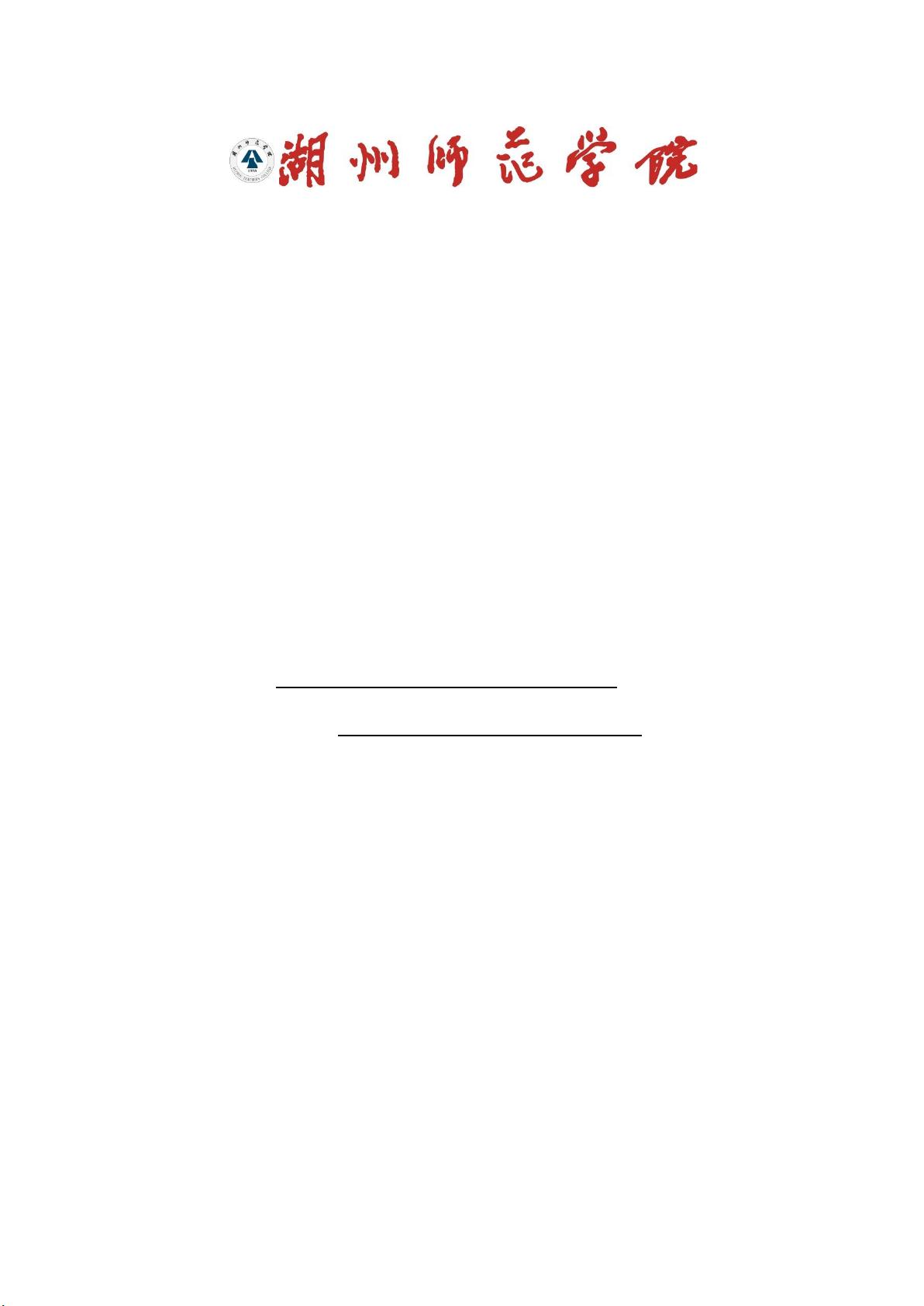
G. Seliger et al. (eds.), Advances in Sustainable Manufacturing: Proceedings of the 8th Global Conference 149
on Sustainable Manufacturing, DOI 10.1007/978-3-642-20183-7_22, © Springer-Verlag Berlin Heidelberg 2011
Methodology for High Accuracy Installation of Sustainable Jigs and Fixtures
J. Jamshidi, P.G. Maropoulos
Department of Mechanical Engineering, University of Bath, UK
Abstract
The ability to accurately measure the components of jigs and fixtures during their installation determines the
state of their precision, especially for large size products and applications. This matter is crucial in mass
customisation where small batches of products and components with high variety in design are manufactured.
