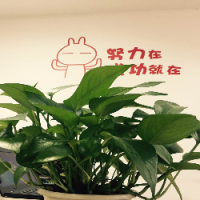

结冰架构
- 粉丝: 917
- 资源: 28万+
最新资源
- 基于微信小程序的网上商城+ssm-微信小程序毕业项目,适合计算机毕-设、实训项目、大作业学习.rar
- 教学辅助微信小程序设计+ssm-微信小程序毕业项目,适合计算机毕-设、实训项目、大作业学习.rar
- 基于微信小程序的童装商城的设计与实现+ssm-微信小程序毕业项目,适合计算机毕-设、实训项目、大作业学习.rar
- Python 实现GARCH分位数时间序列预测的设计项目实例(含完整的程序,GUI设计和代码详解)
- 家庭记账本的设计与实现+ssm-微信小程序毕业项目,适合计算机毕-设、实训项目、大作业学习.rar
- 基于微信小程序的校园二手交易平台系统设计与开发ssm-微信小程序毕业项目,适合计算机毕-设、实训项目、大作业学习.rar
- 基于微信小程序的小区疫情防控ssm-微信小程序毕业项目,适合计算机毕-设、实训项目、大作业学习.rar
- 流浪动物救助小程序--论文pf-微信小程序毕业项目,适合计算机毕-设、实训项目、大作业学习.zip
- 开放实验室预约管理系统pf-微信小程序毕业项目,适合计算机毕-设、实训项目、大作业学习.zip
- 美食推荐系统的微信小程序--论文pf-微信小程序毕业项目,适合计算机毕-设、实训项目、大作业学习.zip
- 基于小程序的社区超市管理系统springboot-微信小程序毕业项目,适合计算机毕-设、实训项目、大作业学习.rar
- 基于微信小程序的在线选课系统springboot-微信小程序毕业项目,适合计算机毕-设、实训项目、大作业学习.rar
- 生活小助手微信小程序_k1s0l-微信小程序毕业项目,适合计算机毕-设、实训项目、大作业学习.zip
- 农场管理系统(小程序)--论文pf-微信小程序毕业项目,适合计算机毕-设、实训项目、大作业学习.zip
- 基于微信小程序的学生公寓电费信息管理系统+ssm-微信小程序毕业项目,适合计算机毕-设、实训项目、大作业学习.rar
- 农业电商服务系统_30249--论文-微信小程序毕业项目,适合计算机毕-设、实训项目、大作业学习.zip
资源上传下载、课程学习等过程中有任何疑问或建议,欢迎提出宝贵意见哦~我们会及时处理!
点击此处反馈


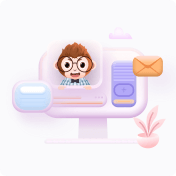