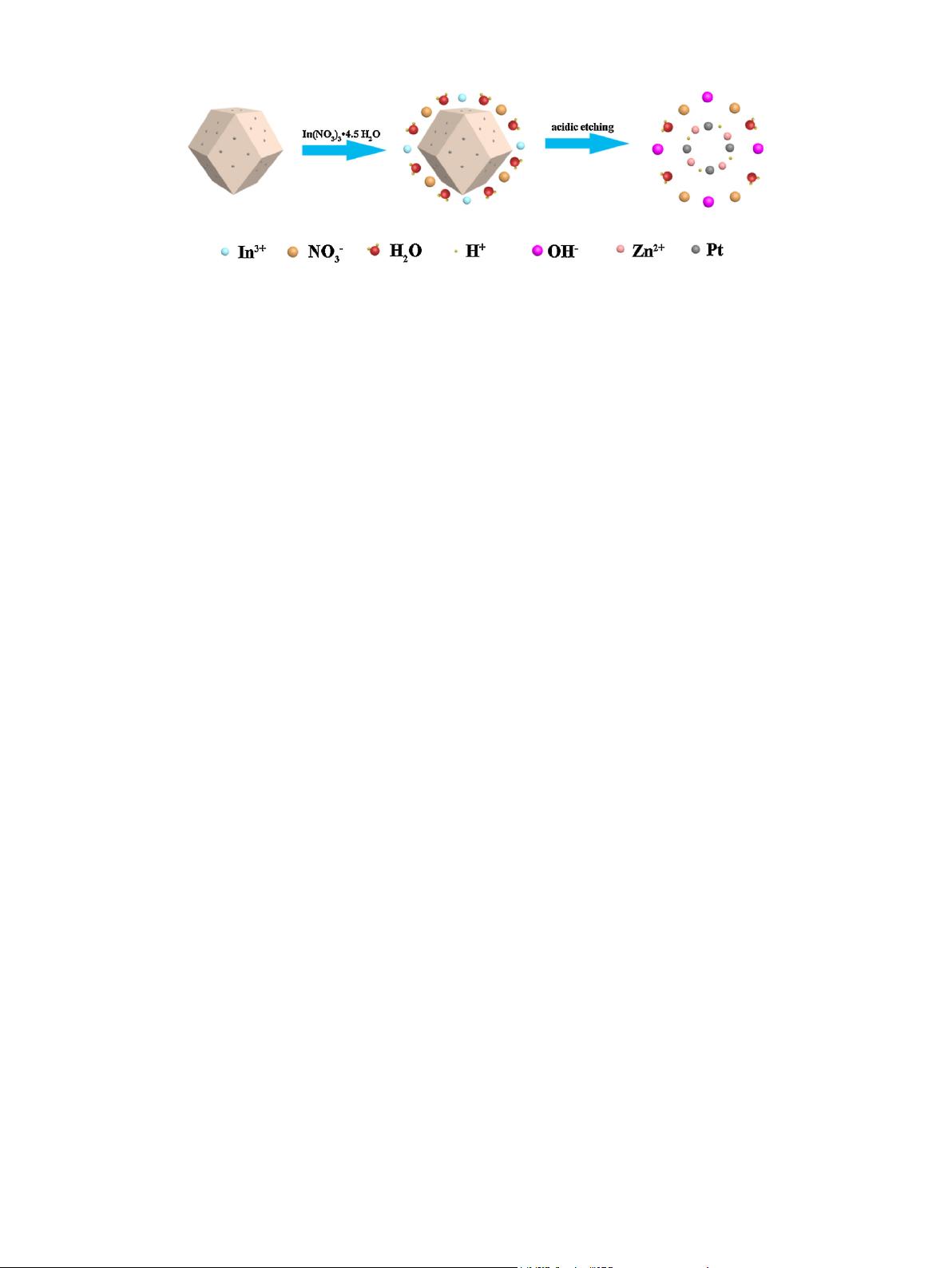
synthesis of noble metal catalyst (Pd) loaded ZIF-8 and then applied
onto metal-oxide semiconductors nanofibers by the means of electro-
spinning [24], which results in significant enhanced gas sensing per-
formance [25– 27].
Based on the reports above, a new type of sensitive materials of Pt-
ZnO-In
2
O
3
nanofibers (NFs) by dispersing Pt loaded ZIF-8 (Pt@ZIF-8)
nanoparticles in PVP/In(NO
3
)
3
precursors is designed. The difference
from Kim's work [25–27] is that the obtained Pt@ZIF-8 nanoparticles
will be affected by the solvent and the nitrates in the electrospun pre-
cursor. As we know, ZIF-8 is easily dissolved in acidic condition [28].
As shown in Fig. 1, as the metal ions (In
3+
) hydrolyze, protons will
generate in the reaction and etch ZIF-8 [29–31]. In high-valent metal
ion (In
3+
) aqueous solution, ZIF-8 dissolves, releasing of Zn
2+
ions and
Pt NPs. According to the experimental results, the average sizes of Pt
nanoparticles obtained in this way are only ∼3 nm. And the sensors
based on Pt-ZnO-In
2
O
3
composited nanofibers exhibited ultra-high
sensitive properties to acetone, great selectivity, fast response time and
low detection limit. Eventually, the related mechanism of gas sensing
will be illustrated in this paper.
