没有合适的资源?快使用搜索试试~ 我知道了~
资源推荐
资源详情
资源评论
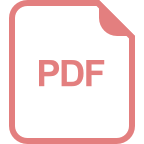
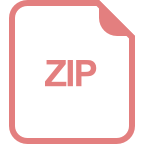
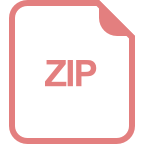
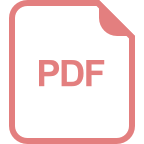
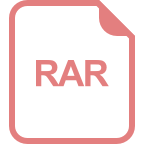
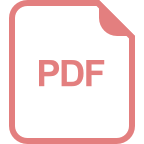
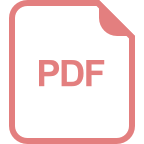
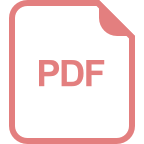
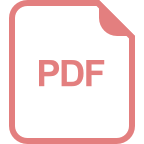
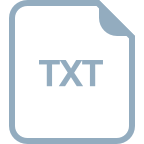
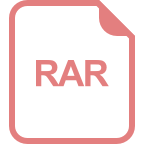
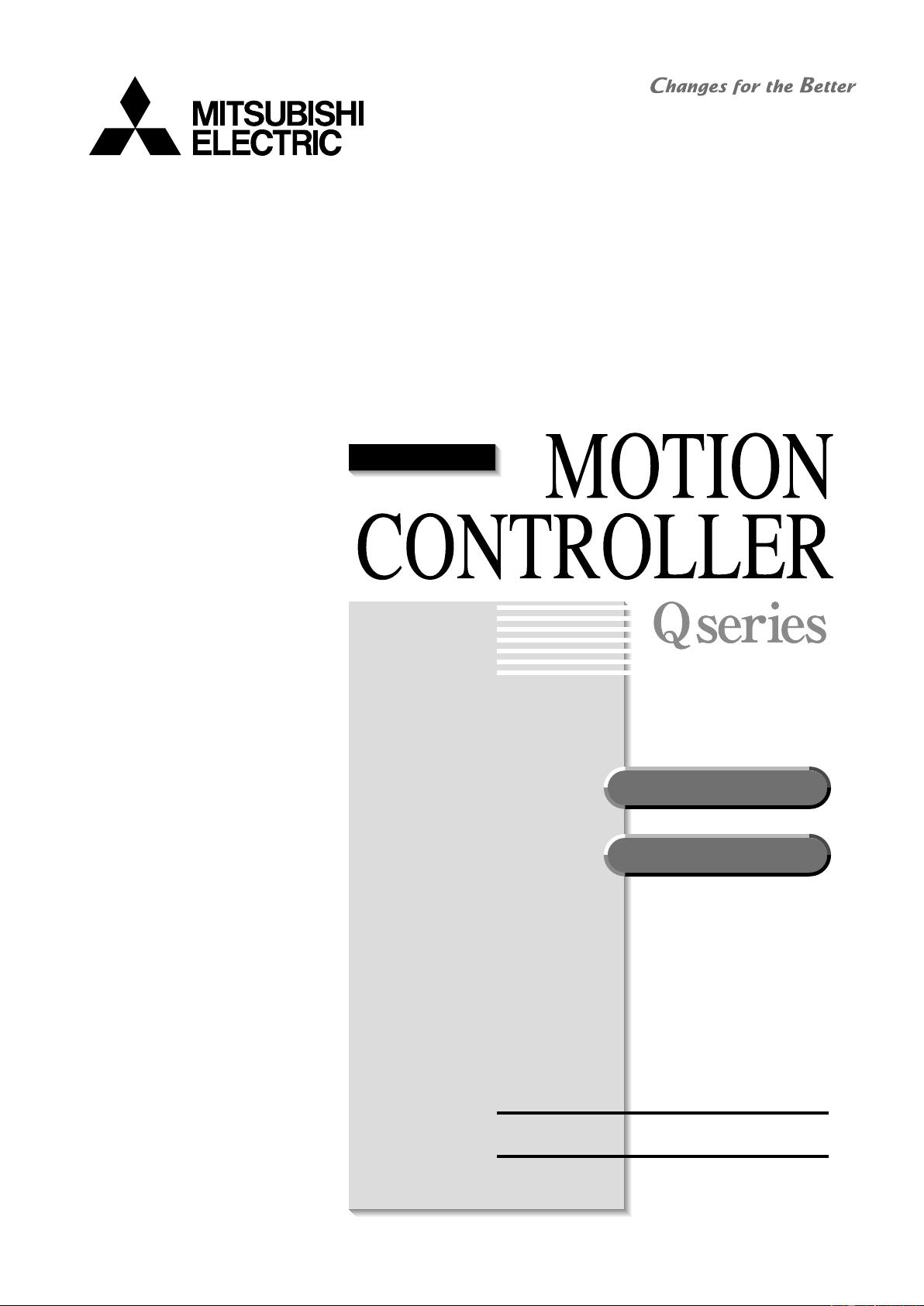
IB(NA)-0300115-A(0602)MEE
P
Q
MOTION CONTROLLER Qseries (SV43) Programming Manual (Q173HCPU/Q172HCPU)
MOTION CONTROLLERS
Programming Manual
MODEL
MODEL
CODE
Q173H-P-SV43-E
1XB915
IB(NA)-0300115-A(0602)MEE
