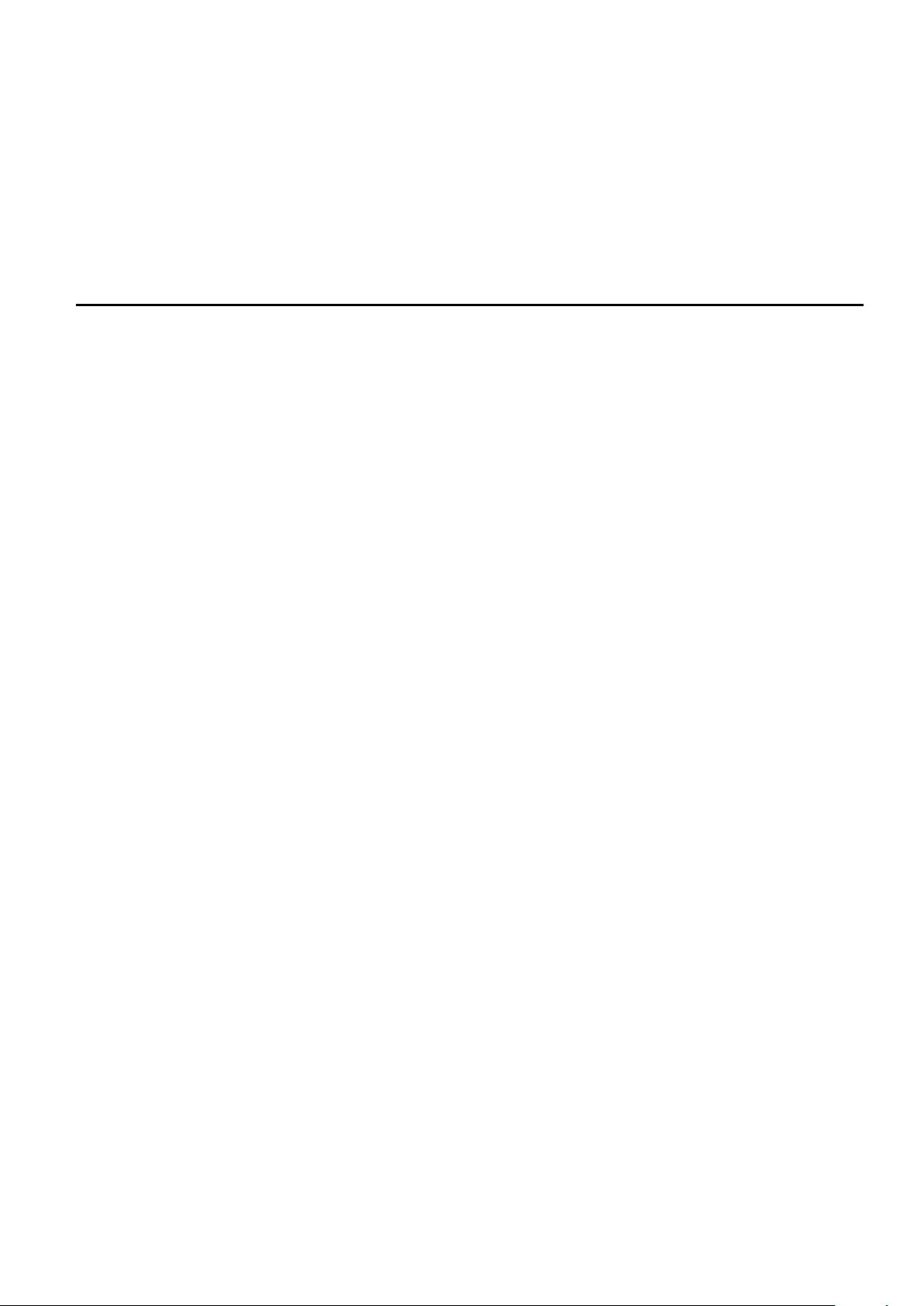
Fault-tolerant control scheme for manipulator with actuator and sensor failure 167
Hong Wang received his BS from Huainan University of Mining Engineering, Huainan, China in
1982, and MS and PhD from the Huazhong University of Science and Technology, Huazhong,
China in 1984 and 1987, respectively. He was a research fellow with Salford, Brunel, UK, and
Southampton Universities, Southampton, UK from 1988 to September 1992. He then joined
UMIST in 2002, and has been a Professor of process control with the Control Systems Centre,
University of Manchester, Manchester, UK since 2002. His current research interests include
stochastic distribution control, fault detection and diagnosis. He has published 200 papers and
three books. He was an Associate Editor of the IEEE Transactions on Automatic Control
and serves as an Associate Editor for IEEE Transactions on Control Systems Technology and
an editorial board member for the Journal of Measurement and Control, Transactions of the
Institute of Measurement and Control, and Automatica Sinica.
