没有合适的资源?快使用搜索试试~ 我知道了~
资源推荐
资源详情
资源评论














Product-level Reliability of GaN Devices
Sandeep R. Bahl, Daniel Ruiz and Dong Seup Lee*
Texas Instruments
2900 Semiconductor Dr. Santa Clara, CA 95052
*13121 TI Blvd, Dallas, TX 75243
Abstract—To enable the widespread adoption of GaN products,
the industry needs to be convinced of product-level reliability.
The difficulty with product-level reliability lies with the diverse
range of products and use conditions, a limited ability for
system-level acceleration, and the complication from non-GaN
system failures. For power management applications, however,
it is possible to identify fundamental switching transitions. This
allows the device to be qualified in an application-relevant
manner. In this paper, we explain how hard-switching can form
a fundamental switching transition for power management
products. We further show that the familiar double-pulse tester
is a good hard-switching qualification test vehicle. The
methodology is explained in the context of the existing
qualification framework for silicon transistors.
Index Terms—Gallium nitride, life testing, power conversion,
power transistors, semiconductor device reliability
I. INTRODUCTION
The industry now takes the reliability of silicon transistors
for granted, as evidenced by their widespread use in products.
This is a result, not only of longstanding experience, but also
of the development of credible reliability and qualification
methodology. Technology is qualified by running
standardized stress tests [1]-[3], and by validating lifetime
requirements [4]. This methodology originated from detailed
work on the understanding of failure modes, their acceleration
and modeling, and a statistical framework to assure a
minimum level of quality.
The stress tests, however, were developed more than
twenty years ago, with the Joint Electron Device Engineering
Council (JEDEC) JESD47 document released in 1995 and the
Automotive Electronics Council (AEC) founded in 1994. The
qualification procedure has remained essentially unchanged
over the years, whereas technology and its uses have changed.
For example, power conversion circuitry using hard-switched
transistors is now much more widespread. There is also
tremendous interest in emerging materials like GaN and SiC
for power management applications.
Transistors from emerging materials are being judged as
“passing qual” when run through the standardized stress tests
described in [1]-[3]. While the standard silicon-based
qualification recipe is a worthy manufacturing, quality and
reliability milestone, it is not clear what it means for emerging
transistors in terms of device lifetime, failure rates and
application-relevance. This is because the failure modes,
activation energies, and acceleration factors are likely to be
different than those used for Si. In addition, the reliability test
conditions may not be representative of the product use-case
so may not accelerate valid failure mechanisms.
For successful technology adoption, it is important to
develop credible reliability and qualification methodology. A
successful methodology allows the industry to gain confidence
that parts will last for the desired lifetime in the end-use
application without many customer returns. It also allows
users to easily benchmark components and suppliers.
II. WHAT DOES QUALIFICATION MEAN?
Traditional qualification testing [1]-[3] or “qual” involves
many tests, which may be classified into three categories:
device, package, and electrostatic discharge (ESD). In this
paper, we focus on device-relevant testing. In order for the
industry to develop GaN-specific methodology, it is important
to understand the fundamentals and assumptions behind
traditional qualification. It is also important to know what
“passing qual” means. The knowledge may be summarized in
the form of the three questions below:
A. How long is the device qualified for?
This is typically perceived to be 10 years
*
. The calculation
arises by running a 1000h test at a junction temperature of
125°C and extrapolating to a use-temperature of 55°C with an
activation energy of 0.7 eV. Additionally, discrete FETs are
commonly qualified at 80% of the minimum breakdown
voltage, e.g. a 600V FET is qualified at 480V. The 80% value
is common practice and not specified by present standards
†
.
The ten-year assumption falls apart for power FETs, even
those made from Si. Several scenarios are calculated in [6].
The typical use-temperature of power FETs is about 100-
110°C. If qualification is run at 150°C, then the non-
accelerated time for use at 105°C is only 1.1 yrs, far short of a
ten year lifetime. Further, thermal acceleration for silicon
assumes an activation energy of 0.7 eV, whereas activation
energies for GaN are likely to be different. Recent power GaN
literature shows a wide range [7]-[13], from 0.1 eV to 1.84
eV. Voltage acceleration is also used [11],[14]. The variation
is expected, due to different failure modes and architectures.