When exported from Japan, this manual does not require application to the
Ministry of Economy, Trade and Industry for service transaction permission.
Specifications subject to change without notice.
Q173HCPU
Q172HCPU
SV43
MOTION CONTROLLER Qseries
SV43 Programming Manual
(Q173HCPU/Q172HCPU)
HEAD OFFICE : TOKYO BUILDING, 2-7-3 MARUNOUCHI, CHIYODA-KU, TOKYO 100-8310, JAPAN
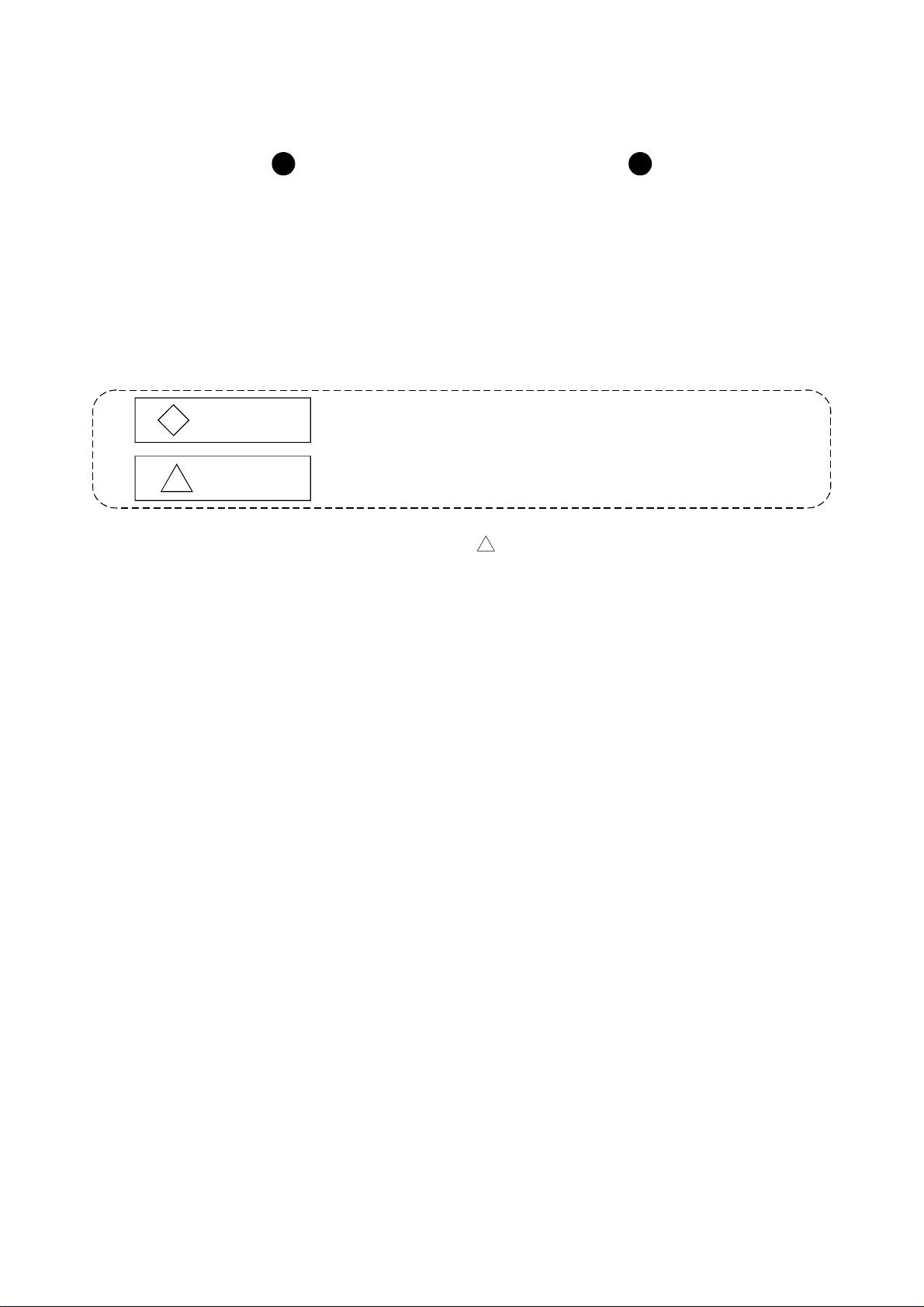
A - 1
SAFETY PRECAUTIONS
(Read these precautions before using.)
When using this equipment, thoroughly read this manual and the associated manuals introduced in this
manual. Also pay careful attention to safety and handle the module properly.
These precautions apply only to this equipment. Refer to the Q173HCPU/Q172HCPU Users manual for a
description of the Motion controller safety precautions.
These SAFETY PRECAUTIONS classify the safety precautions into two categories: "DANGER" and
"CAUTION".
!
DANGER
CAUTION
!
Indicates that incorrect handling may cause hazardous conditions,
resulting in death or severe injury.
Indicates that incorrect handling may cause hazardous conditions,
resulting in medium or slight personal injury or physical damage.
Depending on circumstances, procedures indicated by
!
CAUTION may also be linked to serious
results.
In any case, it is important to follow the directions for usage.
Store this manual in a safe place so that you can take it out and read it whenever necessary. Always
forward it to the end user.
