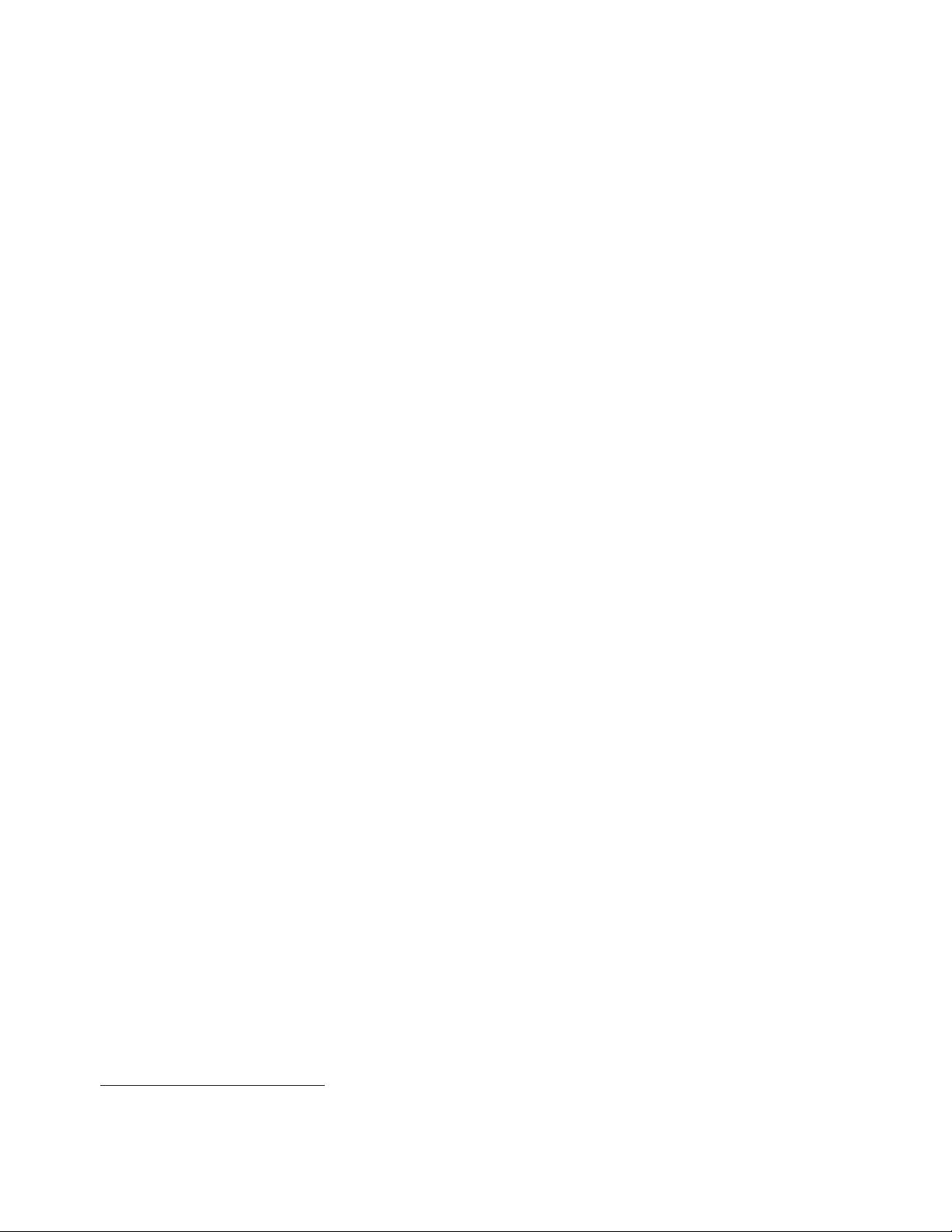
1 INTRODUCTION
Mobile operational ground robot systems (a combination of
ground mobile robot and mechanical arm), are utilized in
disaster relief ,anti-terrorism and anti-riot occasions etc.
They have been fully verified as well as widely recognized.
The idea of combining the operational ability of mechanical
arms and the mobility of mobile robots thus expanding the
scope of application of robots is highly attractive.
