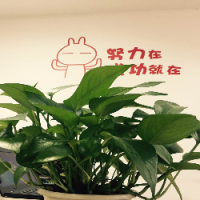

结冰架构
- 粉丝: 917
- 资源: 28万+
最新资源
- 信捷XD系列4轴标准程序,包含轴回零,相对定位,绝对定位,手,电机参数计算,整个程序的模块都有,程序框架符合广大编程人员思维,只要弄明白这个程序,一般的项目都不会无从下手,参照这个,做项目不再难,拿着
- SIEMENS 西门子1200走总线FB284控制3台V90伺服和相机调整角度,DP通讯控制FANUC机器人,程序简单明了,适合初学者入门,博途FB284功能块入门使用手册 PLC程序带完整的注解和
- matlab模型IEEE33节点配电网,附参数,可接分布式电源,电压可调
- 西门子1214 PID 通信模板 西门子PLC 1214和多台G120西门子变频器Modbud RTU通讯 (1)西门子触摸屏; (2)变频器参数 Modbus通讯报文详细讲解; (3)PID自写
- 西门子200Smart加维纶触摸屏程序画面程序案例,项目内容为某制造企业疫苗车间控制系统,报告配液工艺,发酵工艺,纯化工艺及CIP清洗工艺控制 程序结构清晰,控制功能较多,包含模拟量,泵,PID,U
- 配电网故障重构matlab 二阶锥 编程方法:matlab+yalmip(cplex为求解器) 基本内容:以33节点为研究对象,编制配电网故障重构模型,采用图论知识保证配电网的连通性和辐射性,以网损和
- 基于YALMIP的微电网优化调度模型 学习使用非常合适 考虑蓄电池,市场购电电约束,功率平衡约束,以总费用最低为目标函数,适合新手学习参考 电网程序matlab,有参考文档 标价即卖价,不议价,不
- 电力系统调度 源荷不确定性matlab 程序语言:matlab+yalmip(可适用cplex或者gurobi作为求解器) 内容:参照考虑源荷两侧不确定性的含风电的低碳调度,引入模糊机会约束,程序包括
- 混凝土多边形骨料二维建模,多边形的边数随机的,可改变骨料面积分数和界面国过渡区厚度,模型的大小也可改变,Comsol with Matlab生成的,得到.mph文件,Comsol直接可以打开,用于后续
- Buck电路设计,开关电源学习工具,可以根据需求修改电路的规格参数,计算书自动生成计算结果,可以进行开关管及无源器件的选型,损耗及温升计算 附赠两个电路优化计算书,可以对比不同电压或者频率下Buck
- MATLAB代码:计及电转气协同的含碳捕集与垃圾焚烧电厂优化调度 关键词:碳捕集 电厂 需求响应 优化调度 电转气协同调度 参考文档:《计及电转气协同的含碳捕集与垃圾焚烧电厂优化调度》完全复现
- MATLAB代码:基于双层优化的电动汽车日前-实时两阶段市场竞标 关键词:日前-实时市场竞标 电动汽车 双层优化 编程语言:MATLAB平台 参考文献:店主自编参考文献,可联系我查看 内容简介:
- PCS7 WINCC报表 1.不需要第三方任何插件实现 2.采用数据库方式实现快速生成WINCC报表 3.提供脚本源码程序 4.可移植,也可以导出来生成EXCEL文件
- 基于Copula理论与K-means的考虑风光出力相关性的风光场景生成与削减 摘要:代码主要做的是风光场景生成的内容,与目前大部分的基于蒙特卡洛或者拉丁超立方等方法不同,代码在场景生成的过程中考虑了风
- 单管共射负反馈放大电路,晶体管放大电路,multisim仿真每一步都有 (会给原文件,有参数不同的双击就可以改) 包含静态工作点测量,调试(测量值和计算值都有) (包括静态工作点的波形,以及关于波形的
- STM32F405_RAW-stm32cubemx
资源上传下载、课程学习等过程中有任何疑问或建议,欢迎提出宝贵意见哦~我们会及时处理!
点击此处反馈


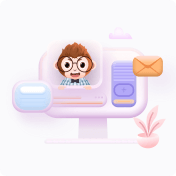