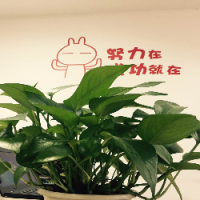

结冰架构
- 粉丝: 907
- 资源: 28万+
最新资源
- (已测试)WordPress企业主题:企业一号 V 1.2.2商业版
- 德普微一级代理 DP3246 QSOP-24/QFN-24 16通道恒流源驱动IC
- SHT30温湿度传感器STM32 IIC程序源码
- 基于java+ssm+mysql+微信小程序的微信阅读小程序 源码+数据库(高分毕业设计).zip
- 基于java+ssm+mysql+微信小程序的图书馆座位再利用系统 源码+数据库(高分毕业设计).zip
- 经管类国自然、国社科立项名单+部分标书1991-2024年-最新出炉.zip
- 德普微一级代理 DP028N12BGN/DP028N12PGN TO-263/TO-220 DPMOS N-MOSFET 120V 180A 2.5mΩ
- 基于java+ssm+mysql+微信小程序的项目申报小程序 源码+数据库+论文(高分毕业设计).zip
- 德普微一级代理 DP900N10DTL TO-252 DPMOS N-MOSFET 100V 16A 83mΩ
- 基于nodejs+mysql+微信小程序的校园兼职系统 源码+数据库(高分毕业设计).zip
- 国密算法sm4加密解密
- 教学创新大赛实施报告图复刻-可编辑修改-2024年最新出炉.zip
- html+css+js网页设计 美食 桂林美食4个页面
- 基于Spring boot+Mybatis+Mysql的登录界面
- 麦克纳姆轮agv小车sw17可编辑全套技术资料100%好用.zip
- 全国教学创新大赛、青教赛、教学能力比赛资料大全-最新出炉.zip
资源上传下载、课程学习等过程中有任何疑问或建议,欢迎提出宝贵意见哦~我们会及时处理!
点击此处反馈


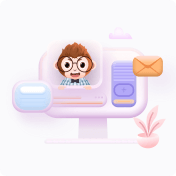