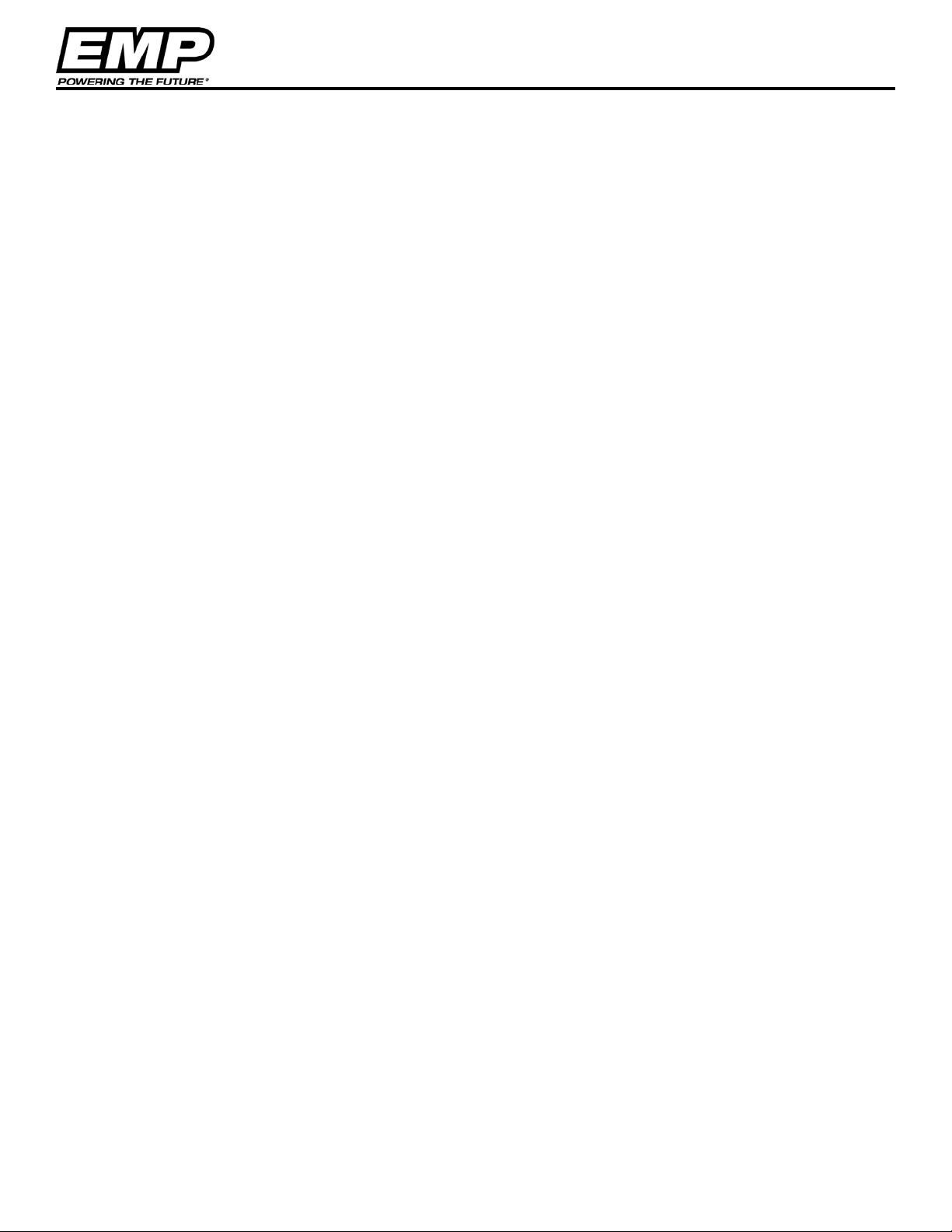
Table of Contents
Table of Contents
Product Overview .................................................................................................................................. 2
Table of Contents .................................................................................................................................. 3
Safety .................................................................................................................................................... 4
Warnings, Cautions & Notes ............................................................................................................. 4
Product Safety Warnings ................................................................................................................... 4
Communication Requirements .............................................................................................................. 5
Motor Command Message .................................................................................................................... 6
Motor On/Off/Direction....................................................................................................................... 6
Power-Hold ........................................................................................................................................ 6
Motor Speed ...................................................................................................................................... 7
Message Layout ................................................................................................................................ 8
Examples ........................................................................................................................................... 9
Motor Status Message ........................................................................................................................ 10
Motor Direction Status ..................................................................................................................... 10
Motor Controller Status.................................................................................................................... 10
Measured Motor Speed (RPM) ........................................................................................................ 10
Measured Motor Controller Temperature ........................................................................................ 10
Measured Motor Power ................................................................................................................... 10
Measured Percent Motor Speed ...................................................................................................... 10
Message Layout .............................................................................................................................. 11
Examples ......................................................................................................................................... 12
Use of Controller Status for Troubleshooting ................................................................................... 12
Controller State Message (CM20 Only) .............................................................................................. 13
Control State ................................................................................................................................... 13
Measured External Temperature ..................................................................................................... 13
Message Layout .............................................................................................................................. 14
Examples ......................................................................................................................................... 15
Alternate Command and Status Message .......................................................................................... 16
CAN Addressing ................................................................................................................................. 17
Resistor Addressing ........................................................................................................................ 17
Resistor Wiring ................................................................................................................................ 18
Diagnostics ......................................................................................................................................... 18
© 2013 EMP, Inc.
3