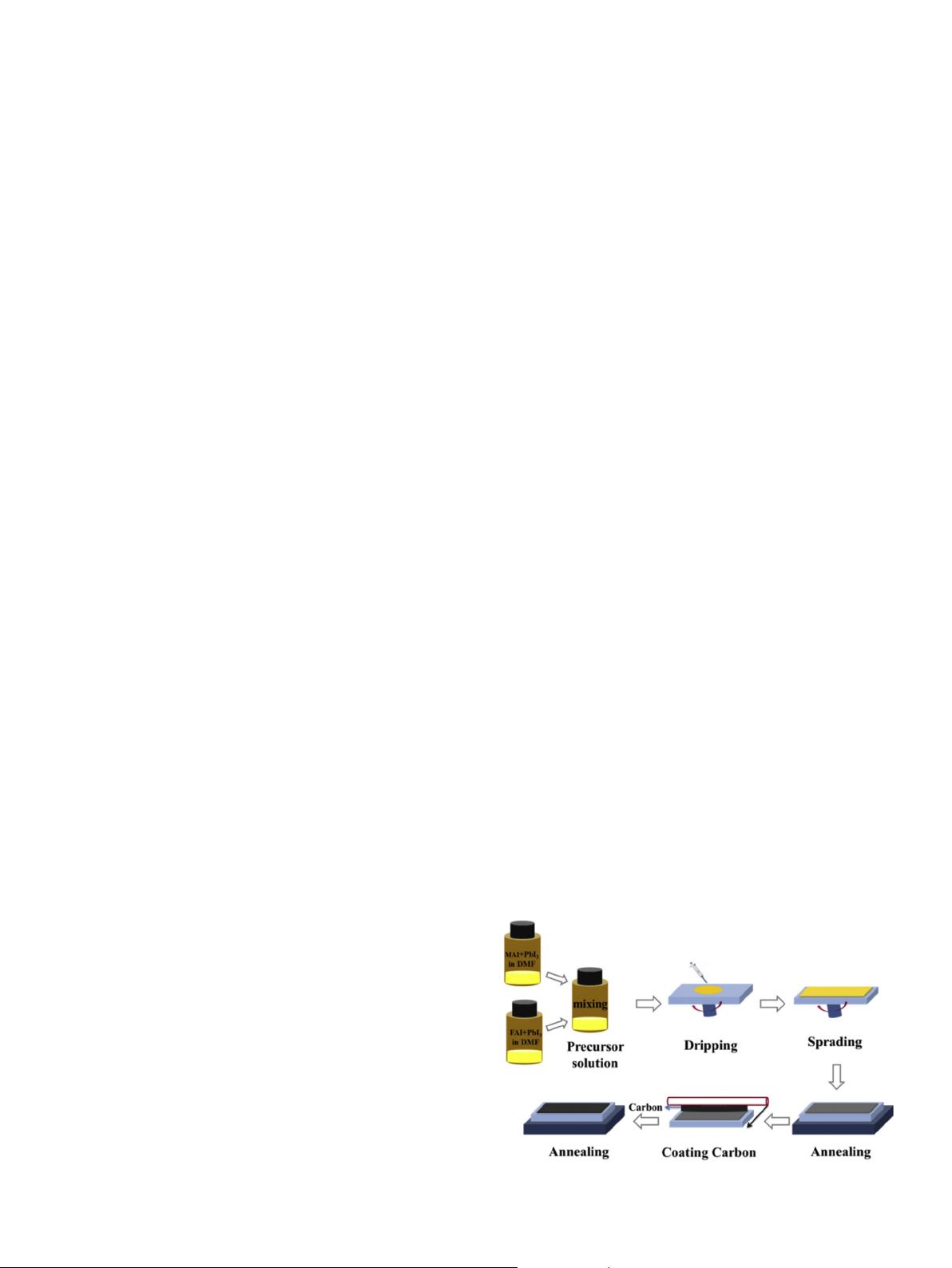
light harvesting capacity on a stable structure of mixed organic
cation is more important. The specific mixing ratio and calcination
temperature are the focus of research.
The conventional hole-transporting materials (HTMs) based on
the 2,2
0
,7,7
0
-tetrakis (N,N-di-p-methoxy phenylamine)- 9,9-spi-
robifluorene (spiro-MeOTAD) [20e22] and poly(triarlyamine)
(PTAA) [22] perform advantages of extracting photogenerated
charge, which achieved high efficiency in PSCs. However, there still
are limitation including high-cost and hydrophilism for potential
photovoltaic application. The noble metal counter electrodes (Au or
Ag) of highly efficient PSCs are fabricated by thermal evaporation
under high vacuum condition [8,21 ,23]. Obviously, energy
consumptive and high production cost of noble metal counter
electrodes limit the scale of production. Besides, Au migrates
through the HTL into the perovskite material, which degrades the
device performance [24]. It is reported that the carbon with work
function (5.0 eV) has been applied in PSCs instead of Au (5.1 eV)
[25e28], especially the large area PSCs has high efficient of 10%
with stable large-area (10 10 cm
2
)[29]. In addition, the HTM-free
PSCs based on carbon electrode shows excellent stability [30e32].
The carbon will become an ideal candidate for applying in PSCs as
counter electrode due to its advantage such as low-cost, abundantly
available, and pollution-free.
