阐述了目前液压支架用立柱中缸管工艺的缺陷,改变传统的工艺,大胆采用新工艺,调整工艺顺序,针对不同的材质采用不同的工艺,减少了中缸管堆焊层处气孔的产生,并提高了堆焊层的硬度,此工艺提高了生产效率,目前在国内外处于领先水平,并被广泛推广。 【液压支架用立柱中缸管工艺革新】的文章主要探讨了当前液压支架中缸管制造工艺的不足,并提出了一种创新的工艺方案,旨在解决传统工艺存在的问题,提高生产效率和产品质量。 液压支架是煤炭开采中至关重要的设备,随着技术的发展,高端液压支架的需求增加,立柱作为其核心组件,其制造工艺的优化显得尤为重要。双伸缩立柱因其高昂的制造成本,推动了煤机厂家对工艺革新的探索。传统工艺中,中缸体的活塞头部分通过堆焊来达到所需的尺寸,但这种方法存在两个主要问题:一是堆焊层容易产生气孔,二是堆焊层的硬度低于母材,影响整体性能。 文章作者孙金兰指出,气孔的产生主要是由于待堆焊区的杂质,如油、水和铁锈等。之前的工艺虽然尝试了预热和去除铁锈,但难以完全消除冷却油带来的影响。为了解决这个问题,提出了新的工艺流程:先堆焊后粗镗内孔。这样可以避免油污在堆焊过程中的影响,从而减少气孔的产生。此外,对于不同材质的中缸管,如27SiMn和30CrMnSi,进行了不同的工艺实验。实验结果表明,对于27SiMn材质,先堆焊再调质可以显著提高堆焊层的硬度,达到与母材相近的水平。 新工艺的具体步骤包括下料、平端面、粗车镀铬区外圆、刀检待堆焊区外圆,然后直接进行堆焊,之后再进行粗镗内孔等后续步骤。对于30CrMnSi材质,先堆焊后调质并未明显改变堆焊层硬度,这提示我们不同材质可能需要针对性的工艺调整。 这一新工艺的应用不仅解决了气孔问题,提高了堆焊层的硬度,还提高了生产效率,因此在国内乃至国际上都处于领先地位,并得到了广泛的推广。这种工艺改进对于降低生产成本、提升液压支架性能和延长使用寿命具有重要意义,为煤炭开采行业的设备升级提供了技术支持。 【液压支架用立柱中缸管工艺革新】着重讲述了如何通过工艺创新解决传统制造过程中的技术难题,提高产品质量和生产效率,这对于煤炭开采行业的持续发展和机械设备的现代化具有深远影响。
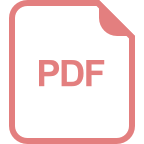
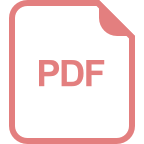
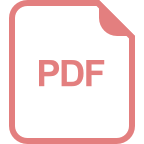
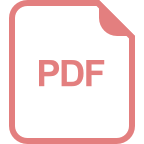
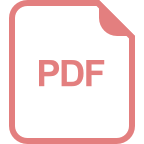
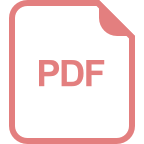
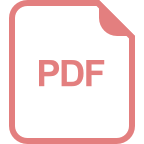
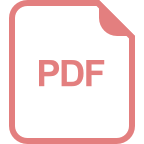
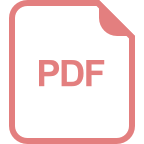
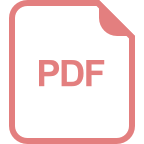
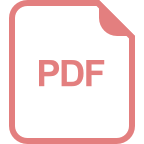
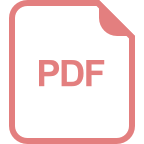
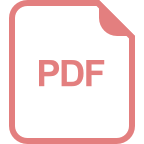
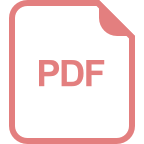
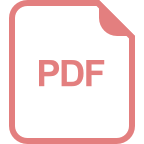
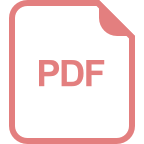
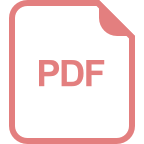
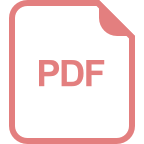
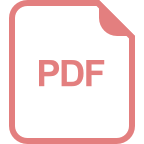
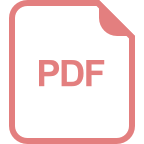
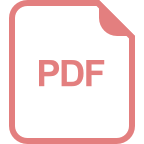
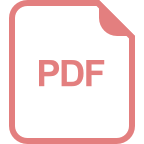
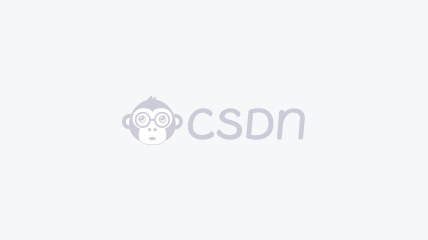

- 粉丝: 10
- 资源: 969
我的内容管理 展开
我的资源 快来上传第一个资源
我的收益
登录查看自己的收益我的积分 登录查看自己的积分
我的C币 登录后查看C币余额
我的收藏
我的下载
下载帮助

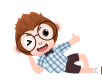
最新资源

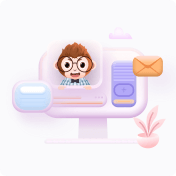