Indeed, power GaN transistors comprise both depletion and
enhancement mode (d- and e-mode) FETs. Further, d-mode
FETs are Schottky [9] or Insulated-gate [12] and are either
cascoded with a low-voltage Si FET [12] or an IC [15] for
*
The traditional calculation results in nine years [1].
†
The current documentation [3] specifies qualification at the maximum rated
DC reverse voltage. An 80% criteria exists in historical documentation [5]
© 2016 IEEE. Personal use of this material is permitted. Permission from IEEE must be obtained for all other uses, in any current or future media, including
reprinting/republishing this material for advertising or promotional purposes, creating new collective works, for resale or redistribution to servers or lists, or reuse of any
copyrighted component of this work in other works.
Presented at the IEEE International Reliability Physics Symposium (IRPS), Apr. 2016. (Invited paper)
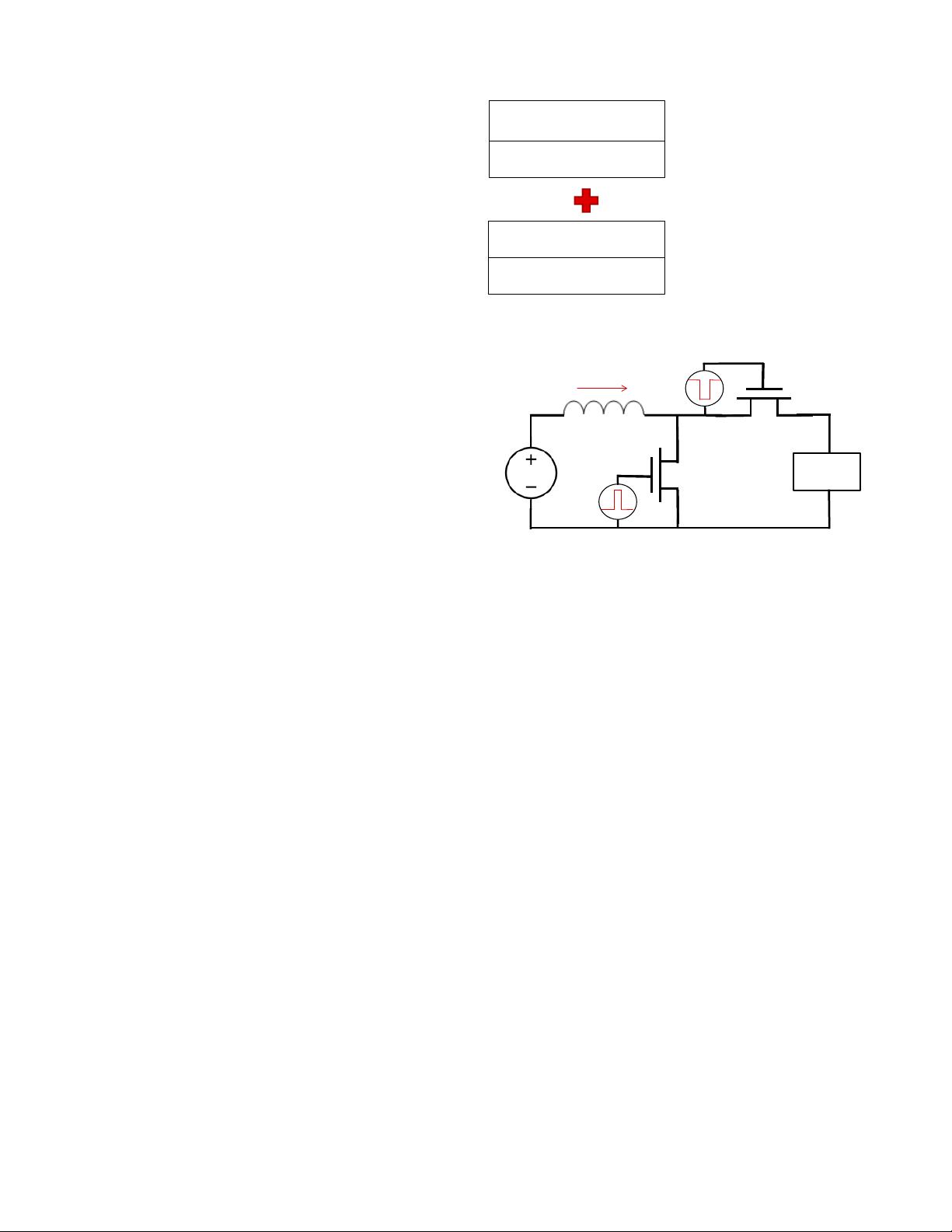
failsafe reasons. E-mode architectures are either junction-gate
[11],[16],[17] or recessed insulated-gate [18].
