. RMI process is the most
attractive method among the three feasible processes considering the processing time and the cost. This
method impregnates porous C/C by molten silicon; C and Si reacts to form SiC at high temperature
(above 1410
o
C). It is a near-net-shape process and only need one infiltration cycle to achieve full
densified production.
Therefore RMI has been extensively investigated since it was firstly developed near 30 years ago
[13]
. The basic investigations were focused on the kinetics of liquid Si infiltration into porous carbon,
and the mechanism of the reaction between solid carbon and liquid silicon
[14-17]
. However, the physical,
mechanical properties and frictional behavior of the resulting C/C-SiC are not only influenced by the Si
infiltration and Si/C reaction, but also dominated by the fiber-matrix interface and the contents and
distribution of different phase in the composites
[18-19]
. Various microstructures and phase compositions
of C/C-SiC composites can be achieved by modifying the fiber preform architecture and the content of
the pyrocarbon in C/C. When fiber preform was chosen and certain pyrocarbon was formed, the
porosity and the pore size distribution in C/C were fixed. Nevertheless, how the porosity of C/C
preform influences the microstructures and mechanical propertied of as-prepared C/C-SiC composites
is not yet clearly investigated.
In the present work, C/C composites were firstly made by CVI method, which derived from same
fiber architecture and has different porosity, then C/C-SiC composites were prepared by RMI
processing from the C/C The influence of the porosity of C/C on the microstructures and mechanical
properties of the C/C-SiC composite was investigated. Based on the present work, RMI processing will
be further understood and we can obtain an optimized porosity of C/C for preparing C/C-SiC with
excellent properties.
2 Experimental procedures
2.1 Material preparation
A quasi three-dimension (3D) carbon fiber was chosen as preforms; the fiber type is T300 (density 1.76
g/cm
3
) and its architecture was shown in Fig. 1. The bulk density of the preform is 0.51g/cm
3
and the
fiber volume ratio is 28.5%. C/C composites with four different porosities were prepared by chemical
vapor infiltration (CVI) method using ethene as precursor. Then the C/C was cut in size of 60 × 8 × 6
mm
3
and consequently RMI with Si under vacuum atmosphere to form C/C-SiC composites. Averaged
Fig. 1. Schematics of the carbon fiber preform used as reinforcement.
size of commercial silicon particles (size 1~3 mm) were used. The reaction temperature and reaction
time of RMI processing were ~1600
o
C and 30 minutes, respectively.
Third level headings are lower case (except for first word and proper nouns), flush left, bold and in
point size 10. One line space before the third level heading and ½ line space after the third level
heading.
剩余7页未读,继续阅读
资源评论
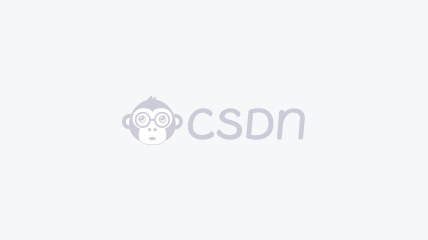

weixin_38727825
- 粉丝: 3
- 资源: 900
上传资源 快速赚钱
我的内容管理 展开
我的资源 快来上传第一个资源
我的收益
登录查看自己的收益我的积分 登录查看自己的积分
我的C币 登录后查看C币余额
我的收藏
我的下载
下载帮助

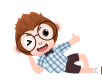
最新资源
- springboot246老年一站式服务平台.zip
- springboot244基于SpringBoot和VUE技术的智慧生活商城系统设计与实现.zip
- 关键词:冷热电联供;CHP机组;热泵;冰储冷空调;需求响应 参考文献:《基于综合需求响应和奖惩阶梯型碳交易的综合能源系统优化调度》《计及需求响应和阶梯型碳交易机制的区域综合能源系统优化运行》碳交易机
- springboot248校园资产管理.zip
- springboot247人事管理系统.zip
- springboot249在线互动学习网站设计.zip
- 蒙特卡洛模拟电动汽车有序充放电(matlab),适合优化调度,微电网,综合能源、储能、新能源方向的基础入门学习
- springboot251基于springboot-vue的毕业论文管理系统.zip
- springboot252基于Springboot和vue的餐饮管理系统的设计与实现.zip
- springboot250智慧校园之家长子系统.zip
- springboot254小区团购管理.zip
- springboot253社区养老服务系统.zip
- springboot255基于spring boot的疫情信息管理系统.zip
- 半桥LLC谐振变器,Matlab simulink仿真,电压闭环PI pi控制,输出电压12V,实现软开关运行
- springboot259交通管理在线服务系统的开发.zip
- springboot256基于springboot+vue的游戏交易系统.zip
资源上传下载、课程学习等过程中有任何疑问或建议,欢迎提出宝贵意见哦~我们会及时处理!
点击此处反馈


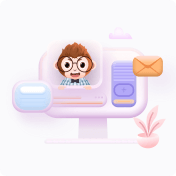
安全验证
文档复制为VIP权益,开通VIP直接复制
