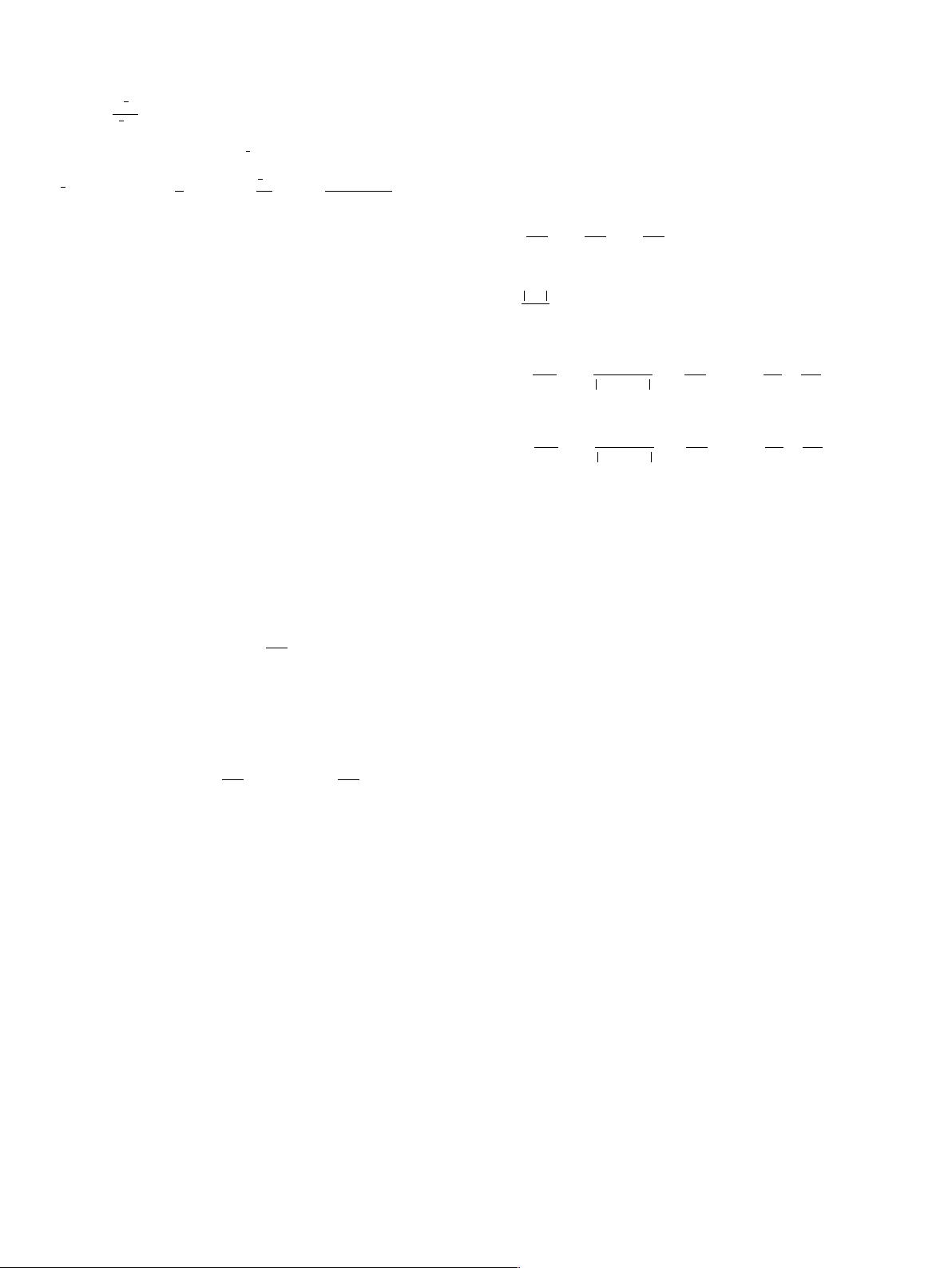
∑
=
⎛
⎝
⎜
∆
ε
ε
pl
f
pl
(4)
Where the plastic failure strain
ε
)
f
pl
is given by
⎜⎟
⎜⎟
=
⎡
⎣
⎢
+
⎛
⎝
⎞
⎠
⎤
⎦
⎥
⎡
⎣
⎢
+
⎛
⎝
⎞
⎠
⎤
⎦
⎥
⎡
⎣
⎢
+
−
−
εddexpd
p
q
d
ε
ε
d
TT
TT
1ln
1
()
()
f
pl
pl
m room
12 3 4
0
5
room
(5)
In Eq. (5), the first term takes care of pressure dependence and the
second term accounts for strain rate dependence. The third term is used
to accommodate the dependence on temperature. Constants d
1,
d
2
, d
3
,
d
4
and d
5
are the failure parameters which are determined experi-
mentally. When damage parameter
ω
)
is 1 for an element that parti-
cular element is deleted in the simulation. The Johnson-Cook model
used in this work is currently available in the Abaqus/Explicit material
model library for both shell and solid elements.
