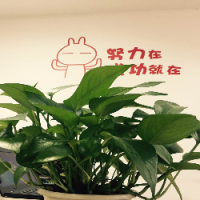

结冰架构
- 粉丝: 917
- 资源: 28万+
最新资源
- 基于java+springboot+vue+mysql的粮仓管理系统设计与实现.docx
- 基于java+springboot+vue+mysql的美发管理系统设计与实现.docx
- 基于java+springboot+vue+mysql的美术馆管理系统设计与实现.docx
- 2023保健品行业洞察报告
- 基于java+springboot+vue+mysql的民宿管理系统设计与实现.docx
- 基于java+springboot+vue+mysql的培训机构管理系统设计与实现.docx
- 基于java+springboot+vue+mysql的民航网上订票系统设计与实现.docx
- 基于java+springboot+vue+mysql的入校申报审批系统设计与实现.docx
- 基于java+springboot+vue+mysql的汽车租赁系统设计与实现.docx
- 基于java+springboot+vue+mysql的商业辅助决策系统设计与实现.docx
- 基于java+springboot+vue+mysql的水产养殖系统设计与实现.docx
- 基于java+springboot+vue+mysql的社区网格化管理平台设计与实现.docx
- 基于java+springboot+vue+mysql的社区医疗服务系统设计与实现.docx
- 基于java+springboot+vue+mysql的玩具租赁系统设计与实现.docx
- 基于java+springboot+vue+mysql的闲置图书分享平台设计与实现.docx
- 基于java+springboot+vue+mysql的西安旅游系统设计与实现.docx
资源上传下载、课程学习等过程中有任何疑问或建议,欢迎提出宝贵意见哦~我们会及时处理!
点击此处反馈


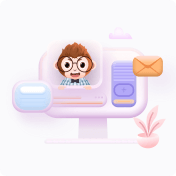