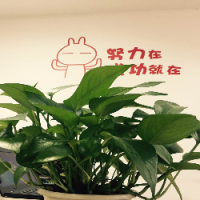

结冰架构
- 粉丝: 916
- 资源: 28万+
最新资源
- 基于matlab的传统滤波、Butterworth滤波、FIR、移动平均滤波、中值滤波、现代滤波、维纳滤波、自适应滤波、小波变,七种滤波方法,可替自己的数据进行滤波,程序已调通,可直接运行
- 基于Java语言开发的ASR+TTS+声纹识别功能的智能聊天小程序设计源码
- 含风电-光伏-光热电站电力系统N-k安全优化调度模型 关键词:N-K安全约束 光热电站 优化调度 参考文档:参考《光热电站促进风电消纳的电力系统优化调度》光热电站模型; 仿真软件: matlab+y
- 基于TypeScript和JavaScript的每日饮食与运动记录工具设计源码
- 基于JavaScript的仪器预约系统设计源码
- 基于Vue的依沫一站式内容资源变现博客设计源码
- 基于SSM框架与微信小程序的宠物管理系统源码设计
- 基于宝塔Linux面板7.9.0免费版的7.9.2兼容CSS美化设计源码
- 基于ActiveReports的C#报表控件设计源码
- 基于C#与Shell语言的SangServerTool服务器DDNS与SSL证书申请工具设计源码
- 基于SpringBoot+Vue的智能停车场管理系统设计源码
- 基于Shell、Python、PHP、HTML的zzxia-op-super-invincible-lollipop代码构建部署运维工具箱设计源码
- 华为FusionCompute 8.0.1 集成设计指导书
- 基于C语言实现的新型疫苗接种管理系统设计源码
- 基于JavaScript和微信小程序的抖音本地生活团购系统源码搭建与部署方案
- 电力电子boost升压电路MATLAB仿真,pi控制闭环(15r)滑模控制改进版(29r)24升48V,电压可修改 基于反激变器的升压电路,降压电路boost buck的MATLAB仿真,PLECS也
资源上传下载、课程学习等过程中有任何疑问或建议,欢迎提出宝贵意见哦~我们会及时处理!
点击此处反馈


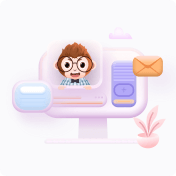