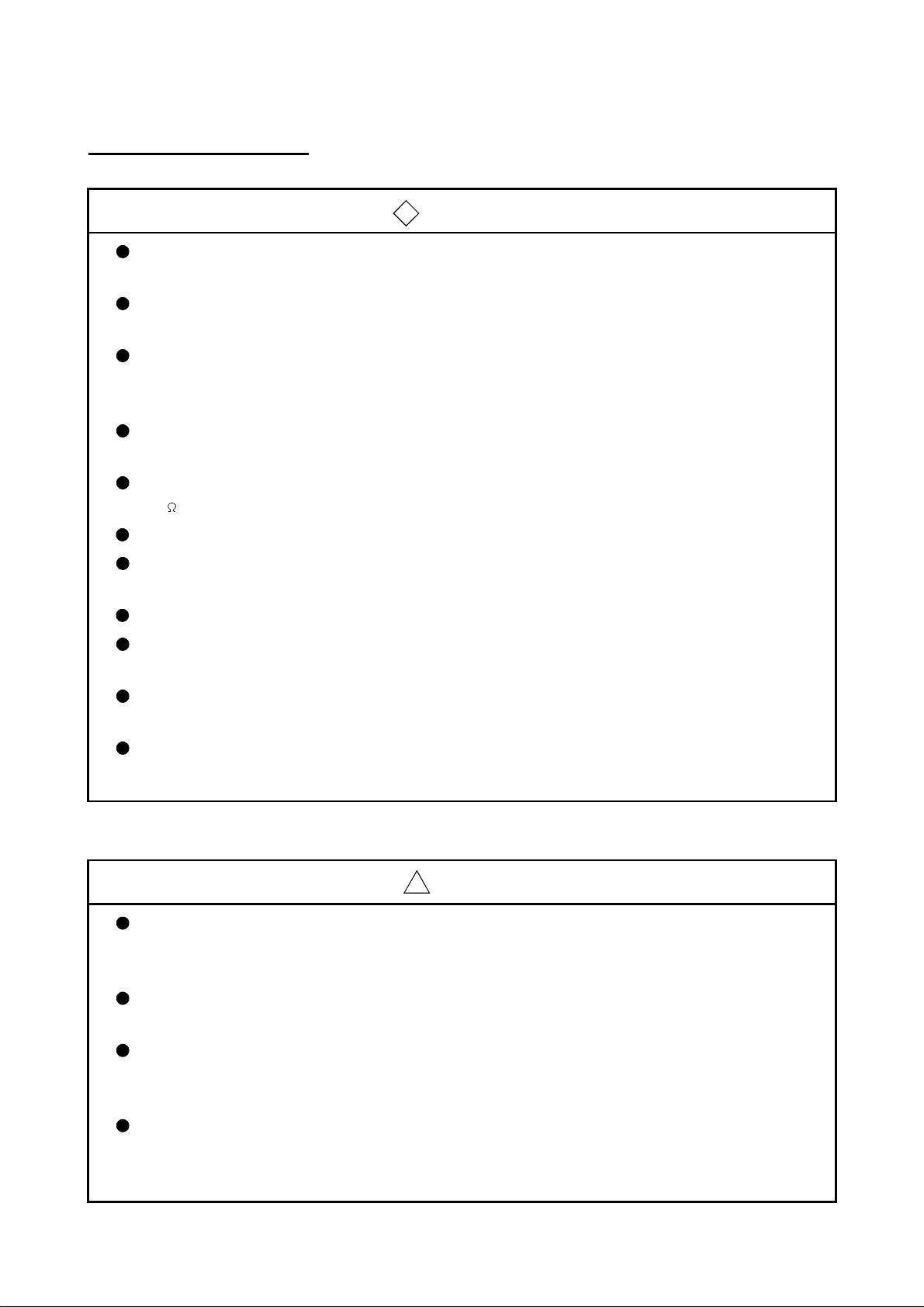
A - 2
For Safe Operations
1. Prevention of electric shocks
!
DANGER
Never open the front case or terminal covers while the power is ON or the unit is running, as
this may lead to electric shocks.
Never run the unit with the front case or terminal cover removed. The high voltage terminal and
charged sections will be exposed and may lead to electric shocks.
Never open the front case or terminal cover at times other than wiring work or periodic
inspections even if the power is OFF. The insides of the Motion controller and servo amplifier
are charged and may lead to electric shocks.
When performing wiring work or inspections, turn the power OFF, wait at least ten minutes, and
then check the voltage with a tester, etc.. Failing to do so may lead to electric shocks.
Be sure to ground the Motion controller, servo amplifier and servomotor. (Ground resistance :
100
or less) Do not ground commonly with other devices.
The wiring work and inspections must be done by a qualified technician.
Wire the units after installing the Motion controller, servo amplifier and servomotor. Failing to do
so may lead to electric shocks or damage.
Never operate the switches with wet hands, as this may lead to electric shocks.
Do not damage, apply excessive stress, place heavy things on or sandwich the cables, as this
may lead to electric shocks.
Do not touch the Motion controller, servo amplifier or servomotor terminal blocks while the
power is ON, as this may lead to electric shocks.
