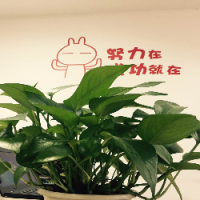

结冰架构
- 粉丝: 913
- 资源: 28万+
最新资源
- 车用驱动电机原理与控制基础-P140公式(6-57)~(6-58)
- MATLAB编程入门指南:环境搭建、基础语法及实用功能
- Oracle SQL Developer Data Modeler:数据建模与模型文档化及分享的最佳实践
- 使用 Python 为新年创建倒数计时器
- python语言huochepiao爬虫程序代码QZQ1.txt
- 2025 年新年快乐 -使用 HTML、CSS 和 JavaScript 设计新年贺卡
- Java毕设项目:基于spring+mybatis+maven+mysql实现的小区停车管理系统【含源码+数据库+毕业论文】
- Java毕设项目:基于spring+mybatis+maven+mysql实现的校园车辆管理系统【含源码+数据库+开题报告+毕业论文】
- 如何使用 Python 创建倒数计时器?
- Java毕设项目:基于spring+mybatis+maven+mysql实现的学生公寓管理系统【含源码+数据库+答辩PPT+毕业论文】
- 电子产品IM端子自动组装机sw14全套技术资料100%好用.zip
- Java毕设项目:基于spring+mybatis+maven+mysql实现的电动车租赁管理系统【含源码+数据库+毕业论文】
- 基于java的酒店客房管理系统的开题报告.docx
- 基于java的酒店预约及管理系统的开题报告.docx
- 电芯铝塑膜冲坑机sw14全套技术资料100%好用.zip
- 基于java的旅游攻略网站的开题报告.docx
资源上传下载、课程学习等过程中有任何疑问或建议,欢迎提出宝贵意见哦~我们会及时处理!
点击此处反馈


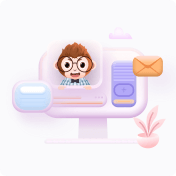