B. Is the stress-testing representative of actual usage?
Traditional qualification testing does not consider the
switching conditions of power management. High-
Temperature Reverse Bias (HTRB) and High Temperature
Gate Bias (HTGB) are static tests. High Temperature
Operating Life (HTOL) is configured to bias operating nodes
and is typically applied on logic and memory devices [19].
Confidence has been built in the qualification methodology for
Si devices over the years. This is because the long-standing
experience has resulted in a detailed understanding of failure
modes, the device design knowledge to avoid them, and the
development of proxy tests e.g. substrate current monitoring
for Hot-Carrier Injection (HCI) robustness [20]. For emerging
technologies, however, switching robustness needs to be
proven by running the device under actual-use conditions.
C. Will there be many field-failures?
Passing qualification with silicon assumptions means that the
lot-tolerant percent defective (LTPD) value is one [1] and
failure in time (FIT) rate is established to be less than about 50
(60% confidence level) [21]. The LTPD calculation arises
from the statistics of zero fails out of 231 (3 lots x 77) parts.
LTPD=1 means that one can state with 90 percent confidence
that less than one percent of the parts in a lot will fail when
run for the non-accelerated time. The FIT rate calculation
arises from the total number of non-accelerated device hours.
In practice, for mature processes, the pooling of multiple
qualification runs increases the total number of parts and
device hours, allowing lower FIT rate and LTPD projections.
In order to get accurate statistics, the acceleration factor needs
to be determined for GaN, and the testing needs to be
predictive of actual-use conditions. The acceleration factor is
also used in early failure testing (ELFR) [1],[22], which is
used to assess the infant mortality rate.
III. APPLICATION-RELEVANT QUALIFICATION
Both JEDEC and AEC standards are based on sound
fundamentals, but lag technology introduction. For example,
the discrete power metal-oxide semiconductor field-effect
transistor (MOSFET) was developed in the late 1970s [23],
but it was not until the early 1990s that JEDEC developed a
qualification standard. A standard is not needed to make
technology reliable. It is a deep understanding of the
technology; its failure modes; and knowledge of testing,
qualification and product operation.
The qualification standards [1]-[3] are stress-based,
consisting of documented, standardized procedures that
prescribe accelerated test conditions. New technology
qualification adds a knowledge-based approach, summarized
in Fig. 1. This builds upon the existing framework by adding
testing and lifetime modeling for GaN specific failure modes,
e.g. dynamic on-resistance (dRon) degradation. It also adds
new stress tests, to represent application-use.
GaN has shown great promise in many power conversion
topologies, e.g. buck and boost converters, bridgeless PFC
circuits, inverters, LLC converters etc. The question arises as
to how GaN would be qualified for all these end applications.
Although JEDEC specifies the need for dynamic testing, it
does not prescribe conditions, citing the ever-evolving
applications and material sets in our industry [24]. It is not
straightforward to assure product-level reliability in a broad
sense. In addition to application diversity, products contain
many non-GaN parts and the system is not typically designed
for accelerated testing, or for running in an oven at 150°C.
Running product reliability under accelerated conditions
would cause many non-GaN failures, making it difficult to
extract useful information. Another difficulty is the energy
requirement. In order to run many power converters, one
would need to dissipate tens of thousands of watts.