Do not touch the built-in power supply, built-in grounding or signal wires of the Motion controller
and servo amplifier, as this may lead to electric shocks.
2. For fire prevention
!
CAUTION
Install the Motion controller, servo amplifier, servomotor and regenerative resistor on
inflammable material. Direct installation on flammable material or near flammable material may
lead to fire.
If a fault occurs in the Motion controller or servo amplifier, shut the power OFF at the servo
amplifier’s power source. If a large current continues to flow, fire may occur.
When using a regenerative resistor, shut the power OFF with an error signal. The regenerative
resistor may abnormally overheat due to a fault in the regenerative transistor, etc., and may
lead to fire.
Always take heat measures such as flame proofing for the inside of the control panel where
the servo amplifier or regenerative resistor is installed and for the wires used. Failing to do so
may lead to fire.
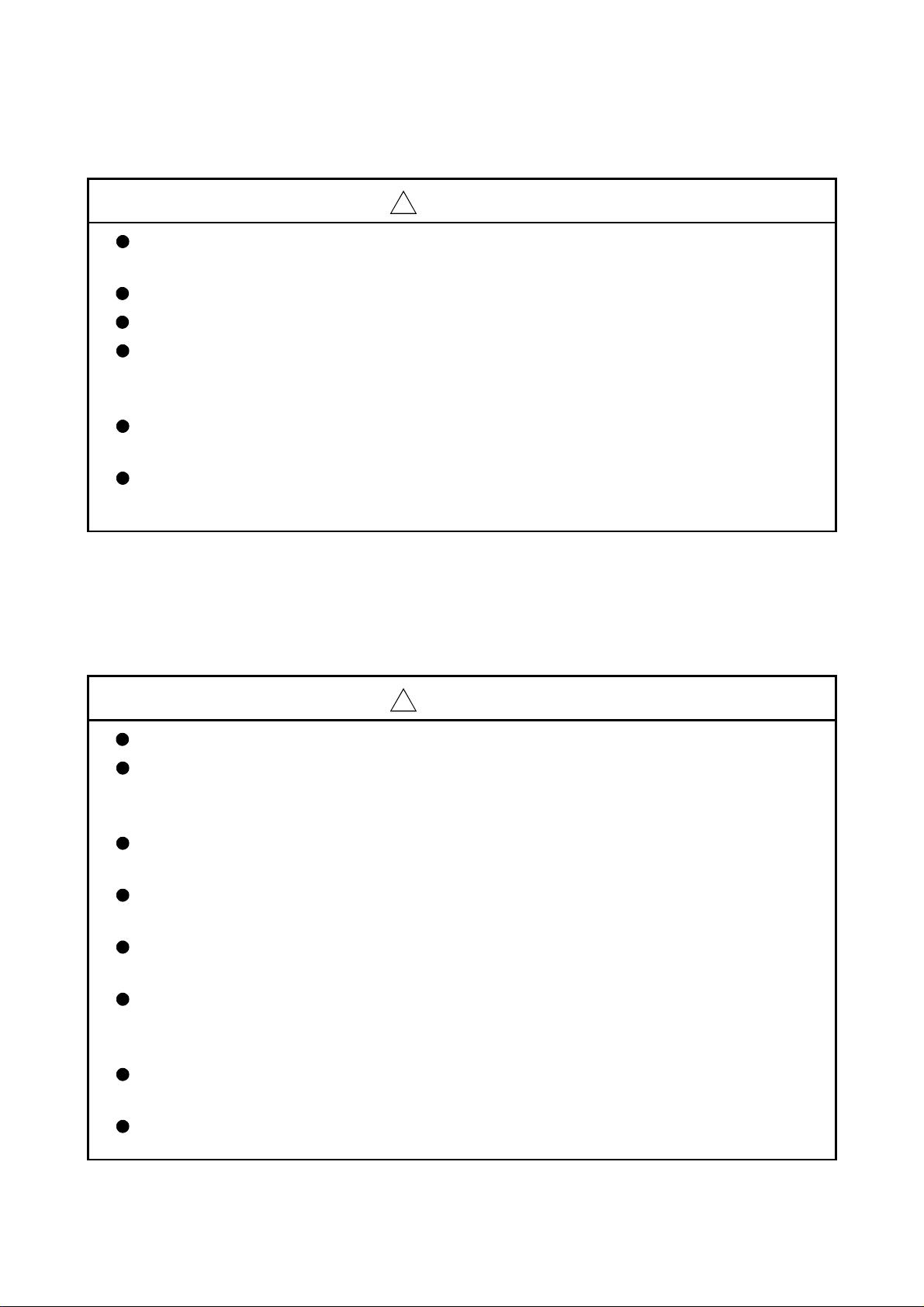
A - 3
3. For injury prevention
!