Here, hole transporting materials and noble metal counter
electrodes were no employed in the large area PSCs. Instead, the
carbon counter electrode was formed by a simply blade coating
skill. The photovoltaic performance of mixed organic cation hole-
conductor-free PSCs based on carbon electrodes was investigated.
The electron transport behavior was further discussed by the
electrical impedance measurements. The results indicated that the
photo-electrical characteristics of our PSCs with mixed organic
cation perovskite (FA)
x
(MA)
1x
PbI
3
were improved with x from 0 to
0.3, the PSCs based on x ¼ 0.3 exhibited the highest the overall
conversion efficiency (
h
) and a long-term stability, though mixed
perovskite material was annealed at low temperature 100
C.
2. Experimental section
2.1. Materials
PbI
2
was purchased from Xian Polymer Light Technology Corp.
TiCl
4
and N,N-dimethylformamide (DMF) were purchased from
Macklin, others reagents were bought from Luoyang chemical re-
agent company. NH]CHNH
3
I (FAI) and CH
3
NH
3
I (MAI) were syn-
thesized under certain conditions according to a published
literature [8,12]. Fluorine-doped tin oxide conductive substrates
(FTO, 7
U
/sq) were purchased from Shen Zhen Hua Nan Xiang
Cheng Factory.
2.2. Device fabrication
The whole experimental processes were finished under air at-
mosphere with high humidity condition around 50%. The devices
were prepared on the clean conductive FTO substrates, which were
cleaned with detergent diluted, deionized water, acetone and
ethanol, then dried in clean air. Blocking layer (BL-TiO
2
) was formed
through FTO substrates dipped into TiCl
4
aqueous solution of
0.08 mol/L and kept at 70
C for 40 min, subsequently washed the
substrates with deionized water and ethanol, which heated in air at
450
C for 0.5 h. The mesoporous layer TiO
2
(MP-TiO
2
) was pre-
pared by spin coating the diluted TiO
2
paste in ethanol (paste:
ethanol ¼ 1:3 wt ratio) at 3800 r.p.m for 30 s, the substrates were
dried at 200
C for 10 min. Then the insulating mesoporous layer
ZrO
2
(MP-ZrO
2
) was formed by spin-coating the diluted ZrO
2
paste
in ethanol (paste: ethanol ¼ 1:3 wt ratio) at 420 0 r.p.m for 30 s, the
devices were gradually sintered at 500
C for 0.5 h. The TiO
2
and
ZrO
2
paste were synthesized by a modified method of our labora-
tory [33], the size of TiO
2
and ZrO
2
nano grain were about 20 nm
and 50 nm respectively. The fabrication process of the pervoskite
film and coating carbon in PSCs were showed in Fig. 1 First, the
precursor solutions of MAPbI
3
, FAPbI
3
were prepared by dissolved
of the MAI and powder PbI
2
, FAI and powder PbI
2
in DMF respec-
tively (The mass fraction was 40%), then stirred at 50
C for 2 h.
Second, the certain amount precursor solutions of MAPbI
3
and
FAPbI
3
was mixed to formed the (FA)
x
(MA)
1-x
PbI
3
precursor solu-
tion. The mixed pre-solution was deposited on MP-ZrO
2
by spin-
coating at a low speed of 1800 r.p.m for 3 s and followed a high
speed of 3600 for 30 s, the films were heated at 100
C for 40 min.
For complete the devices, carbon paste was blade coating on the top
of perovskite films aided by glass rod as the counter electrode, the
substrates were heated at 100
C for 15 min. The active area of the
as-fabricated PSCs was 0.96 cm
2
.
2.3. Photovoltaic measurements
The morphology of as-prepared (MA)
x
(FA)
1-x
PbI
3
film was
observed by scanning electron microscope (SEM, Zeiss Supa 50VP,
Germany). The phase structure and purity were recorded by X-ray
diffraction (XRD) patterns of via a Rigaku SmartLab diffractometer
with Cu K
a
target. Optical absorbance characteristics were
measured by the TU-1810PCS UVevis spectrophotometer (Beijing
Purkinje General Ins. Co. Ltd., CHINA) with wavelength range
300e900 nm. As-prepared PSCs with area of 0.96 cm
2
were tested
by a solar simulator BOS-X-1000G of irradiance 1000 W m
2
(Changchun Bosheng, Com. Inc., CHINA, the equivalent of one sun at
AM1.5G, intensity adjust by using PMA2100/PMA2144 Pyranometer
(Solar Light CO., INC., USA)) at the surface. The current-voltage
characteristics were recorded by a Keithley model 2602A digital
source meter (Keithley, USA) with external potential bias to the
PSCs. Electrochemical impedance spectrum of PSCs was measured
through electrochemical workstation (Parstat 2273, USA,
Princeton).
3. Results and discussion
As-prepared PSCs was made of FTO glass, compact blocking
layers, mesoporous TiO
2
layer, mesoporous ZrO
2
insulating layer,
pervoskite and Carbon. The schematic structure was glass/FTO/BL-
TiO
2
/MP-TiO
2
/MP-ZrO
2
/(FA)
x
(MA)
1x
PbI
3
/C as shown in Fig. 2(a)
and the corresponding energy level diagram of TiO
2
, ZrO
2
, per-
voskite, and Carbon was showed in Fig. 2(b). The perovskite layer
Fig. 1. Fabrication process of the pervoskite film and coating carbon in PSCs.
H. Liu et al. / Electrochimica Acta 266 (2018) 78e85 79