With the extension of robots’ applications, people are more
eager to witness that flying robots can exert active
influences on the environment. Installing an operating
manipulator mechanism onto flying robot platform thus
endowing the robot active operation capability in complex
3D working environment is highly practically significant.
The design idea of most flying robots is to avoid contact
with the environment. Yet RUAVs have the characteristics
of hovering and high mobility, and can replace humans in
acquiring information in risky and hazardous
environments. For this reason, people are hoping that the
RUAVs can conduct maneuvers that effectively contact the
environment. To realize this hope, the research of the
contact between RUAV and its environment has already
become a hotspot, and has attracted extensive attention in
the flying robot domain.
The concept of combining a RUAV and a manipulator has
been preliminarily validated by several research institutes.
The Yale Aerial Manipulator [1] has a compliant gripper
which can grasp objects while landed or hovering. Here, the
system stable area was evaluated with reference to the
This work is supported by National Natural Science Foundation of China
(Project 61433016 and 61273025)
position of the payload relative to the system’s center of
gravity (CG). The University of Pennsylvania’s research
[2] adopted the method of parameter estimation, and
estimated the uncertain parameters of RAM when grasping
payloads. The RAM system from DLR [3] is loaded with a
7-DOF industrial manipulator and is able to grasp long
sticks on the ground. Here, the control issues involving the
CG change of the RAM system when grasping had been
studied. In addition, there are some other researches on
multi-rotor aircraft mounted with a manipulator which can
grasp lightweight objects [3-5].
The examples mentioned above all use electric motors to
drive the manipulators, and all mount the manipulator on
the RUAV to grasp light weight or fixed shape objects. Yet
in reality, many demands cannot be met by simple grasping
maneuver, such as the maintenance of high voltage power
transmission lines. The severing off operation of damaged
power lines requires great force and torque. This operation
requires the end-effector to be very powerful and finish the
cutting off operation in a short time. However, none of the
aforementioned papers discussed such an operation. Also
none of the end-effectors mentioned in those papers has
adequate power to perform this kind of operation. If an
electric motor is chosen to drive the end-effector, the gear
box will become a heavy burden for the RUAV and the
vibration of the motor and the gear box will induce extra
disturbance.
To solve this problem, a novel RUAV mobile operating
system is proposed which is composed of an RUAV and a
multiple degrees of freedom (DOF) miniature hydraulic
manipulator shown in Figure 1. Hydraulic system is chosen
because it has many advantages compared to electric or
pneumatic systems. Power in the hydraulic system is
Modeling and Controller Design of Hydraulic Rotorcraft Aerial Manipulator
Lin Tianyu
1,2
, Li Yongzhe
3
, Qi Juntong
1
, Meng Xiangdong
1
, Han Jianda
1
1. State Key Laboratory of Robotics, Shenyang Institute of Automation, Chinese Academy of Sciences, Shenyang 110016
E-mail: qijt@sia.cn, xdmeng09@163.com, jdhan@sia.cn
2. Shenyang Ligong University, Shenyang 110159
E-mail: razorwoods@126.com
3. Northeastern University, Shenyang 110819
Abstract: Traditional Rotary-wing Unmanned Aerial Vehicles (R-UAV) are mostly utilized to conduct surveillance.
Installing a mechanical manipulator on R-UAV will result a Rotorcraft Aerial Manipulator (RAM) system. A RAM
system enlarges the R-UAV’s application scope. The RAM system proposed by this research is composed of R-UAV and
a miniature hydraulic manipulator. With the combined merits of the two systems, this RAM system has enhanced
flexibility and is capable of fulfilling more tasks. The hovering mode dynamics model of the RAM is established
referring to the working characteristics of the hydraulic manipulator. An LQR controller is used to control the planar
motion of the hydraulic manipulator. The motion of the manipulator will exert coupled force and moment influence on
the RAM system. This coupled influence is taken as a disturbance to the R-UAV system which is restrained by a robust
controller. Finally, through simulation, the effectiveness of the established dynamics model and the proposed control
strategy is verified.
Key Words: RAM, Hydraulic manipulator, Modeling, LQR controller, Robust controller
5446
978-1-4799-7016-2/15/$31.00
c
2015 IEEE