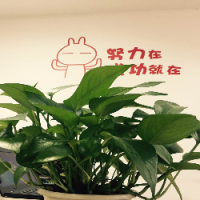

结冰架构
- 粉丝: 914
- 资源: 28万+
最新资源
- 储能变流器PQ并网和VF离网 含学习资料 一、图1、图2、图3为储能变流器PQ控制能量可实现能量双向流动 1储能电压外环,电流内环 2逆变器采用PQ控制,可实现能量双向流动 3仿真实现的内
- 机械设计双工位PCM焊接机sw18非常好的设计图纸100%好用.zip
- 基于java+springboot+vue+mysql的仓库管理系统 源码+数据库+论文(高分毕业设计)
- 最新版Unity Racing Game Starter Kit2
- Comsol仿真-相场法多晶铁电体介电击穿模拟 复现参考文献:Revisiting the Dielectric Breakdown in a Polycrystalline Ferroelectr
- 基于国内某高校校园一卡通系统一个月的运行数据,使用数据分析和建模的方法,挖掘数据中所蕴含的信息,分析学生在校园内的学习生活行为+python项目源码+文档说明
- Comsol仿真-相场法多晶铁电体介电击穿模拟 复现参考文献:Revisiting the Dielectric Breakdown in a Polycrystalline Ferroelectr
- 基于永磁同步电机旋转高频信号注入法零低速无位置控制仿真 1相比高频方波信号注入法,旋转高频信号注入法噪声更小损耗更低 2该模型注入1000Hz旋转高频电压信号到电机中用于产生激励电流,在低速1
- 基于永磁同步电机旋转高频信号注入法零低速无位置控制仿真 1相比高频方波信号注入法,旋转高频信号注入法噪声更小损耗更低 2该模型注入1000Hz旋转高频电压信号到电机中用于产生激励电流,在低速1
- 基于java+springboot+vue+mysql的校园二手物品交易平台 源码+数据库+论文(高分毕业设计)
- 中国生态功能保护区shp数据
- html+css+js网页设计 美食 好厨艺西餐美食企业网站模板6个页面
- STM32F407单片机上使用HAL库实现can总线的接收和发送
- STM32F767 UCOS开发手册-V1.0.zip
- 光伏蓄电池单相并网模型 带参考文件,模型说明文件 模型内容: 1.光伏+MPPT+boost升压电路+桥式逆变 2.电池模型+电池控制器+直流母线控制 3.稳定交流负载+功率控制器+pwm调制 仿真
- 一个加载UCOSII嵌入式操作系统的STM32项目模板.zip
资源上传下载、课程学习等过程中有任何疑问或建议,欢迎提出宝贵意见哦~我们会及时处理!
点击此处反馈


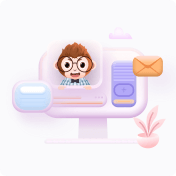