
weixin_38640985
- 粉丝: 8
- 资源: 965
最新资源
- 毕设和企业适用springboot企业协作平台类及企业健康管理平台源码+论文+视频.zip
- 毕设和企业适用springboot企业协作平台类及运动管理平台源码+论文+视频.zip
- 毕设和企业适用springboot企业协作平台类及在线招聘平台源码+论文+视频.zip
- 毕设和企业适用springboot企业协作平台类及招聘管理平台源码+论文+视频.zip
- 毕设和企业适用springboot企业协作平台类及社会服务平台源码+论文+视频.zip
- 毕设和企业适用springboot企业协作平台类及全景数据分析平台源码+论文+视频.zip
- 毕设和企业适用springboot企业协作平台类及社交媒体平台源码+论文+视频.zip
- 毕设和企业适用springboot企业协作平台类及智能农场管理系统源码+论文+视频.zip
- 毕设和企业适用springboot企业协作平台类及智能配送系统源码+论文+视频.zip
- 毕设和企业适用springboot企业协作平台类及智能交通管理平台源码+论文+视频.zip
- 毕设和企业适用springboot企业云存储平台类及AI数据标注平台源码+论文+视频.zip
- 毕设和企业适用springboot企业云存储平台类及健康数据分析系统源码+论文+视频.zip
- 毕设和企业适用springboot企业云存储平台类及电影票务系统源码+论文+视频.zip
- 毕设和企业适用springboot企业协作平台类及视频内容分发平台源码+论文+视频.zip
- 毕设和企业适用springboot企业云存储平台类及跨平台销售系统源码+论文+视频.zip
- 毕设和企业适用springboot企业云存储平台类及社交电商平台源码+论文+视频.zip
资源上传下载、课程学习等过程中有任何疑问或建议,欢迎提出宝贵意见哦~我们会及时处理!
点击此处反馈


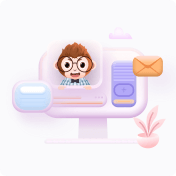