CAUTION
Do not apply a voltage other than that specified in the instruction manual on any terminal.
Doing so may lead to destruction or damage.
Do not mistake the terminal connections, as this may lead to destruction or damage.
Do not mistake the polarity ( + / - ), as this may lead to destruction or damage.
Do not touch the servo amplifier's heat radiating fins, regenerative resistor and servomotor, etc.,
while the power is ON and for a short time after the power is turned OFF. In this timing, these
parts become very hot and may lead to burns.
Always turn the power OFF before touching the servomotor shaft or coupled machines, as
these parts may lead to injuries.
Do not go near the machine during test operations or during operations such as teaching.
Doing so may lead to injuries.
4. Various precautions
Strictly observe the following precautions.
Mistaken handling of the unit may lead to faults, injuries or electric shocks.
(1) System structure
!
CAUTION
Always install a leakage breaker on the Motion controller and servo amplifier power source.
If installation of an electromagnetic contactor for power shut off during an error, etc., is specified
in the instruction manual for the servo amplifier, etc., always install the electromagnetic
contactor.
Install the emergency stop circuit externally so that the operation can be stopped immediately
and the power shut off.
Use the Motion controller, servo amplifier, servomotor and regenerative resistor with the combi-
nations listed in the instruction manual. Other combinations may lead to fire or faults.
If safety standards (ex., robot safety rules, etc.,) apply to the system using the Motion controller,
servo amplifier and servomotor, make sure that the safety standards are satisfied.
Construct a safety circuit externally of the Motion controller or servo amplifier if the abnormal
operation of the Motion controller or servo amplifier differ from the safety directive operation in
the system.
