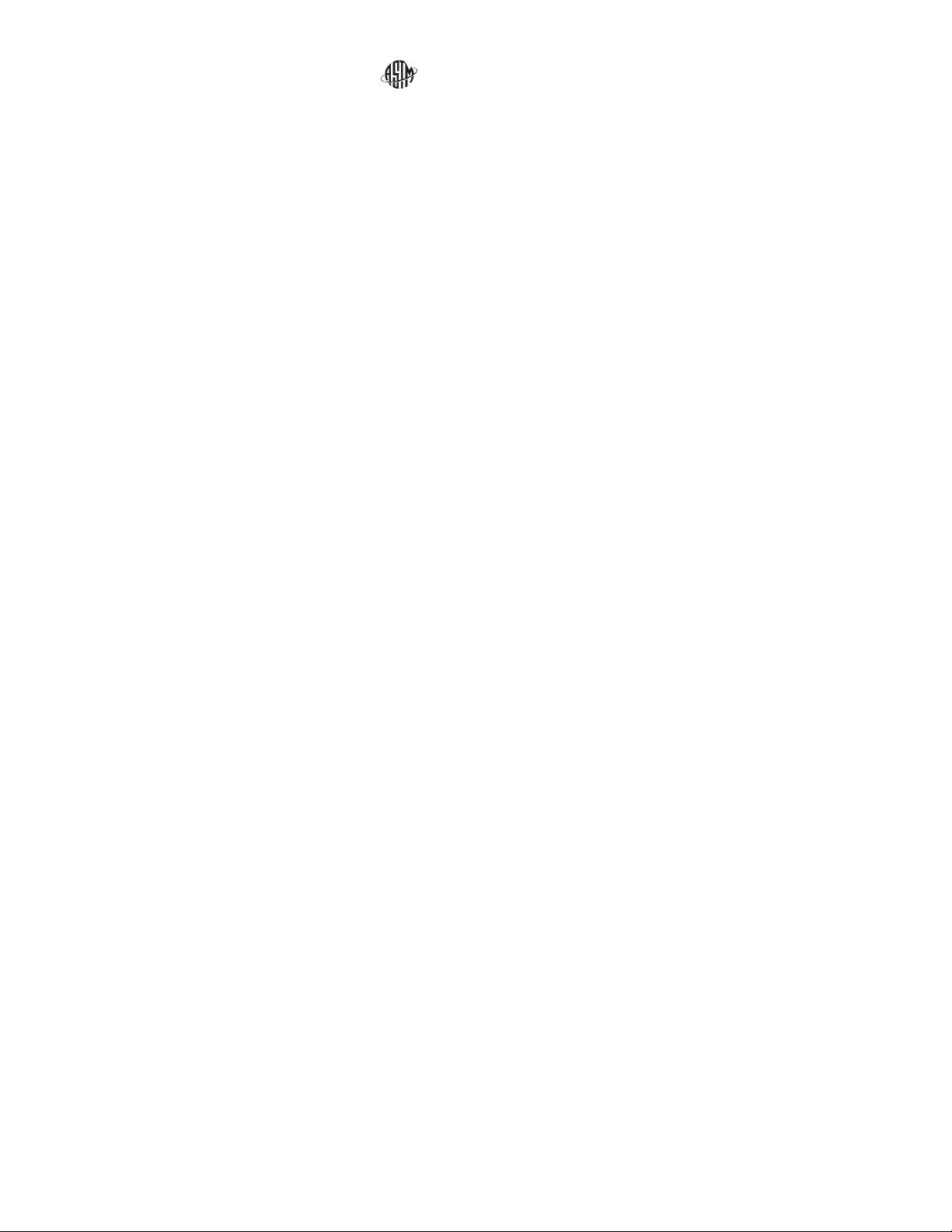
A 744/A 744M Specification for Castings, Iron-Chromium-
Nickel, Corrosion Resistant, for Severe Service
A 747/A 747M Specification for Steel Castings, Stainless,
Precipitation Hardening
A 751 Test Methods, Practices, and Terminology for
Chemical Analysis of Steel Products
A 800/A 800M Practice for Steel Casting, Austenitic Alloy,
Estimating Ferrite Content Thereof
A 802/A 802M Practice for Steel Castings, Surface Accep-
tance Standards, Visual Examination
A 890/A 890M Specification for Castings, Iron-Chromium-
Nickel-Molybdenum Corrosion-Resistant, Duplex
(Austenitic/Ferritic) for General Application
A 915/A 915M Specification for Steel Castings, Carbon,
and Alloy, Chemical Requirements Similar to Standard
Wrought Grades
A 941 Terminology Relating to Steel, Stainless Steel, Re-
lated Alloys, and Ferroalloys
A 958 Specification for Steel Castings, Carbon and Alloy,
with Tensile Requirements, Chemical Requirements Simi-
lar to Standard Wrought Grades
A 967 Specification for Chemical Passivation Treatments
for Stainless Steel Parts
A 991/A 991M Test Method for Conducting Temperature
Uniformity Surveys of Furnaces Used to Heat Treat Steel
Products
A 1002 Specification for Castings, Nickel-Aluminum Or-
dered Alloy
E94 Guide for Radiographic Examination
E 125 Reference Photographs for Magnetic Particle Indica-
tions on Ferrous Castings
E 165 Test Method for Liquid Penetrant Examination
E 186 Reference Radiographs for Heavy-Walled (2 to 412-
in. [51 to 114-mm]) Steel Castings
E 280 Reference Radiographs for Heavy-Walled (412 to
12-in. [114 to 305-mm]) Steel Castings
E 340 Test Method for Macroetching Metals and Alloys
E 353 Test Methods for Chemical Analysis of Stainless,
Heat-Resisting, Maraging, and Other Similar Chromium-
Nickel-Iron Alloys
E 354 Test Methods for Chemical Analysis of High-
Temperature, Electrical, Magnetic, and Other Similar Iron,
Nickel, and Cobalt Alloys
E 446 Reference Radiographs for Steel Castings Up to 2 in.
