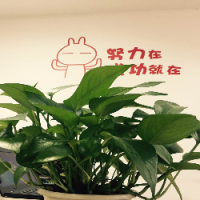

结冰架构
- 粉丝: 945
- 资源: 28万+
最新资源
- 毕业设计JAVAWEB校园订餐系统项目源码
- html css js分页按钮
- Comsol多孔板相场断裂模型:一种高效的数值模拟工具,好的,以下是根据您提供的“comsol多孔板相场断裂模型”提炼出的一个标题: COMSOL多孔板相场模拟与断裂分析模型 此标题涵盖了您提供
- Vcredist运行库【2005、2008、2010、2012、2013、2015-2022】X86+X64集合打包
- 六轴EtherCAT总线伺服涂布收卷机程序:动态测量与同步控制,具备参考值的六个伺服+变频器+编码器方案,六轴EtherCAT总线伺服涂布收卷机高级编程:伺服、变频器与编码器的协同控制及动态测量频率转
- springboot接入InfoSuiteAs
- 命令行界面构建库 :CmdForge
- 电力系统风储协同调频策略的MATLAB仿真模型:基于四机两区系统的频域模型与控制策略优化分析,MATLAB仿真模型:风储联合一次调频在四机两区电力系统的应用与优化,电力系统风储联合一次调频MATLAB
- 【微信小程序源码】笑话
- 「三菱R系列PLC应用:ST、RD77MS定位与触摸屏配方功能实现异地操作及快速通信」,三菱R系列PLC案例详解:高级应用与CClink通信实现机器人远程操作及触摸屏配方功能,三菱R系列PLC案例程序
- 【微信小程序源码】滑动选项卡
- Video_59564296397953.mp3
- 使用c++开发相机的示例CameraDS,引用DirectShow技术
- 贪吃蛇 web版 支持python启动
- 基于NRBO优化算法的Transformer-BiLSTM回归模型Matlab代码:适用于多变量时序预测的电力负荷与光伏功率预测,NRBO-Transformer结合BiLSTM神经网络的时序数据回归
- 【微信小程序源码】京东白条
资源上传下载、课程学习等过程中有任何疑问或建议,欢迎提出宝贵意见哦~我们会及时处理!
点击此处反馈


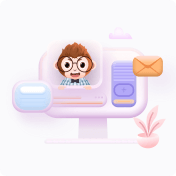