In systems where coasting of the servomotor will be a problem during the forced stop,
emergency stop, servo OFF or power supply OFF, use dynamic brakes.
Make sure that the system considers the coasting amount even when using dynamic brakes.
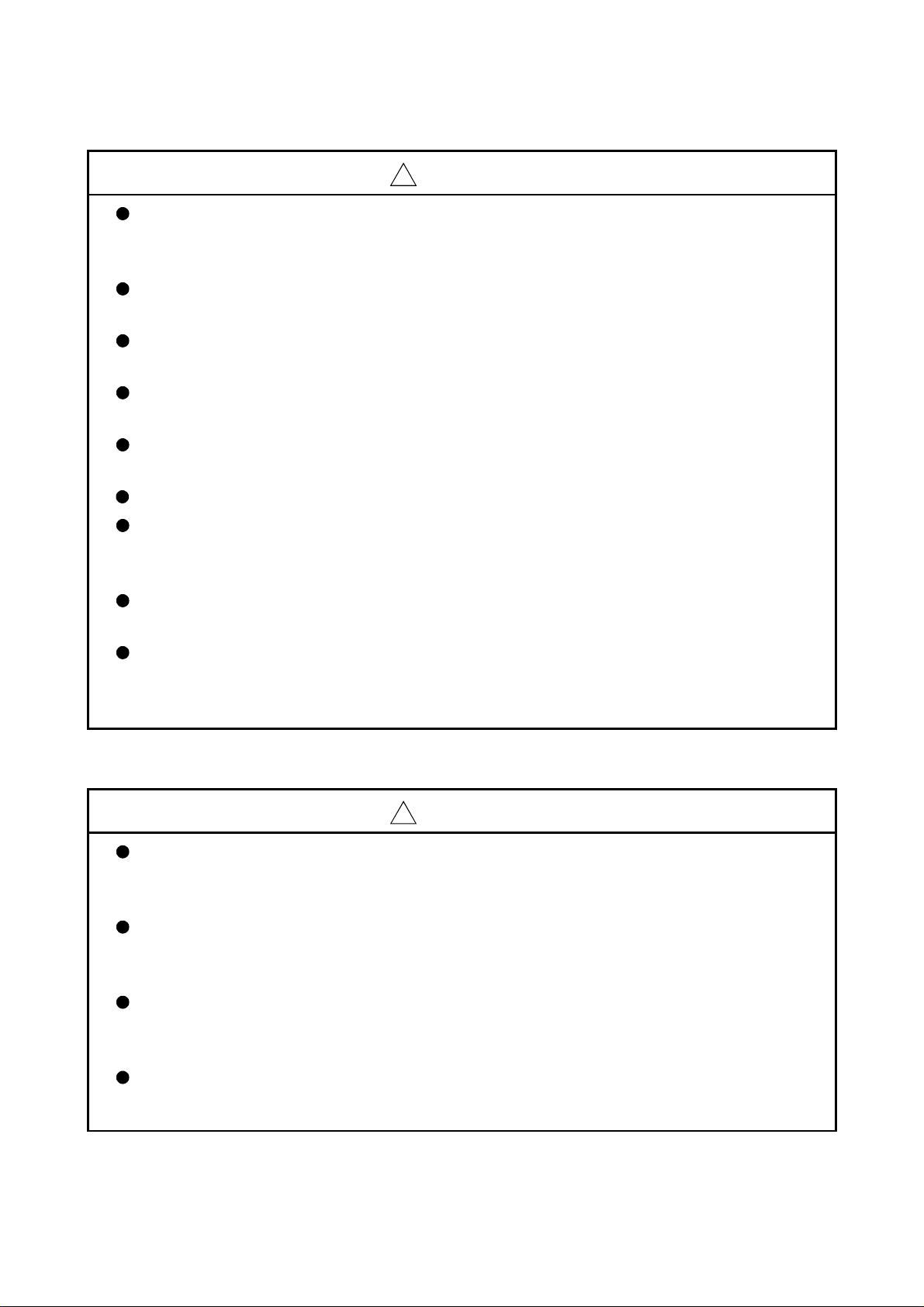
A - 4
!
CAUTION
In systems where perpendicular shaft dropping may be a problem during the forced stop,
emergency stop, servo OFF or power supply OFF, use both dynamic brakes and
electromagnetic brakes.
The dynamic brakes must be used only on errors that cause the forced stop, emergency stop,
or servo OFF. These brakes must not be used for normal braking.
The brakes (electromagnetic brakes) assembled into the servomotor are for holding
applications, and must not be used for normal braking.
The system must have a mechanical allowance so that the machine itself can stop even if the
stroke limits switch is passed through at the max. speed.
Use wires and cables that have a wire diameter, heat resistance and bending resistance
compatible with the system.
Use wires and cables within the length of the range described in the instruction manual.
The ratings and characteristics of the parts (other than Motion controller, servo amplifier and
servomotor) used in a system must be compatible with the Motion controller, servo amplifier
and servomotor.
Install a cover on the shaft so that the rotary parts of the servomotor are not touched during
operation.
There may be some cases where holding by the electromagnetic brakes is not possible due to
the life or mechanical structure (when the ball screw and servomotor are connected with a
timing belt, etc.). Install a stopping device to ensure safety on the machine side.
(2) Parameter settings and programming
!
CAUTION
Set the parameter values to those that are compatible with the Motion controller, servo amplifier,
servomotor and regenerative resistor model and the system application. The protective functions
may not function if the settings are incorrect.
