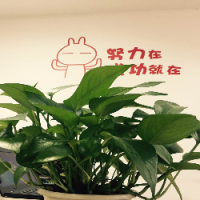

结冰架构
- 粉丝: 945
- 资源: 28万+
最新资源
- ASL6328芯片规格说明书
- 基于Matlab实现智能体一阶有领导者仿真(源码+数据).rar
- 独立公众号版本微信社群人脉系统社群空间站最新源码+详细教程
- 森林图像数据集(2700张图片).rar
- 《基于Comsol仿真模拟的岩石损伤研究-水力压裂实验探究》,利用Comsol仿真模拟技术精确预测水力压裂过程中岩石损伤情况,comsol仿真模拟水力压裂岩石损伤 ,关键词:COMSOL仿真;水
- 自由方舟管理后台通用模板-基于TDesign二次优化
- 《学习CRUISE M热管理的视频教程及文档解说,无需模型,轻松入门》,CRUISE M热管理视频教程:无模型,文档解说,轻松学习掌握热管理知识,录的CRUISE M热管理视频,有文档解说,没有模型
- 洛杉矶犯罪数据集概览 (2020年至今),犯罪事件数据集,犯罪影响因素
- 电信客户流失数据集,运营商流失客户数据集
- FinalBurn Neo源代码
- 基于积分型滑模控制器的永磁同步电机FOC转速环设计及仿真模型参考,基于积分型滑模控制器的永磁同步电机FOC转速环设计及仿真模型参考,基于积分型滑模控制器的永磁同步电机FOC 1.转速环基于积分型滑模面
- 智能车辆模拟系统:深度探究多步泊车,平行泊车与垂直泊车的仿真应用,《深入探讨carsim仿真技术下的多步泊车策略:平行泊车与垂直泊车的实现与优化》,carsim仿真多步泊车,平行泊车和垂直泊车 ,核心
- BMS模块Simulink开发基于算法,基于Simulink开发的BMS算法:包含SOC计算、故障处理与状态监测的充放电控制策略图解,BMS Simulink 所有算法基于Simulink开发 BMS
- 犯罪率与社会经济因素数据集,探讨了犯罪率与各种社会经济因素之间的关系,如教育水平、就业率、中位收入、贫困率和人口密度涵盖了1000个地区的数据
- ASL6328芯片原理图-V1.1
- 精品源码Javaweb仓库管理系统项目源码
资源上传下载、课程学习等过程中有任何疑问或建议,欢迎提出宝贵意见哦~我们会及时处理!
点击此处反馈


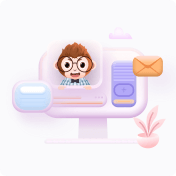