2. Experimental section
2.1. Preparation process
2.1.1. Synthesis of ZIF-8
ZIF-8 was prepared as described in previous study [27]. Typically,
0.582 g of (Zn (NO
3
)
2
·6H
2
O and 0.6568 g of 2-methylimidazole were
dissolved in 25 mL methanol separately to obtain two kind of clear
solutions. Then, the solution of 2-methylimidazole was slowly added
into the (Zn(NO
3
)
2
·6H
2
O solution. The mixed solution was stirred under
magnetic stirring for 30 min and then was aged for another 24 h at
room temperature. The white precipitate was collected and purified by
centrifugation and washed with ethanol. After purification, the pre-
cipitate was dried at 80 °C for 20 h.
2.1.2. Synthesis of Pt@ZIF-8
Pt@ZIF-8 composites were synthesized by a modified method as
described in reference [27]. Simply, 80 mg ZIF-8 was dispersed in 5 mL
deionized water (DI-water). Then, 8 mg NH
4
PtCl
6
was added into the
solution above under stirring with magnetic bar during 2 h. Next, Pt
4+
in the cavity of ZIF-8 could be reduced to Pt by NaBH
4
solution.
Eventually, the as-prepared Pt@ZIF-8 suspension was purified by cen-
trifugation, washed with absolute alcohol and then dried in vacuum.
2.1.3. Synthesis of pristine In
2
O
3
NFs, ZnO-In
2
O
3
NFs and Pt-ZnO-In
2
O
3
NFs
Pt-ZnO-In
2
O
3
NFs were synthesized by electrospinning. For the
electrospinning process, 40 mg Pt@ZIF-8 were dispersed in 10 mL N, N-
dimethylformamide (DMF). To make the dispersion of Pt@ZIF-8 more
homogenous, ultrasonication technique was used. Then 0.5 g In
(NO
3
)
3
·4.5H
2
O were added in the solution above. After stirring for
5 min, a certain amount of PVP (polyvinyl pyrrolidone,
Mw = 1,300,000) were added into the solution with the concentration
of 12 wt%. Eventually, the solution was stirred for 5 h continually until
viscous precursor solution was completely formed. After fully stirring,
the solution was transferred into the syringe attached with a spinneret.
Some parameters in the electrospinning were as follows: a feeding
rate of 0.3 mL/h was kept by a syringe pump. A constant DC voltage of
16 ± 2 kV and distance (15 cm) were maintained between the tip of
the syringe needle and the stainless steel foil collector. The electrospun
nanofibers were collected and annealed in muffle furnace at 500 °C for
2 h (2 °C min
−1
) to remove the organic constituents of the PVP.
Similarly, ZnO-In
2
O
3
NFs were prepared by the same process
through using ZIF-8 instead of Pt@ZIF-8. And the pristine In
2
O
3
na-
nofibers were obtained without the addition of Pt@ZIF-8 or ZIF-8.
2.2. Characterization
X-ray diffraction (XRD) patterns were recorded by a Rigaku TTRIII
X-ray diffractometer with Cu-Kα1 radiation (λ = 0.15406 nm) in the
range of 20°- 80° (2θ). Scanning electron microscopy (SEM) images
were obtained using a JEOL JSM-7500F microscope with an accelera-
tion voltage of 10 kV. Transmission electron microscopic (TEM), high-
resolution transmission electron microscopic (HRTEM) images, and
selected area electron diffractive (SAED) pattern were obtained on a
JEOL JEM-3010 transmission electron microscope with an acceleration
voltage of 200 kV. Energy-dispersive X-ray spectroscopy (EDS) spots
pattern scanning analysis was performed by the transmission electron
microscopic attachment. X-ray photoelectron spectroscopy (XPS) ana-
lysis was conducted on an ESCALABMKII X-ray photoelectron spectro-
meter with Mg-Kα (1253.6 eV) achromatic X-ray source.
2.3. Fabrication and measurement of gas sensors
To fabricate the gas sensors, alumina substrates would be used
(thickness = 0.2 mm, area = 1.0 mm × 1.5 mm). The front side of the
substrate has two gold electrodes with a width of 0.3 mm. The back side
of the substrate has a micro-heater composed of Pt wires, RuO
2
layer
and Au electrodes. By adjusting electric current flowing through the
two leads, the working temperatures of sensors can be controlled. The
sensor temperature was measured using a FLIR temperature sensor. The
obtained nanofibers were respectively hot-pressed onto the alumina
substrates by Hot Press Machine (HS-XX40). The temperature of hot-
press is kept at 100 °C for 5 min to form a sensing layer with a thickness
of 10 ∼ 30 μm. The schematic illustration of the blank sensor coated
with the sensitive materials is shown in Fig. 2a. With the appropriate
heating and pressuring, the sensitive materials and electrodes can form
good contact. Following the hot-pressing step, the substrates were
calcined at 400 °C (2 °C min
−1
) for 2 h in air. This process is also helpful
to the stability of the sensors. After that, the substrates were welded on
the four feet socket. The schematic illustration of the fabricated sensor
is revealed in Fig. 2b.
The gas response properties of these sensors were researched with a
static gas-sensing characterization system under laboratory conditions
Fig 1. Schematic illustration of the etching process of ZIF-8 in the electrospun precursor solution.
L. Guo et al.
Sensors & Actuators: B. Chemical 272 (2018) 185–194
186