没有合适的资源?快使用搜索试试~ 我知道了~
温馨提示
A description of a mathematical algorithm for simulating grain structures with straight and hyperbolic interfaces is shown. The presence of straight and hyperbolic interfaces in many grain structures of metallic materials is due to different solidificatio
资源推荐
资源详情
资源评论
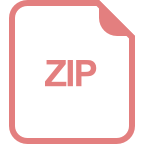
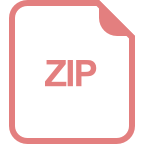
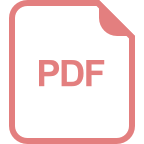
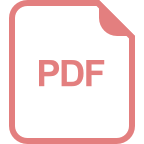
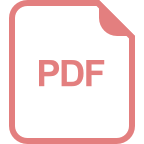
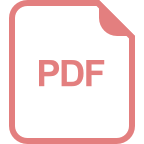
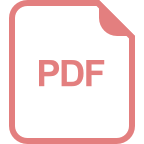
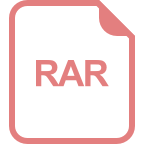
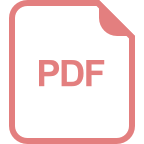
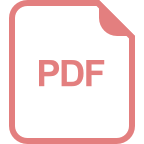
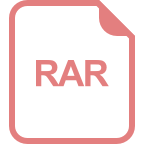
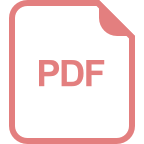
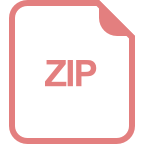
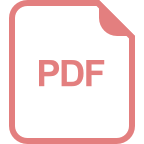
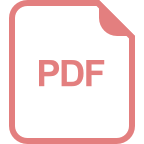
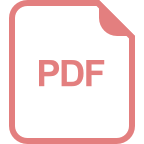
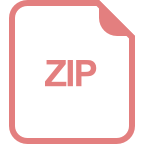
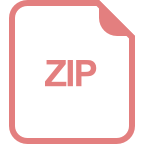
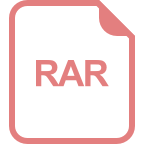
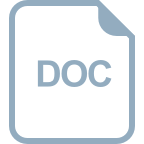
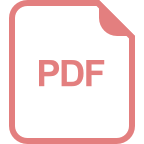
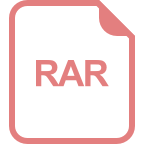
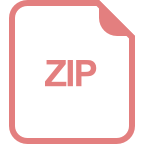
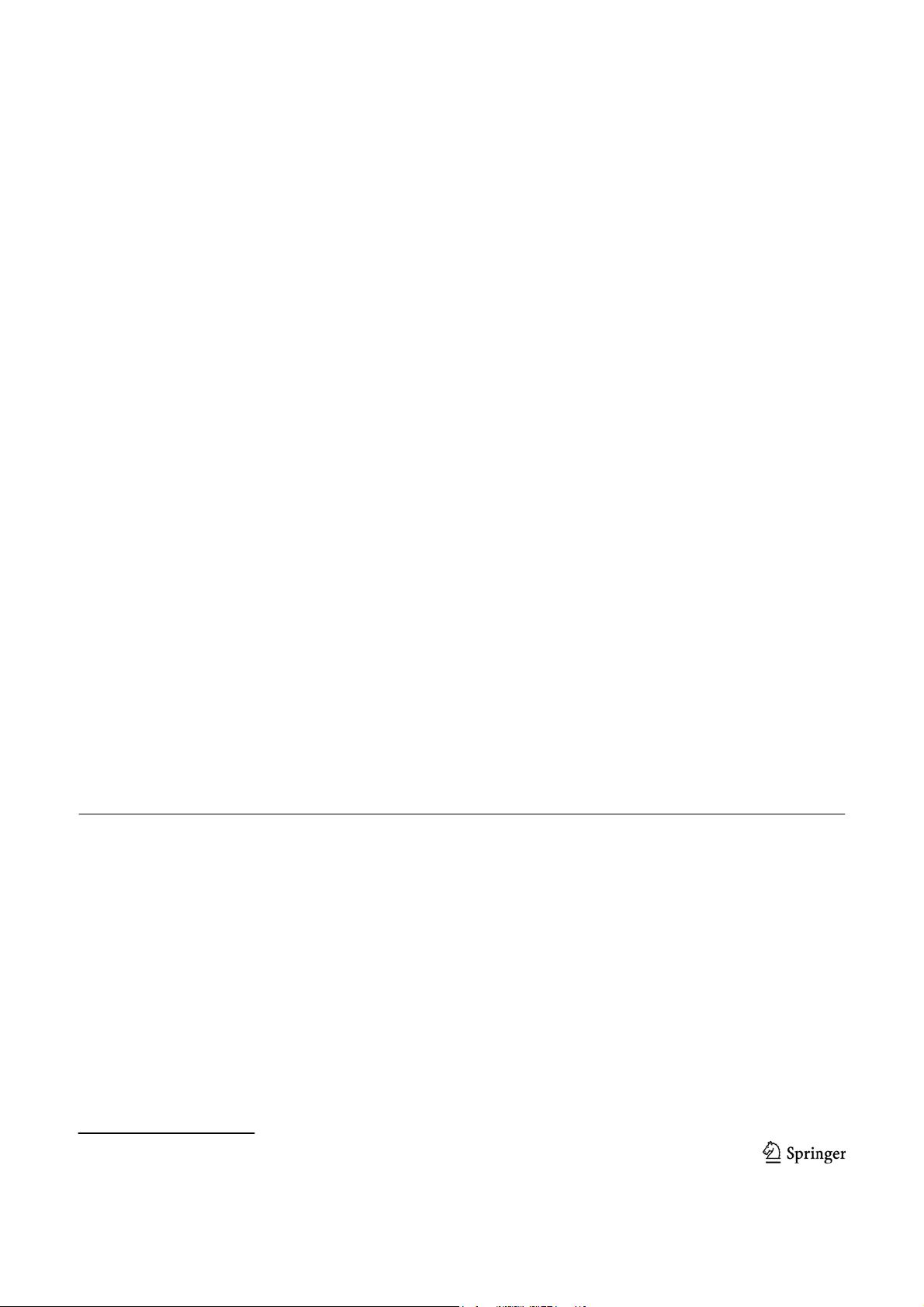
International Journal of Minerals, Metallurgy and Materials
Volume 19, Number 8, Aug 2012, Page 699
DOI: 10.1007/s12613-012-0616-0
Corresponding author: A. Ramírez-López E-mail: adaramil@yahoo.com.mx
© University of Science and Technology Beijing and Springer-Verlag Berlin Heidelberg 2012
A cellular automata model for simulating grain structures with straight and
hyperbolic interfaces
A. Ramírez-López
1, 2, 3)
, M. Palomar-Pardavé
1)
, D. Muñoz-Negrón
2)
, C. Duran-Valencia
3)
,
S. López-Ramirez
3)
, and G. Soto-Cortés
1)
1) Materials and Energy Department, Metropolitan Autonomous University, Mexico
2) Department of Industrial Engineering, Technological Autonomous Institute of Mexico, Mexico
3) Department of Molecular Engineering, Mexican Institute of Petroleum, Mexico