Al-6061 (aluminium) and St-37(steel) are the metallic materials
used for the material plates. Material properties of Johnson Cook model
for Al and steel is given in appendices in Tables A.1 and A.2, at the end
of the paper.
2.2.2. Johnson-Holmquist model for ceramics
Generally, ceramic materials are brittle in nature. They have high
compressive strength but low tensile strength and tend to exhibit pro-
gressive damage under compressive load due to the growth of micro
fractures. The Johnson-Holmquist material model (JH-2) [20] with
damage evolution is useful for modeling failure in brittle materials
subjected to large pressures and high strain rates and has been used in
this work. As per JH-2 model, the normalized equivalent stress is
evaluated as,
=− −
σDσσ
*
*
(
**
iif
(6)
The stresses in Eq. (6) are normalized to equivalent stress at Hu-
goniot Elastic Limit (HEL) i.e.
=
*
σ
σ
HEL
.
i
and
f
are normalized in-
tact and fractured equivalent stress respectively and D is damage
(0 < D < 1). Values of both these stresses are given as
=+ +
AP T C ε
*
(
**
)(1 ln
*
i
N
(7)
=+
BP C ε
*
(
*
)(1 ln
*
)
f
M
(8)
*
is normalized dimensionless pressure through Hugoniot Elastic
Limit and is defined as
=
*
P
P
HEL
. Similarly
=T
*
T
P
HEL
is the normalized
maximum tensile fracture strength.
T
tends to zero as
D
approaches 1.
Additional material constants
ABNC
,, ,,
are determined through
experiments. The damage for fracture is accumulated in a manner si-
milar to that used in Johnson Cook fracture model and it is expressed as
∑
=∆Dεε/
p
f
(9)
∆ε
p
is the equivalent plastic strain increment during a cycle of in-
tegration and
ε
f
=f(P) is the plastic strain to fracture under constant
pressure. When D is 1 for an element that particular element is deleted
in the simulation.
Silicon carbide is used as the ceramic material. All the essential
parameter values of silicon carbide are mentioned in the input file. The
properties which are used for silicon carbide (ceramic) are given in
Table A.3 in appendices.
2.2.3. Hashin 3-D and Puck criterion for composite materials
Composite materials are processed by stacking layers of lamina
which are made of fiber and matrix on top of each other to get desired
thickness. Fiber acts as a strength bearing member while matrix keep
them together. Therefore failure of composite structures is dictated by
the failure behavior of fiber and matrix. Various theories have been
proposed to accurately predict the failure of composite structures [23].
