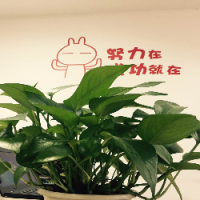

结冰架构
- 粉丝: 914
- 资源: 28万+
最新资源
- 基于PHP的FeelDesk工单管理系统开源版设计源码
- 基于Antv-X6的组态编辑器与可视化设计源码
- factoryio2.5工厂流水线仿真程序,期末专周可用,多个场景可以咨询 使用简单的梯形图与SCL语言编写,通俗易懂,起到抛砖引玉的作用,比较适合有动手能力的入门初学者 软件环境: 1、西门子编程
- 基于公有云平台的OpenIoT项目设计源码
- 基于微信小程序文件系统的MxLocalBase本地数据库设计源码
- 基于C语言的2023级寒假实践打地鼠游戏设计源码
- 基于matlab的孔入式静压轴承程序,进油孔数为4个,采用有限差分计算轴承油膜厚度及油膜压力 程序已调通,可直接运行
- 控制电机-感应电动机转差型矢量控制伺服模型系统 仿真模型+实验报告(内附实验参数,仿真波形等) 注意:matlab版本需在2016a以下,否则可能打不开
- 控制电机-正弦波永磁同步电动机矢量控制系统仿真 仿真模型+实验报告(内附实验参数,仿真波形等) 注意:matlab版本需在2016a以下,否则可能打不开
- 基于扰动观测器的永磁同步电机(PMSM)模型预测控制(MPC)仿真 速度外环基于模型预测控制、电流内环基于无差拿控制搭建,控制效果理想,模块程序设计通俗易通
- 基于Laravel的简化Smarty模板引擎设计源码
- NSGA2遗传算法多目标优化 三维视图 寻优多个函数(函数类型见图二类型),出图为三维红色为帕列托(图一), 带最终结果图(图三)
- 基于graqhql/mongodb/nodejs/nuxtjs的Vue跨世代实时在线文档编辑系统设计源码
- 基于Java的用户线程模型设计源码
- 基于Rust Axum框架的Web后端项目设计与源码实践
- 基于HTML、CSS和JavaScript的eui后台UI框架设计源码预览版账号密码提供
资源上传下载、课程学习等过程中有任何疑问或建议,欢迎提出宝贵意见哦~我们会及时处理!
点击此处反馈


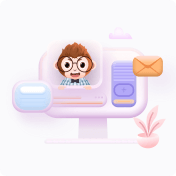