(Received: 11 May 2011; revised: 4 July 2011; accepted: 11 July 2011)
Abstract: A description of a mathematical algorithm for simulating grain structures with straight and hyperbolic interfaces is shown. The
presence of straight and hyperbolic interfaces in many grain structures of metallic materials is due to different solidification conditions, in-
cluding different solidification speeds, growth directions, and delaying on the nucleation times of each nucleated node. Grain growth is a
complex problem to be simulated; therefore, computational methods based on the chaos theory have been developed for this purpose.
Straight and hyperbolic interfaces are between columnar and equiaxed grain structures or in transition zones. The algorithm developed in this
work involves random distributions of temperature to assign preferential probabilities to each node of the simulated sample for nucleation
according to previously defined boundary conditions. Moreover, more than one single nucleation process can be established in order to gen-
erate hyperbolic interfaces between the grains. The appearance of new nucleated nodes is declared in sequences with a particular number of
nucleated nodes and a number of steps for execution. This input information influences directly on the final grain structure (grain size and
distribution). Preferential growth directions are also established to obtain equiaxed and columnar grains. The simulation is done using rou-
tines for nucleation and growth nested inside the main function. Here, random numbers are generated to place the coordinates of each new
nucleated node at each nucleation sequence according to a solidification probability. Nucleation and growth routines are executed as a func-
tion of nodal availability in order to know if a node will be part of a grain. Finally, this information is saved in a two-dimensional computa-
tional array and displayed on the computer screen placing color pixels on the corresponding position forming an image as is done in cellular
automaton.
