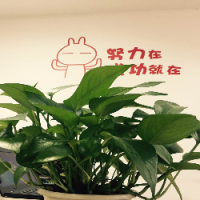

结冰架构
- 粉丝: 916
- 资源: 28万+
最新资源
- 多目标点移动机器人改进路径规划算法 送餐机器人,AGV室内机器人仿真路径规划 采用改进A*算法融合模拟 火算法,规划多目标点路径规划 解决路径与障碍物相撞,AGV不斜穿室内区间,采用水平垂直方向移动
- 基于C#语言的上海水电服务端及MQTT服务端设计源码
- 基于carsim与matlab simulink的联合仿真,采用五次多项式实时规划,控制量为节气门开度,制动压力与方向盘转角,弯道道模型
- 动态加载dll控制软件框架,可自主根据接口扩展dll,配置到主框架运行 开发语言:C# + Halcon 1.运动控制,相机采图; 2.实时加载dll工具流程,动态加载窗口; 3.IO控制获取工
- 基于PHP、JavaScript、CSS、HTML、Shell语言的芊雅自助台球系统设计源码
- 基于微信小程序技术的书店门户全功能设计源码
- 表贴式永磁同步电机非线性磁链观测器无感仿真,该仿真在初始位置确定后能够直接起动电机,在低速区不需要高频信号注入,起动电流远远小于if起动,转速和位置在速度上来后精度高,即使在低速也有不错的性能 起动
- 基于Vue框架的新闻资讯与商城前后端分离项目设计源码
- 前端分析-2023071100789
- 基于hyperf框架的全新Vue3+Antdv2.1后台管理系统设计源码
- factoryio工厂流水线仿真程序 使用简单的梯形图与SCL语言编写,通俗易懂,起到抛砖引玉的作用,比较适合有动手能力的入门初学者 软件环境: 1、西门子编程软件:TIA Portal V15(博
- 基于Go语言的secpaver安全策略开发工具源码
- 西门子PCS7自定义单位教程 1.西门子PCS7非标单位的程序编写: 例如:% LEL,%VOL 2.自定义的单位如何立即生效 3.在CFC中通道输入和输出块的单位引脚,直接指定自定义单位,WIN
- 基于TypeScript开发的鸿蒙操作系统录音机设计源码
- 基于Vue框架的慕课在线教育平台设计源码
- 非线性振动,非线性动力学分岔,混沌
资源上传下载、课程学习等过程中有任何疑问或建议,欢迎提出宝贵意见哦~我们会及时处理!
点击此处反馈


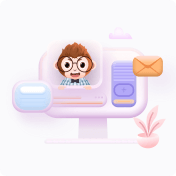