1 Introduction
Fault tolerant control (FTC) is very important to be applied
in manipulator systems. Due to the nature of operation,
it might not be feasible to intervene or rectify the fault
immediately when it is detected by fault detection and
isolation (FDI) module. FTC provides an effective way to
keep safe behaviour and a certain level of performance
even in the presence of faults (Muscio and Pierri, 2012).
Recently, the FTC problems have been intensively studied.
In general, FTC can be classified as passive FTC and
active FTC. These two methods use different design ideas
for the same objective: to preserve an acceptable level
of performance even in the presence of system faults. In
passive FTC, the controller need not to be adjusted to adapt
to unexpected fault. Since the fixed controller can not cover
all faulty scenarios, the limited tolerant capacity is the main
issue of the method. In addition, as pointed in Jiang and
Yu (2012), it focuses more on stability and involves the
drawback of conservation. In active FTC, the controller
is reconstructed based on the real-time information from
FDI scheme. In comparison with passive FTC, active FTC
exhibits a more promising performance and adaptability to
a wider class of faults. Consequently, some intensive works
have been done on this area during the last two decades.
In general, the design of active FTC consists of two
parts:
1 to design an effective FDI module to provide
information about the fault
2 to reconfigure controller to achieve stability and
acceptable control performance.
Our focus is on the second part. With respect to FDI, the
interesting authors can be referred to Capisani et al. (2012).
In Patton and Klinkhieo (2009), an output feedback control
is adopted and the faults are estimated and compensated
within an adaptive control scheme with required stability
and robustness. An internal model-based FTC scheme is
developed in Bonivento et al. (2004) for manipulator with
various sinusoidal torque disturbances acting on the joint.
In the method, an augmented tracking controller is proposed
using internal model to compensate the unknown fault
disturbance torque. In addition, it is able to provide FDI
information. Recently, a fault tolerant framework based
on sliding mode technique is provided in Khireddine and
Boutarfa (2013) for manipulator with sensor or motor
failures. In the method, the unmeasurable state and fault
information are estimated real-time via observer and then
are compensated in control input. Finally, the capacity of
tolerant is preserved without the intervention of human.
In addition, there are many other methods, such as
backstepping (He et al., 2013) and output-feedback H
∞
control (Sigueira et al., 2007) used in FTC for manipulator.
At present, most of the existing control schemes for
manipulator’s FTC are asymptotically stable control law
which implies convergent time is infinite. Obviously, the
finite time convergence is more desirable in practice and
it exhibits higher accuracy and better disturbance rejection
(Bhat and Bernstein, 2000).
The main objective of the work is to develop a FTC
scheme ensuring the actuator fault and unknown states
caused by sensors faults can be reconstructed in finite time.
Then, a continuous multivariable control law is established
based on the estimated information, which renders the
stabilisation of the closed-loop system in finite time. As a
result, the stabilisation of the system can be preserved even
in the presence of faults.
The rest of paper is organised as follows. In Section 2,
the problem is presented. In Section 3, the fault control
schemes using multivariable second order sliding mode
technique is described. The simulation results are provided
in Section 4 and the main conclusions are finally
summarised in Section 5.
2 Problem formulation
Consider the following n-joint robot manipulator
τ = M (q)
¨
q + C(q,
˙
q)
˙
q + G(q) (1)
where τ ∈ R
n
is control torque, q ∈ R
n
is generalised
coordinate vector, M (q) ∈ R
n×n
is inertia matrix,
C(q,
˙
q) ∈ R
n
represents centripetal and Coriolis torques
and G(q) ∈ R
n
is the vector of gravitational torques. For
brevity, let position states x
1
= q, velocity states x
2
=
˙
q.
Then,system (1) is transformed into the following form
˙
x
1
= x
2
,
˙
x
2
= f (x
1
, x
2
) + g(x
1
)u (2)