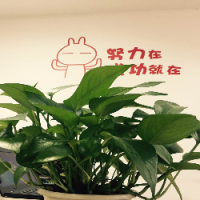

结冰架构
- 粉丝: 916
- 资源: 28万+
最新资源
- Screenshot_2025-01-07-12-49-36-964_net.csdn.csdnplus.jpg
- gbase8s死锁模拟
- 基于Java Web的电影在线推荐系统设计与实现-基于用户协同过滤的个性化推荐
- 【2025新软件】+文件批量下载器.exe+【批量下载神器】+【Windows必备】
- 435asp.net美容院管理系统毕业课程源码设计+论文资料+开题报告+任务书
- 1渗透测试流程.pdf
- 仅供自己使用,请勿下载,谢谢
- python框架的课堂投票系统(全套毕业文档+源代码).zip
- 仅供自己使用,请勿下载,谢谢
- 评估过期处理办法.docx
- 品牌设计领域权威书籍指南: 提升品牌创建与CI设计理念
- 436大神C#基于winform图书管理系统毕业课程源码设计
- PhpStudy教程.pdf
- burpSuite的安装和使用.pdf
- http协议那点儿事.pdf
- 毕业设计-java-springboot+vue二手车估值与销售平台实现源码(项目源码+毕业全套文档).zip
资源上传下载、课程学习等过程中有任何疑问或建议,欢迎提出宝贵意见哦~我们会及时处理!
点击此处反馈


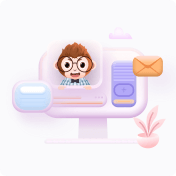