在冶金连铸电气控制中,PLC(Programmable Logic Controller,可编程逻辑控制器)控制系统的设计与分析是一个重要的研究方向。冶金连铸是一个复杂的过程,涉及到多个环节的精确控制,包括氩气流量、水流量、二冷水系统、大包回转台控制、拉矫机控制以及自动出坯系统等。通过实现这些环节的自动化控制,可以显著提高冶金生产的效率和质量。 PLC控制系统在冶金连铸中的调节功能至关重要。调节功能要求对氩气流量、水流量等关键参数进行精确控制,以保持稳定的数值。在自动化控制系统的程序设计中,西门子PLC被用来代替智能仪表,实现手动和自动调节的切换。用户只需手动输入特定的参数,系统即可自动进行控制。 冶金连铸电气控制系统的设计包括多个步骤,其中拉矫机控制功能需要按照特定的步骤完成。第一步是启动拉矫机并控制其运行速度和运行形式,无论是正转还是反转。在自动控制模式下,系统会根据子程序来控制拉矫机的运行。第二步是对发电机的数据进行判断和识别,通过调速装置的输出反馈值可以直接显示拉矫机的拉速。最后一步是对拉矫机的调速装置的参数进行设定,并对其运行过程进行故障诊断,以显示其运行状况。 二冷水系统中的调节也是一个重要组成部分。根据铜种类型的不同,二冷水配置制度也存在较大的差异。在每流PLC控制中,二冷水的调节可以通过监控站的应用来实现自动化配水工作,并能够在画面上对自动、手动以及全自动这几种配水方式进行设置。在实际操作中,需要弹出调节画面,并通过全自动方式调节水表参数。二冷水的调节需要通过PLC的应用对调节阀进行设定,以实现对现场气动调节阀的控制功能。 大包回转台控制涉及到两个钢包的承载和浇筑过程中的状态切换。由于回转台在旋转过程中承受的压力较大,因此需要精确控制旋转速度和时间,以避免波动的产生。旋转速度和时间需要合理控制,以提高旋转效率,减少旋转时间。大包回转台的旋转角度也需要严格精确控制,通常采用脉冲编码器来完成检测。在脉冲编码器的检测过程中,需要在大包回转台旁安装两个同步的开关,用于对脉冲进行清零并完成检测。 拉矫自动控制系统关注的是铸机的拉速调节。借助铸机的控制箱电阻电位器来控制,PLC控制系统会持续发送模拟信号,并通过通讯网络实现对变频器输出拉速的控制。通过对制造工艺和模拟信号的快速计算,可以实现振频与拉速的匹配,进而降低拉矫电机的负荷量。在铸坯切割前,输送辊道会应用西门子变频调速装置,并在通信网络中实现参数的连接和共享,保持铸坯切割前的距离和拉矫机的输送速度的一致性。 自动出坯系统由移坯车编码器、冷床限位、移坯车和翻转冷床等部分组成。在完成铸坯切割后,铸坯会通过输送辊道运输到长辊平移冷床上。当监测到坯子信号时,相关信息会通过PLC进行传输,并根据累计信号进行操作,如停止输送辊道、启动移坯车、移动坯车并进行位置控制等。红外镜头对热坯的监测会导致PLC对冷床启动命令的发出,完成导板上热坯的运输。当冷床架上冷却后的坯子达到一定数量时,它们将被电磁吸盘吊走。 在整个冶金连铸生产过程中,PLC控制系统的设计和实施是提高生产效率、保证产品质量的关键。通过实现自动化和智能化控制,冶金企业可以在激烈的市场竞争中获得更好的发展。此外,对PLC控制系统的研究和应用还能促进冶金行业的技术进步,为冶金行业的未来发展方向提供参考。
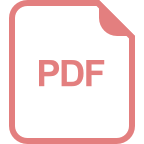
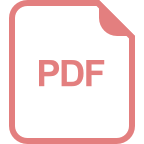
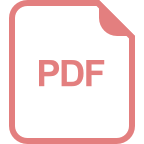
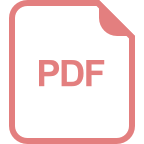
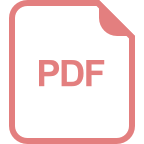
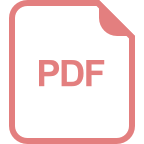
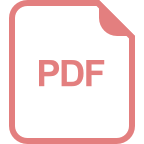
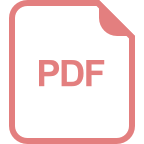
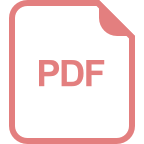
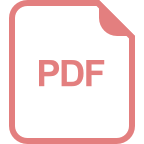
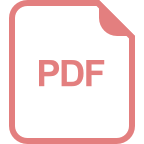
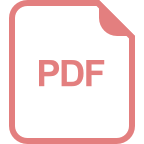
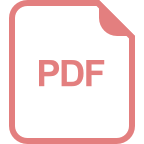
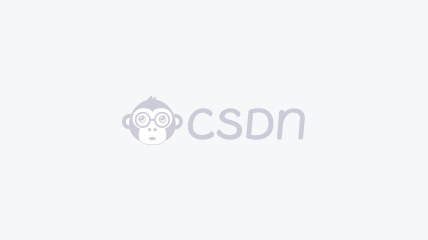
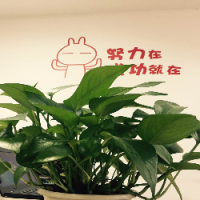

- 粉丝: 902
- 资源: 28万+
我的内容管理 展开
我的资源 快来上传第一个资源
我的收益
登录查看自己的收益我的积分 登录查看自己的积分
我的C币 登录后查看C币余额
我的收藏
我的下载
下载帮助

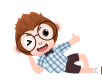
最新资源

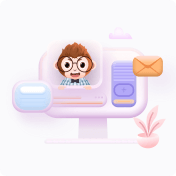