Among these, the Hashin 3D and Puck criterion which predict the
failure of unidirectional, transversely isotropic composite material are
phenomenologically accurate and the predicted values are close to ex-
perimental observations [24]. Each mode of failure is treated in-
dependently in these theories. In the FEM simulations performed here,
Hashin 3D failure model is used for fiber and Puck failure criterion is
used for matrix. The failure of composite materials is governed by the
following four failure criterion,
Equation for Tensile fiber failure if
rf
> 1 where
⎜⎟⎜⎟⎜⎟
=
⎛
⎝
⎞
⎠
+
⎛
⎝
⎞
⎠
+
⎛
⎝
⎞
⎠
rft
σ
ft
σ
f
σ
f
11
1
12
12
13
13
22
(10)
Equation for Compressive fiber failure if
rf
> 1 where
=rfc
σ
fc
11
1
(11)
Equation for Tensile matrix failure if
rmt
> 1 where
⎜⎟⎜ ⎟⎜⎟ ⎜
=
⎛
⎝
⎞
⎠
+
⎛
⎝
×
⎞
⎠
+
⎛
⎝
⎞
⎠
+
⎛
⎝
+
rmt
σ
ft
σ
ft fc
σ
f
σ
ft fc
11
21
22
22
12
12
22
1
2
1
2
2
2
2
(12)
Equation for Compressive matrix failure
rmc
> 1 where
⎜⎟⎜ ⎟⎜⎟ ⎜
=
⎛
⎝
⎞
⎠
+
⎛
⎝
×
⎞
⎠
+
⎛
⎝
⎞
⎠
+
⎛
⎝
+
rmc
σ
ft
σ
ft fc
σ
f
σ
ft fc
11
21
22
22
12
12
22
1
2
1
2
2
2
2
(13)
Where, f
it
denotes the allowable tensile strength in respective directions
(i = 1, 2, 3) and f
ic
denotes allowable compressive strength in respective
direction (i = 1, 2, 3). The values of different material parameter used
here are given in Table A.4 in appendices.
The above mentioned failure crit eria also govern the damage in-
itiation in composite layer and are available in Abaqus/Explicit.
However, these can be use d only with p lane formulation i.e. plane
stress, s hell, continuum shell and membrane elements. Even though, it
is possible to perform impact simu lations with thes e elements b ut to
have a standard comparison, the composite plate is modeled with 3D
elements by us ing user defin ed material model VUMAT in Abaqus si-
mulations. Initially in the impact simulat ions at t =0,thecomposite
is assumed to be linear elastic and its deformation behavior is gov-
erned by Eqs. (A .1) and (A.2).Oncethedamageinitiates(asperEqs.
(10)–(13)), the stiffness degrades and the el astic constants are updated
as per Eqs. (A.5)– (A.15). The modeling strategy used here is in line
with [28].
2.3. Post processing
The simulation time in all the FEM calculations kept fixed at 0.1 ms.
As the impactor is rigid, initial energy imparted to the impactor in the
form of kinetic energy (initial velocity of the impactor) is utilized in
deformation and fracture of the deformable plate. So, as impactor pe-
netrates through the thickness of plate, defined as depth of penetration
(DOP), its kinetic energy will keep on reducing and will approach to
zero. The initial velocity of impactor is increased gradually and the
response of various plates with different material combinations is stu-
died. To have a standard comparison, we define the critical failure
velocity V
cf
, the velocity at which the impactor is just able to penetrate
through the thickness of single/multilayer plate i.e. at
≤
V
c
, the DOP
will be either less than or equal to the total thickness of the plate. For
velocities higher than V
cf
, the impactor will pass through the plate and
as a result the calculated DOP will be greater than total plate thickness
which has no physical significance.
2.4. Validation
In order to check the accuracy and predicting capability of proposed
FE modeling approach, the results of FEM simulations is confronted
with experimental data available in the literature. Fig. 4 compares the
residual velocity as a function of impact velocity obtained from current
FEM simulations and experimental data reported in [26] for the plate
A. Sharma et al.
Thin-Walled Structures 126 (2018) 193–204
196