Keywords: grain growth; interfaces; grain size and shape; computational methods; algorithms; cellular automata; computer simulation
1. Introduction
Simulation of grain structures is a very important topic in
materials science. Metallic pieces are frequently processed
and formed by foundry, laminated, rolling, etc. During manu-
facturing and processing, different grain sizes and mor-
phologies are obtained according to particular solidification
conditions and thermal treatments. Fractals, stochastic
methods, cellular automata, models based on Monte Carlo,
random walk, and the chaos theory have been employed to
simulate the anisotropic features of grain structures and the
phenomena related such as recrystallization and grain de-
formation during processing.
Many authors [1-15] have developed mathematical mod-
els to simulate grain growth during solidification of metallic
materials (metals and alloys). The beginners [2] used basic
geometrical models due to the limited computational capaci-
ties. Nevertheless, the development of new mathematical
methods, more efficient algorithms, and the increment in
computational data speed and storage capacities have been
possible to solve complex problems that involve no-regular
geometries and random processes using Monte Carlo [1, 2, 4,
7] and cellular automaton [5, 8, 11-15]
methods in problems
related to materials science. Some of these authors [1, 4-8,
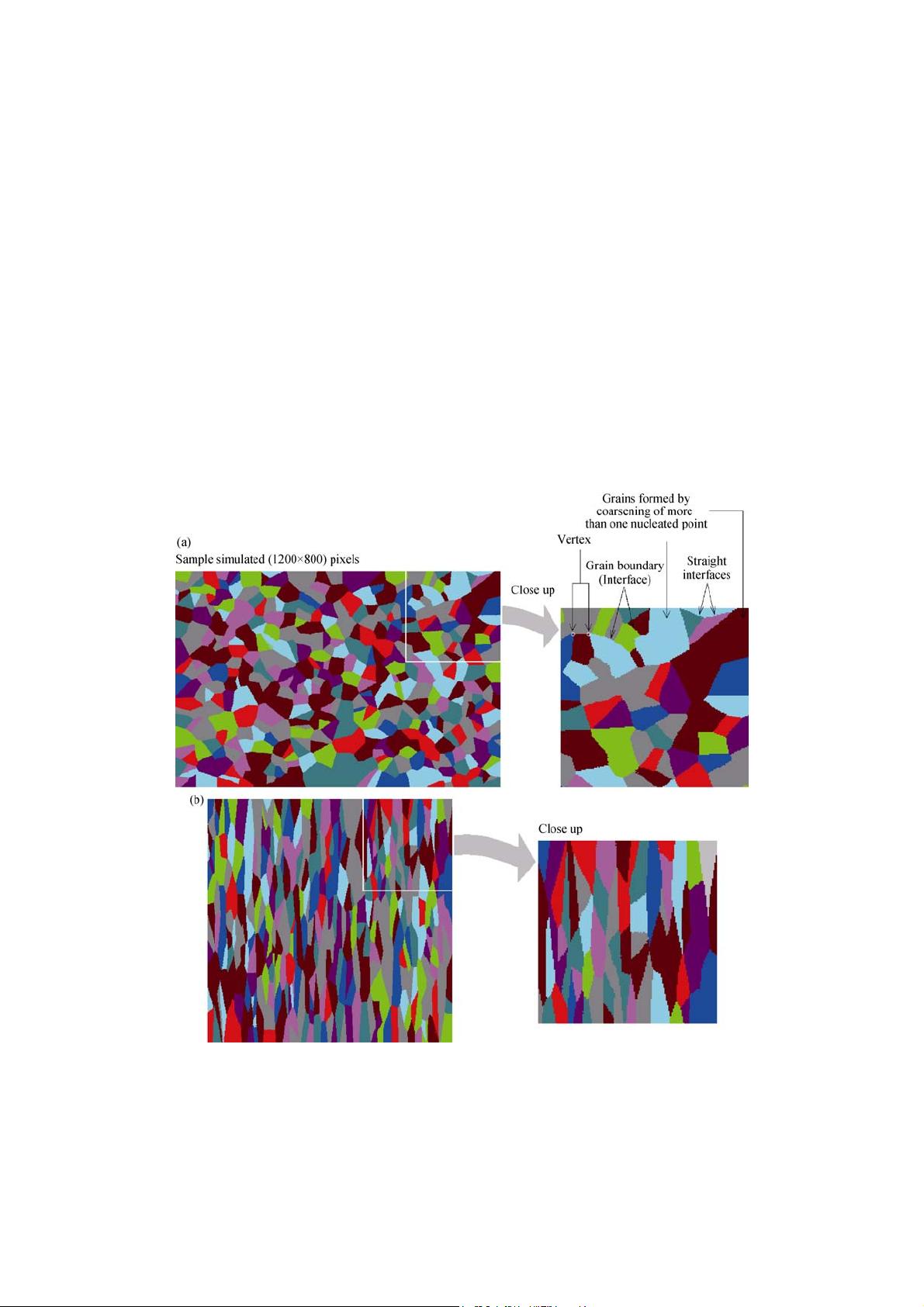
700 Int. J. Miner. Metall. Mater., Vol.19, No.8, Aug 2012
10-12] have developed models for solidification processes
as a function of solid and liquid fractions for different metals.
