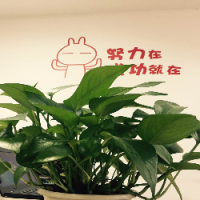

结冰架构
- 粉丝: 926
- 资源: 28万+
最新资源
- 基于Python的学生会管理系统后端开发设计源码
- Comsol HM耦合模型与MATLAB裂缝函数在岩石水力压裂损伤模拟中的应用,基于COMSOL的HM耦合模型与MATLAB裂缝函数模拟水力压裂岩石损伤与裂隙扩展,comsol水力压裂岩石损伤耦合,裂
- 基于C++的图书借阅系统QT界面设计源码
- 基于Java语言的简单打分app设计源码
- 基于COMSOL两相流模型模拟静水动水条件下的注浆过程,基于COMSOL两相流模型模拟静水动水条件下的注浆过程,comsol两相流模型,静水动水条件下注浆模拟 ,关键词:Comsol两相流模型;静水
- 基于Expo框架的Tsx医疗APP前端设计源码
- 基于Vue和JavaScript的HTML门户网站设计源码
- 基于遗传算法和模态置信准则的振动传感器优化布置策略-实现成本效益最大化与系统可靠性的提升,基于遗传算法和模态置信准则的振动传感器优化布置策略-实现成本效益最大化与系统可靠性的提升,基于模态置信准则
- 基于Vue框架的报表填报系统设计源码
- 六轴机器人仿真与自制轨迹规划系统:姿态插补与关节及笛卡尔空间轨迹规划的深度解析,六轴机器人仿真与自制轨迹规划系统:姿态插补与关节及笛卡尔空间轨迹规划技术解析,六轴机器人仿真轨迹规划姿态插补关节空间轨迹
- 基于JavaScript的红色知识图谱项目源码及配套资源
- 基于C#开发的web2投票系统设计源码
- 基于DSP28335控制的先进三相交错双向DCDC变换器技术探究,DSP28335三相交错双向DCDC变换器技术细节解析与实践应用,基于DSP28335的三相交错双向DCDC变器 ,基于DSP2833
- 基于Java、Vue、JavaScript、HTML、Shell的综合性人口数据库管理系统设计源码
- 基于Java和Vue的德育素质评价系统设计源码
- 基于JavaScript与Java技术的唱跳rap篮球主题应用设计源码
资源上传下载、课程学习等过程中有任何疑问或建议,欢迎提出宝贵意见哦~我们会及时处理!
点击此处反馈


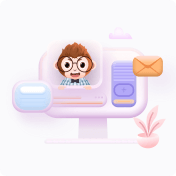