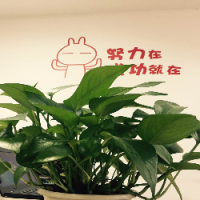

结冰架构
- 粉丝: 917
- 资源: 28万+
最新资源
- 永磁同步电机直接转矩控制DTC仿真模型,三相PMSM直接转矩控制matlab仿真算法,基于matlab simulink搭建 附参考资料,简单电子资料
- 2025年春节烟花特效html
- Python_利用AI大模型一键生成高清短视频 Generate short videos with one clic.zip
- Python_连接到任何数据源,轻松可视化仪表板和共享您的数据.zip
- Python_利用GDB开发和逆向工程变得容易.zip
- 永磁同步电机PMSMsimulink仿真,模型参考自适应方法在线辩识转动惯量,可选变增益,纯手工搭建,附参考资料
- Python_领先的ETL ELT数据管道数据集成平台,从api数据库文件到数据仓库、数据湖、数据湖,包括自托管和云托.zip
- Python_令人敬畏的开源启动替代知名SaaS产品列表.zip
- Python_流氓接入点框架.zip
- Python_马尔:口齿不清.zip
- Python_免费超快副驾驶替代Vim和Neovim.zip
- Python_麦考夫核心麦考夫人工智能平台.zip
- Python_每个人的开源机器学习框架.zip
- Python_免费的计算机编程类中文书籍欢迎投稿.zip
- 光伏逆变器仿真模型,boost加NPC拓扑结构,基于MATLAB Simulink建模仿真 具备中点平衡SVPWM控制,正负序分离控制,可以进行功率调度仿真 仿真模型使用MATLAB 2017b搭
- Python_免费和开源企业资源规划ERP.zip
资源上传下载、课程学习等过程中有任何疑问或建议,欢迎提出宝贵意见哦~我们会及时处理!
点击此处反馈


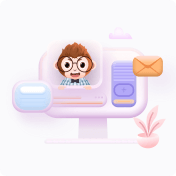