The regenerative resistor model and capacity parameters must be set to values that conform to
the operation mode, servo amplifier and servo power supply module. The protective functions
may not function if the settings are incorrect.
Set the mechanical brake output and dynamic brake output validity parameters to values that
are compatible with the system application. The protective functions may not function if the
settings are incorrect.
Set the stroke limit input validity parameter to a value that is compatible with the system
application. The protective functions may not function if the setting is incorrect.
剩余523页未读,继续阅读
资源评论
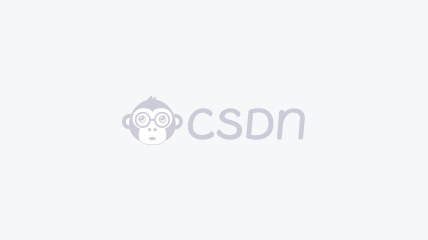
- 姜工Engineer2017-10-20英文版的,
- cnceng2013-12-18一直想了解三菱运动控制器SV43的使用方法,苦于一直没找到资料.非常感谢BH7LRF!

BH7LRF
- 粉丝: 5
- 资源: 11
上传资源 快速赚钱
我的内容管理 展开
我的资源 快来上传第一个资源
我的收益
登录查看自己的收益我的积分 登录查看自己的积分
我的C币 登录后查看C币余额
我的收藏
我的下载
下载帮助

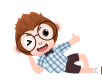
最新资源
- 【创新无忧】基于多元宇宙优化算法MVO优化广义神经网络GRNN实现光伏预测附matlab代码.rar
- 【创新无忧】基于白鲨优化算法WSO优化广义神经网络GRNN实现光伏预测附matlab代码.rar
- 【创新无忧】基于多元宇宙优化算法MVO优化广义神经网络GRNN实现数据回归预测附matlab代码.rar
- 【创新无忧】基于多元宇宙优化算法MVO优化极限学习机ELM实现乳腺肿瘤诊断附matlab代码.rar
- 【创新无忧】基于多元宇宙优化算法MVO优化极限学习机KELM实现故障诊断附matlab代码.rar
- 【创新无忧】基于飞蛾扑火优化算法MFO优化广义神经网络GRNN实现电机故障诊断附matlab代码.rar
- 【创新无忧】基于多元宇宙优化算法MVO优化相关向量机RVM实现数据多输入单输出回归预测附matlab代码.rar
- 【创新无忧】基于多元宇宙优化算法MVO优化相关向量机RVM实现北半球光伏数据预测附matlab代码.rar
- 【创新无忧】基于飞蛾扑火优化算法MFO优化广义神经网络GRNN实现光伏预测附matlab代码.rar
- 【创新无忧】基于飞蛾扑火优化算法MFO优化极限学习机ELM实现乳腺肿瘤诊断附matlab代码.rar
- 【创新无忧】基于飞蛾扑火优化算法MFO优化广义神经网络GRNN实现数据回归预测附matlab代码.rar
- 【创新无忧】基于飞蛾扑火优化算法MFO优化相关向量机RVM实现数据多输入单输出回归预测附matlab代码.rar
- 【创新无忧】基于飞蛾扑火优化算法MFO优化相关向量机RVM实现北半球光伏数据预测附matlab代码.rar
- 【创新无忧】基于飞蛾扑火优化算法MFO优化极限学习机KELM实现故障诊断附matlab代码.rar
- 【创新无忧】基于非洲秃鹫优化算法AVOA优化广义神经网络GRNN实现电机故障诊断附matlab代码.rar
- 【创新无忧】基于非洲秃鹫优化算法AVOA优化广义神经网络GRNN实现光伏预测附matlab代码.rar
资源上传下载、课程学习等过程中有任何疑问或建议,欢迎提出宝贵意见哦~我们会及时处理!
点击此处反馈


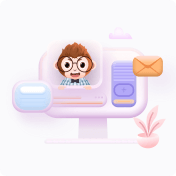
安全验证
文档复制为VIP权益,开通VIP直接复制