Others [1-4, 6, 9, 12-15] have been working in models to
simulate dendrite growth, which is the basic structure in
primary metallic products obtained after foundry.
In a previous work, Ramírez et al. [15] explained the de-
velopment of a basic computational algorithm to create
grain structures as a function of an initial stochastic tem-
perature distribution during the solidification of a squared
metallic sample. Heterogeneous distributions of temperature
provide nodes with particular probabilities to be nucleated.
The results are zones with big and small grains. The assig-
nation of preferential growth directions gives samples with
different grain sizes. Nevertheless, in the original algorithm,
there was only one single nucleation execution.
The grain structures formed in metals are heterogeneous
and the grain morphology can also be very different due to
the factors involved in the manufacturing process. Grains
with equiaxed and columnar morphologies, with different
sizes and distributions, can be simulated as shown in Figs.
1(a) and 1(b), respectively, using the original algorithm de-
veloped [15]. Nevertheless, the interfaces between the grains
(grain boundaries) are always straight (straight lines for
two-dimensional (2D) models and flat planes for three-di-
mensional (3D) models) as shown in better detail in the
close-ups, which show the boundaries between these. This
work describes an improved algorithm to generate more
complex 2D grain structures. The new algorithm includes
multiple nucleation sequences to generate different grain
sizes and hyperbolic interfaces between them.
Fig. 1. Different grain structures with straight interfaces: (a) equiaxed grains; (b) columnar grains.
Straight lines are presented in grain boundaries during the
evolution of the simulation as shown in Figs. 1(a) and 1(b).
These are formed because all the nodes are nucleated in only
one single sequence and because all of them have the same
growth rate. Nevertheless, this does not happen during real
solidification.
Fig. 1(a) shows an equiaxed grain structure. This kind
resulted after the metal is foundry and cast. Grain size dis-
tribution is frequently a function of the nucleation node dis-
tribution in the sample and the growth procedure. Neverthe-
剩余11页未读,继续阅读
资源评论
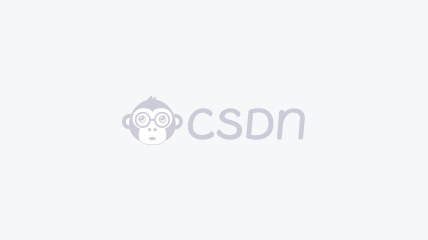

weixin_38665814
- 粉丝: 6
- 资源: 982
上传资源 快速赚钱
我的内容管理 展开
我的资源 快来上传第一个资源
我的收益
登录查看自己的收益我的积分 登录查看自己的积分
我的C币 登录后查看C币余额
我的收藏
我的下载
下载帮助

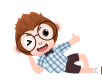
最新资源
- matlab平台的垃圾识别定位.zip
- matlab平台的疲劳检测GUI设计.zip
- matlab平台的垃圾分类系统.zip
- matlab平台的苹果水果分级.zip
- matlab平台的漂浮物识别.zip
- matlab平台的疲劳专注度检测系统.zip
- matlab平台的脐橙水果分级.zip
- 连续小波变换加卷积神经网络进行轴承故障诊断
- matlab平台的人脸考勤设计.zip
- matlab平台的人脸购物系统.zip
- matlab平台的人脸识别.zip
- matlab平台的人脸识别系统.zip
- matlab平台的人脸门禁系统.zip
- matlab平台的手势识别设计.zip
- matlab平台的手势控制系统.zip
- matlab平台的手势识别.zip
资源上传下载、课程学习等过程中有任何疑问或建议,欢迎提出宝贵意见哦~我们会及时处理!
点击此处反馈


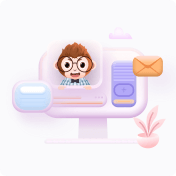
安全验证
文档复制为VIP权益,开通VIP直接复制