[51 mm] in Thickness
E 709 Guide for Magnetic Particle Examination
3. Terminology
3.1 Definitions:
3.1.1 The definitions in Test Methods and Definitions
A 370, Test Methods, Practices, and Terminology A 751, and
Terminology A 941 are applicable to this specification and
those listed in
1.1.
3.1.2 test coupon, n—the part from which the test specimen
will be extracted.
3.1.3 test specimen, n—the part that will be acted upon in a
test.
4. Materials and Manufacture
4.1 Melting Process—The steel shall be made by open-
hearth or electric furnace process with or without separate
refining, such as argon-oxygen-decarburization (AOD), unless
otherwise specified in the individual specification.
4.2 Heat Treatment:
4.2.1 Castings shall be heat treated in the working zone of a
furnace that has been surveyed in accordance with Test Method
A 991/A 991M.
4.2.2 When castings are heat treated at temperatures above
2000°F [1100°C], then the working zone shall have been
established by a survey performed at not more than 25°F
[15°C] below nor more than 200°F [110°C] above the mini-
mum heat treatment temperature specified for the grade. If a
minimum heat treatment temperature is not specified for the
grade, then the survey temperature shall be not more than 50°F
[30°C] below nor more than 175°F [100°C] above the furnace
set point used.
4.2.3 The maximum variation in measured temperature as
determined by the difference between the highest temperature
and the lowest temperature shall be as agreed between the
purchaser and producer except that during production heat
treatment, no portion of the furnace shall be below the
minimum specified temperature nor above the maximum
specified temperature for the grade being processed.
5. Chemical Composition
5.1 Chemical Analysis—Chemical analysis of materials
covered by this specification shall be in accordance with Test
Methods, Practices, and Terminology
A 751.
5.2 Heat Analysis—An analysis of each heat shall be made
by the manufacturer to determine the percentages of the
elements specified in the individual specification for the grade
being poured. The analysis shall be made from a test sample
preferably taken during the pouring of the heat. When drillings
are used, they shall be taken not less than
1
⁄
4
in. [6.4 mm]
beneath the surface. The chemical composition thus deter-
mined shall conform to the requirements in the individual
specification for the grade being poured.
5.3 Product Analysis—A product analysis may be made by
the purchaser from material representing each heat, lot, or
casting. The analysis shall be made on representative material.
Samples for carbon analysis of carbon and alloy steel shall be
taken no closer than
1
⁄
4
in. [6 mm] to a cast surface, except that
castings too thin for this shall be analyzed on representative
material. The chemical composition thus determined shall meet
the requirements specified in the applicable specification for
the grade involved, or shall be subject to rejection by the
purchaser, except that the chemical composition determined for
carbon and low alloy steel castings may vary from the specified
limits by the amounts shown in
Table 1. The product analysis
tolerances of
Table 1 are not applicable as acceptance criteria
for heat analysis by the casting manufacturer. When comparing
product and heat analysis for other than carbon and low alloy
steels, the reproducibility Data R
2
, in Test Methods E 353 or
E 354, as applicable, shall be taken into consideration.
A 781/A 781M – 06
2
Copyright ASTM International
Provided by IHS under license with ASTM
No reproduction or networking permitted without license from IHS
--`,,```,,,,````-`-`,,`,,`,`,,`---