One approach to this problem is to identify an application
stress condition common to a class of devices. For example,
JESD226 [25] takes such an approach for power amplifier
modules (PAMs). The documentation states “This method is
intended to refine and focus the myriad of biasing options
down to a standard that can be applied industry-wide so that
users of PAMs can gain confidence that devices successfully
completing this test method will exhibit adequate reliability
for the anticipated use conditions”.
There is a large class of power management products that
place similar stresses on the power transistor. To illustrate,
consider the hard-switched boost converter schematic in Fig.
2. Teaching waveforms for both the high and low side FETs
are shown in Fig. 3, and the different operating regions are
described in Table 1. Table 1 also lists the bias stress on each
FET. As can be seen, the devices need to withstand the
following five types of stresses:
Established framework for Si
qualification and reliability
Extension for GaN – Failure
modes, lifetime extrapolation
Actual-use condition for
power management
JESD94B: Application-specific
qualification using knowledge-based
test methodology
JESD 226: An application relevant
example: RF bias life stress (RFBL)
for power amplifier modules
e.g. JESD47, AEC-Q100, Q101
Based upon methodology in e.g.
JESD22-A108D and JEP122G
Failure modes, lifetime
extrapolation
Figure 1: Qualification framework for GaN, built upon JEDEC
documentation. The silicon framework is extended for GaN-specific failure
modes and application-relevant testing is added.
Ga
GaN
FET1
Load
Ga
GaN
FET2
V
IN
I
L
Figure 2: Boost-converter schematic
剩余6页未读,继续阅读
资源评论
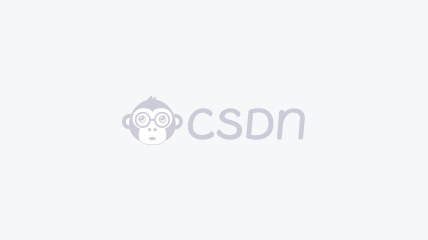

weixin_38689551
- 粉丝: 9
- 资源: 918
上传资源 快速赚钱
我的内容管理 展开
我的资源 快来上传第一个资源
我的收益
登录查看自己的收益我的积分 登录查看自己的积分
我的C币 登录后查看C币余额
我的收藏
我的下载
下载帮助

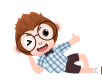
最新资源
- 微控制器固件包_STM32CubeG0_1741142084.zip
- 《ARM9嵌入式系统设计基础教程》第13章图形用户接口(GUI).ppt
- 《机械设计基础》课后习题答案
- C#调用Ni板卡进行实现采集任务(模拟量输入输出)示例2
- 《实验一 Java开发环境&语法基础》
- 2016级河南大学计算机与信息工程学院创新实践计划-消防机器人.zip
- Java课程设计-学生成绩管理系统-Swing+MySQL.zip
- 《AE影视后期特效制作实例教程》8-3++空中气流写字字帖.ppt
- Unwrap Pro是一个3ds Max插件,可以在产生低失真,无重叠,加权密度的UVs的同时展开网格,而不像3ds Max Peel命令,它产生具有高面积失真的重叠UV,UnwrapPro是非常快的
- 大二下SQL实验学生信息系统.zip
- macd指标算法 php语言编写 大智慧/同花顺 数据一致
- 2025修复版绿色全自适应php核心制作的邮编查询网整站源码带百万数据+定时触发更新
- 人工智能&深度学习:PyTorch 图像识别实战 - 卷积神经网络与模块应用资源(源码+数据集+说明资料)
- 《Java语言编程基础立体化实用教程》2-6+成绩增加和成绩修改窗体的实现.ppt
- ITECH艾德克斯交直流程控源使用手册
- 实时操作系统_FreeRTOS_内核组件_通用与特定_1741145229.zip
资源上传下载、课程学习等过程中有任何疑问或建议,欢迎提出宝贵意见哦~我们会及时处理!
点击此处反馈


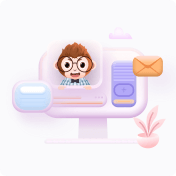
安全验证
文档复制为VIP权益,开通VIP直接复制