Product quality should be in harmony with rapid changeover philosophy as compromising quality for speed is
not forgivable for sensitive components and assemblies such as those seen in the aerospace industry. It is
necessary for the installation of the jigs and fixtures to be highly accurate in order to minimise the use of
tolerance budget due to variations in jigs and fixture positioning. Major overhead costs for jigs and fixtures
particularly in the aerospace industry led to the development of the concept of flexible and reconfigurable jigs
and fixtures. Reusability of reconfigurable jigs and fixtures makes them attractive for sustainable solutions as
their components can be reused for several variant of a product or assembly. The main drawbacks of this type
of jigs and fixtures have been their poor accuracy and reliability. In this paper accurate positioning of the key
components of sustainable jigs and fixtures is investigated. The factors affecting the performance of the jigs
and fixtures are reviewed from the installation stage. The paper introduces a methodology for minimising
uncertainties in positioning of the holds and clamps for flexible jigs and fixtures.
Keywords:
Sustainable Jig, Jig installation, Calibration Uncertainty, Jig Monitoring, Metrology, Reusable Jig
1 INTRODUCTION
Factors such as quality and reliability have long converted to
implicit characteristics of the new products. Recent market
trends have forced manufacturing industries to move towards
mass customisation in their products and service range.
Increased variation in the design of new products is followed
by a second wave of variation with higher amplitude at
subassemblies and component level.
State of the art manufacturing systems and technologies
have provided more flexibility, enabling designers to think
more freely. For instance new large volume measurement
systems, developed in the past few years, are capable of
measuring several decametre distances. Such technologies
facilitate the verification of large size components that used to
be manufactured from several assembled components.
The manufacturing of large size products requires specialist
jigs and fixtures in order for their components to be held in the
desired orientation during build and assembly. This requires
major overhead cost that can only be justified by mass
production in some cases or otherwise the cost of finished
products can be very high. This issue contradicts with the
market trends where customers are constantly looking for
higher value for their money. In a typical product the variation
in the product creates a more sustainable business as it can
fulfil the needs of a relatively larger market.
Flexible and reconfigurable jigs and fixture that can be formed
in different shapes to support different variation of products is
a key solution for the above challenges. The concept of
flexible jig existed for several years in the research domain
[1]. However, they are not fully utilised to a great extent in
real production facilities especially for large size product
manufacturers, such as aerospace. This is due to the
challenges related to their initial installation, poor calibration,
and repeatability that often exceed the tolerance requirement.
The manufacturing of these jigs and fixtures from high quality
key components as well as their integration with large volume
metrology systems can reduce the above limitations.
This paper covers metrology issues related to the installation
and calibration of flexible jigs and fixtures as well as their
monitoring during service.
2 RELATED WORK
2.1 Manufacturing and assembly of large scale parts
Typically prior to precision manufacturing of mechanical parts
it is essential to move the raw material to the machine bench,
proceed with rough cutting then fine alignment and clamping.
At this stage the part is ready for machining of its high
precision key features. However, this is not always possible
for large size and/or heavy components. Large scale products
refer to those with components that are not economically
possible to handle or move around in the factory for
fabrication and assembly purposes [2]. The manufacturing
and assembly processes of these parts encompass
movement of the machines and systems to the desired
location and orientation with respect to these parts. Such
parts are normally held in their positions using large size jigs
and fixtures. If these parts are produced in small batch sizes
that is the case for aerospace industries, high overhead cost
per product will occur. There have been many attempts to
design and manufacture jigs and fixtures so that they can
hold a number of variants of components [3, 4]. However, this
approach is not feasible for parts with sensitive or key
features due to their high accuracy requirements.